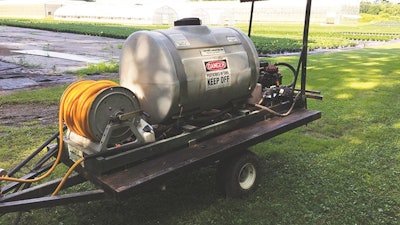
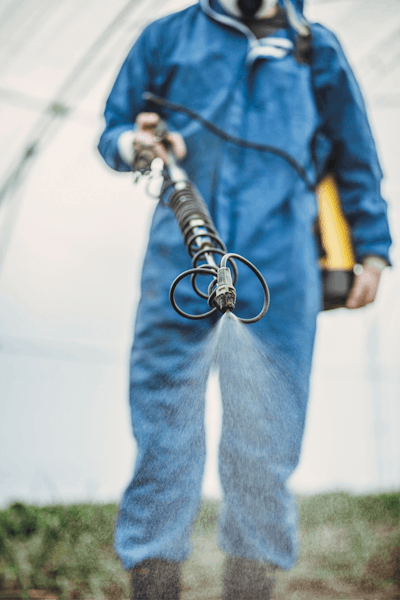
The actual application of pesticides is the most difficult task to perform in any integrated pest management (IPM) program. Even when the applicator has safe, reliable products and equipment, applying pesticides—especially if done incorrectly—is fraught with risk to workers, plants and the environment.
So how do you find reliable pesticide application information? Most likely you’ve relied on trial and error, advice from colleagues, the internet, or from pesticide producers. Are you satisfied with that information? If you’re like me, you’ve been tempted by silver bullets before: one mythical solution that will kill all the bugs and spores once and for all—something that will take the “management” out of pest management. After a few years, however, most of us learn that Jeff Goldblum’s character in the movie “Jurassic Park” was right and “life, uh, finds a way.” In other words, pests will always be with us. Unlike the rest of U.S. agricultural production, cannabis has not benefited from the U.S. Cooperative State Research, Education and Extension Service that is responsible for disseminating unbiased information from university testing to growers.
Extension specialists don’t just serve farmers and 4-H programs, but also nursery, orchard, hydroponic and greenhouse growers. Luckily for Cannabis Business Times readers, some of the first articles written by extension specialists related to cannabis (other than hemp) have been published in this magazine. Dr. Brian Whipker and Dr. Brian Jackson of North Carolina State University have written on plant nutrition, and Dr. Raymond Cloyd of Kansas State University reported on using biological controls in greenhouses. They’ve also spoken at the Cannabis Conference.
This should not be taken for granted. Many of their counterparts are not allowed to contribute information to our industry. If your company touts a commitment to implementing commercial agriculture or horticulture methods, these articles should be required reading for your staff, as the partnership between U.S. industry and academia is what created that methodology in the first place.
I’ve relied on the insect control advice of Dr. Cloyd for decades. Likewise, I’ve been fortunate to have plant pathologists provide similar advice for disease control measures and university specialists on pesticide safety and environmental protection. Here are 17 tips for proper pesticide applications based on expert advice and information my pesticide applicator teams and I have implemented in our greenhouses and grow rooms during the past three decades.
1. Use products compatible with your biological controls. Several producers of beneficial insects have “side effects” links on their websites that allow you to determine if the product you are going to apply will hurt or kill your beneficial insects. From the menus, simply click on a pesticide and then on the beneficial insects you have released or plan on releasing. The app then displays toxicity information for each life stage of the beneficial insect. These are incredibly useful tools, and using more than one app improves the scope of your search. Follow this link for an example: bit.ly/Koppert-side-effects.
2. Read and follow the label. After you’ve read a couple of these, you’ll be able to get through the legalese quickly and discover some very important information that will improve the effectiveness of these products or prevent plant damage. Go online and print PDF versions of these. Make a binder of them and their related Safety Data Sheets, highlight pertinent information and keep them at your fingertips.
3. Use reverse osmosis water to make your spray solutions. Poor-quality water will render some pesticides ineffective very quickly. For example, many pesticides lose effectiveness above pH 7. If you don’t have purified water available, test your final solution and adjust pH to what the label recommends. When in doubt, adjust to a range of pH 6 to 7.
4. Focus. Whether it be for insect or disease control, focusing on adequate spray coverage of all leaf surfaces is key. This doesn’t mean overapplying and wasting product but using the proper techniques and tools that allow the applicator to focus on this goal. The work environment plays a part in focus, as well. In my experience, the best way to obtain excellent coverage is to provide your applicator a comfortable, unhurried environment to work in. We changed our application time to early morning to avoid the heat that builds up in a greenhouse by day’s end and to avoid the fatigue of spraying after a full day of tasks. We make sure personal protective equipment (PPE), including boots, gloves and masks fit well, and keep spares of all PPE so clean, unbroken items are always handy to use. We stopped using lab goggles and moved to approved face shields that would not fog up and reduce vision, and to light-weight, disposable lab coats.
5. Bring a co-pilot. Whether using a small 2-gallon sprayer or a large “war wagon” hydraulic pump sprayer with a reel of hose to lug around, it really helps the applicator concentrate if a second person can move things out of the way and watch for tripping hazards. He or she can make sure doors are locked and signs are posted for restricted access and help with the cleanup. Remember, this assistant needs to wear the same PPE as the applicator.

6. Consider a cold fogger. A cold fogger is an ultra-low volume (ULV) sprayer that ejects a 10-foot to 12-foot stream of spray droplets about 25 microns or less in diameter. These fog droplets penetrate dense foliage and adhere to the undersides of the leaves. They also persist in air longer than a liquid spray, so insects are exposed for a longer period. The cold foggers are available as handheld or fixed-position units on a wheeled dolly. I’ve used a fixed-position cold fogger with a timer, so it can come on at night when the room is locked and empty of employees, reducing worker exposure and labor. ULV sprayers come in multiple sizes to match the size of the room. They use only a fraction of the volume of spray solution—about 2 liters for a small room—but the amount of product you mix into that 2 liters of water is the same as you would mix for a normal hydraulic sprayer, so it’s very concentrated. Because of this, do not direct the fog directly at plants. If you are applying microbial products, always use a cold fogger rather than a thermal fogger, which heats up the spray solution to a temperature that would kill many beneficial fungi. Check with the manufacturer to determine which products work best in cold foggers, as some formulations may clog or damage the nozzle. I’d recommend paying a little extra for a stainless-steel nozzle upgrade. My technician at Purdue University attached a portable cold fogger to a wheeled cart so he could move it into different positions and adjust the height of the fog stream.
7. Use cold foggers in combination with circulation fans. Turn off the circulation fans for the first 30 minutes of fog application. Then, leave them on for at least two hours following application. This will improve fog penetration into dense foliage.
8. Understand the drawbacks to cold fogging. Cold foggers may pose a greater risk to workers because the fog droplets can be inhaled more easily. Fog is almost invisible, so lock the room and keep workers away. You may need to clear adjacent areas if the room is not tightly sealed. Cold fogging takes much more time to distribute the solution—as much as two hours for 2 liters for a fixed-position unit. As stated above, not all pesticides are suitable for cold foggers. Lastly, you can’t choose to just spray a small area—it’s the whole room or nothing at all.
9. Let your environmental control system assist you. Many environmental control systems (ECSs) have pesticide programming features that allow you to change the environment before, during and after the application. For example, the circulation fans during a cold-fogging application can be programmed to turn off and on automatically. Then, after a proper number of hours, the greenhouse can be ventilated so that it is ready to be entered when staff returns. For spray applications, the temperature of the room can be lowered while the sprayer is inside to keep them comfortable as they focus on coverage. The convenience of this programming is that it is timer-based, so it will return to normal setpoints without your input.
10. High temperatures require more frequent sprays. Just as high temperatures speed the growth rates of plants, insects also complete their life cycles faster. Frequency of sprays will need to increase during warmer greenhouse temperatures, or if you increase the temperatures of your indoor grow room. In my greenhouses, weekly sprays suffice during most of the year, but in the heat of summer we learned we needed to spray every five days.
11. High temperatures can lead to spray damage. Spray applications that are perfectly safe and effective in moderate temperatures may cause phytotoxicity during extreme temperatures of 85 degrees to 90 degrees Fahrenheit. This is particularly true with oil sprays.
12. Avoid multiple sprays of insecticidal soap. If you are permitted to use insecticidal soap in your state, avoid more than two applications to a crop. The soap accumulates on leaf surfaces and causes a toxic response. Like all phytotoxic responses, some cultivars are more affected than others.
13. Don't spray and pray. Conduct phytotoxicity tests. Test any pesticide you’ve not used before on a small set of plants of each cultivar. If you are in a hurry, mix up a small amount in a pump sprayer and spray two to three plants of each cultivar, flagging the plants as you go. Wait for three to five days to see if the product causes damage. For a more formal approach, set aside nine plants of each cultivar and spray three with water as a control, three with the product at a label’s low rate and three with the high rate.
14. Consider a fume hood for your mixing area. If you’re designing a facility, consider installing a fume hood, like those used in tissue culture labs, in your pesticide storage area. It provides a safe place to handle wettable powders and liquid concentrates and also will draw away any bad odors from the storage room if you let it run continuously.
15. Mix your spray solutions thoroughly. A commercial mixing agitator will ensure thorough mixing of concentrates into a large volume sprayer. In a pinch, you can devise your own. We rigged a metal mixing paddle into the drill-bit hole of a standard power drill with a locking activation switch. This was much cheaper and lighter than the commercial agitator. Let it spin on a low speed while mixing pesticides in the spray tank.
16. Go lightly on those adjuvants. You can mix substances called adjuvants into a spray tank to improve pesticide performance. Adjuvants include spreader stickers, which help solutions stick to leaves, and surfactants that help the solution spread out into a fine film on a leaf, effectively increasing coverage. There are other types of adjuvants on the market, and there are several “synergists,” as well, that are supposed to improve the effectiveness of pesticides. The problem with adjuvants and synergists is that they can cause damage to leaves and flowers more readily than the active ingredient of the pesticide. In fact, most phytotoxic responses from sprays are not from the active ingredient but the inactive ingredients the producer used in the formulation. Many commercial pesticides already have these adjuvants in them in proper amounts. Adding more can cause an overdose. Therefore, only apply surfactants if the label suggests it would be helpful or if you’ve done your own phytotoxicity tests.
17. Get licensed. Commercial greenhouses, nurseries, farms and orchards are required to abide by the Worker Protection Standard (WPS), enforced by the U.S. Environmental Protection Agency. This law requires growers to provide training and information to workers at agriculture facilities about the dangers of pesticides and of heat stress. It came about after many tragic accidents, such as migrant workers using empty pesticide containers as water bottles, which is why pesticide warning labels are bilingual. All workers must have awareness training, and all applicators must be licensed in application safety, pesticide knowledge and environmental safeguards. Testing is required for the license and recertification every few years, depending on the state. Though the WPS is not apparently enforced in the cannabis industry, I believe it will become mandatory once the crop is federally legalized, because the program is well established. You can receive training and testing at state land grant universities. See the WPS Guide here: bit.ly/WPS-guide for more information.