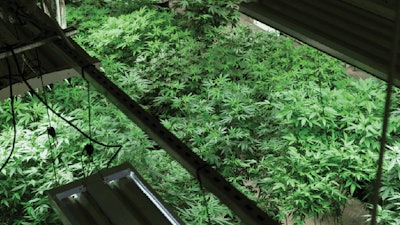
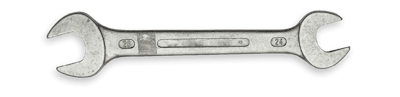
Cannabis production facilities need to be well-oiled machines to produce consistent yields of expected quality. The systems and equipment that provide optimal environments for plant growth and development operate in dynamic conditions and are put under stress day in and day out as they support production. These systems’ components will degrade over time, but growers can extend their equipment’s longevity by conducting proper maintenance.
Operators who identify and mitigate sub-optimal system performance can save money by reducing operating expenses, and using commissioning processes to verify environmental control systems can help keep up with facility demands. (For more on systems commissioning, see the November 2020 CBT column from RII here.) Furthermore, creating and implementing operations and maintenance (O&M) plans for your cannabis facility can help avoid equipment downtime from malfunctions and failures.
Live an Easier Life
Horticultural environments are tough on environmental control systems. High-output light fixtures (whether light-emitting diodes (LEDs) or high-intensity discharge (HID)) are used for numerous hours a day, and cooling and dehumidification systems continuously deal with humid air at hot temperatures. Also, plants are constantly changing as they grow taller, as their transpiration rates fluctuate, and as target environmental conditions vary to suit the different stages of plant development.
Regular maintenance can have many financial and operational benefits. When HVAC equipment is pushed to capacity limits or is run hard continuously without downtime, components wear down and systems perform below rated efficiency. For example, short-cycling happens when compressors in HVAC equipment turn on and off more than usual, increasing energy consumption and causing undue wear and tear on equipment. Short-cycling can be caused by low refrigerant in cooling systems and can be avoided with preventive maintenance activities like maintaining refrigerant charge and checking for refrigerant leaks.
Before creating an effective maintenance plan for a facility, first conduct a system audit to gather information on all environmental control systems and equipment serving cultivation processes. Review design drawings of the building that list major systems and equipment, their technical specifications, and associated design conditions. The components installed in the field may not be exactly the same as what is shown on paper, so check out equipment in the field and inspect information found on the device’s nameplate. Collect important details such as: year installed; manufacturer make, model, and serial number; rated capacity; rated efficiency; electrical information like voltage (V), amperage (A, amps), frequency (Hz or cycles per second), and power in watts (W) or horsepower (HP); and certifications.
Check on mission-critical lighting, HVAC, and fertigation systems for periodic tune-ups to extend the life of some of the most expensive equipment in cultivation facilities while also reducing energy and water bills.
Operators should recommission systems annually to validate performance and to understand how systems meet targets and respond to equipment failures. Run lighting controls systems through functional performance tests to ensure schedules, flux targets, and dimming sequences of operation are implemented as expected. Consider how lights should automatically respond if HVAC systems go down; if cooling systems fail, should lights ramp down or turn off?
In greenhouses, test how light deprivation, shade curtain, energy screens, and lighting control systems respond and how systems should operate when temperatures get too hot or too cold.
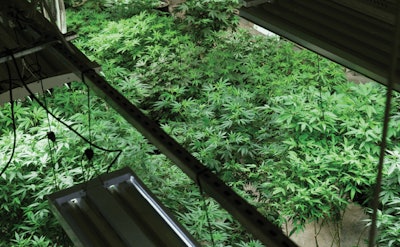
Document the Plan
Using design drawings and information collected during your system audit, download equipment manuals for systems serving cultivation environments and check out the manufacturer’s recommended maintenance activities. To start an operations and maintenance plan, create a document that describes every critical system, its major components, its sequence of operations, and essential maintenance tasks. This resource trains and guides facility staff on all systems, their expected performance, and any maintenance protocols to follow.
Assess core environmental control systems and determine how parallel equipment will be rotated to maintain even wear. Lead and standby equipment installed in parallel, like two pumps in a chilled water system loop, can take turns running for a set period of time. Track both lifetime runtime and staging runtime and decide how often devices should rotate. Lifetime runtime describes cumulative runtime since equipment start-up. American Society of Heating, Refrigerating and Air-Conditioning Engineers (ASHRAE) guidelines compare staging runtime to the trip setting on an odometer: it’s an operator-resettable runtime point that stores cumulative runtime since the last reset.
When drafting the maintenance plan, determine how backup equipment will serve when primary systems need to be taken down for maintenance, or if systems fail. Some especially critical systems may need redundant equipment primed and ready to step in if a worst-case scenario occurs. In these cases, ensure these systems’ perform in emergencies by planning for their routine maintenance alongside equipment that will see daily duty. Some growers run automatic routine testing of generators on a weekly basis, while others work with their controls’ vendor technicians to run functional tests twice a year.
Decide how frequently environmental sensors should record data and where that data should be logged, as multiple years of data can support year-over-year comparisons. The more often sensors take readings, the more data your system has to retain. While readings logged at frequent intervals like one or five minutes tell granular stories about environmental conditions in grow rooms, they also require more space for data storage. Readings at fifteen minutes take up less space, but may not capture the dynamics at work in grow rooms. Additionally, local data loggers can be limited by their storage capacity. Some growers store data redundantly both on- and off-site, keeping records for two weeks before replicating them in the cloud or to an external hard drive.
Maintain for Equipment Longevity
Because of year-round growing, maintenance should be integrated within production schedules since equipment runs continuously and facilities are never completely empty. Implement environmental control system maintenance on both a monthly and annual basis. Train staff to impart the importance of these periodic maintenance tasks:
Monthly Maintenance
1. Review historical trended data. Make data analysis an official step in the production cycle process. Review data collected by environmental control systems for each grow room at the end of each harvest to understand performance information. Set baselines to more quickly catch when your yields don’t meet expectations. Consider holding monthly team meetings to proactively build a culture around data that integrates controls and information systems with the day-to-day interactions of staff with the facility.
2. Sanitize after each grow cycle. When moving plants in and out of rooms, adhere to good manufacturing practices and clean rooms to ensure optimal product quality and safety. Mold and mildew thrive in hot and humid conditions, so HVAC system components like filters should be inspected and cleaned frequently with appropriate cleaning agents. Keep environmental sensors clean to ensure accurate readings; the U.S. Department of Energy reports that for every one degree of accuracy, an operation can save 3 to 5 percent on total energy costs.
3. Replace worn out components. Proactively replace damaged components so equipment performs at its best. When environmental control systems are equipped with components that function at typical efficiency, facilities use less energy and systems have greater longevity. Use O&M plans to describe critical components and visual indicators to use during routine inspections. For example, guide field inspections with an image or list of descriptive characteristics that flag components for replacement.
Annual Maintenance
4. Calibrate sensors. Sensors need to be maintained to achieve optimal environmental conditions. During commissioning, verify readings and calibrate sensors by comparing outputs with output from calibrated sensors that are otherwise stored and only used for the purpose of calibration. ASHRAE standard 90.1 requires new temperature sensors be calibrated for accuracy to ±2°F over the range of 40°F to 80°F. New humidity sensors should be accurate to ±5% over the range of 20% to 80% RH. Calibrate sensors annually as readings naturally drift and lose accuracy over time. How deeply control and optimization can be accomplished depends on the controls manufacturer.
5. Check for leaks in HVAC systems. All kinds of leaks drive up utility bills. When conducting environmental control systems recommissioning activities, use leak detection equipment to assess ductwork and piping for leaking air and refrigerant. Refrigerant leaks cause HVAC equipment to run harder and short-cycle, straining compressors and eventually causing equipment failure. Escaped refrigerants are also greenhouse gases and are a primary contributor to climate change. Also, conditioned air escaping from ducts wastes energy used for cooling and dehumidification, so be sure to seal leaky spots to save on both energy and money.
Cultivation facilities that produce cannabis year-round can maximize profits by ensuring the mission-critical systems serving plants are maintained to last and minimize downtime. Work with commissioning agents to build out O&M plans in design and construction to help prevent suboptimal system performance and guide operators to target their efforts when troubleshooting equipment problems.