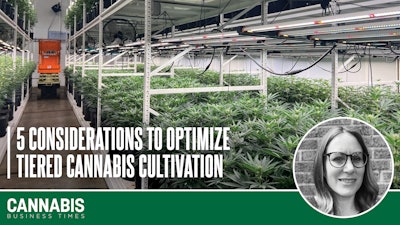
Vertical farms are indoor growing systems insulated from outdoor environments that utilize artificial light and controlled climate management to cultivate crops. Vertical farms often operate with hydroponic or aeroponic systems, but in some cases, soil or other substrates are used to support plants. Growing in tiers can optimize resource usage, particularly water and energy, as compared to layouts with larger footprints of the same canopy size. However, working at heights can limit access to caring for and monitoring crops, . putting a strain on labor efficiency. With good planning and effective personnel and equipment management, these challenges can be mitigated. Here are five considerations when managing workflows within tiered grows to optimize efficiency, safety and plant health.
1. Access
Plant access is a top obstacle in vertical grows that must be overcome to achieve overall labor efficiency. Some racks have removable custom scaffolding that insert between benches so that employees can walk easily on higher tiers, but this can be an expensive option depending on the size of your crop space and may not be realistic for three or more levels. Stools and step ladders can work for a second floor of canopy, but beyond that, access becomes more challenging. For three tiers and above, most cultivators use some form of mobile scaffolding combined with electric scissor lifts to provide worker access to higher tiers.
Mobile scaffolding, rolling, portable platforms similar to what is used for painting, can support two people comfortably and can be positioned very closely to plants. Employees need to step down from this type of scaffolding before moving it, so they aren’t efficient for tasks that require minimal time per plant such as scouting plants or applying foliar sprays. They can work well for slower-moving tasks like pruning. Consider the necessary storage space for this type of equipment.
Electric scissor lifts provide access to three tiers and higher, and most load limits allow two employees on the lift simultaneously. Electric scissor lifts can move forward or backward while raised, so this makes them an excellent tool for applying foliar sprays, pruning, scouting plants, applying trellis and harvesting.
We have found at the Galenas facility in Akron, Ohio, that two scissor lifts are adequate to manage 4,600 square feet of canopy across three tiers. This means that four cultivation employees can work on any tier at a given time.
One challenge when using lifts is moving plants or other materials on and off the platforms. There isn’t much more storage room other than for a tote or bucket, though some lifts have an extendable platform that can be used to accommodate additional tools and supplies. One helpful modification is to attach a pulley system that can raise or lower a bucket or tote, so that tools or plant material can be lowered down to an employee on the ground without having to lower the lift. This is very handy for harvesting plants. A large tote can be loaded with six to eight plants then lowered carefully down to employees on the ground to rack.
Certain tasks can be accomplished most effectively with two scissor lifts working in tandem, one on each side of the row. Applying or removing trellis netting often works best with a team on each side working together on the same bench. Certain cleaning processes may also require two lifts to complete tasks quickly.
2. Safety
Electric scissor lifts are relatively easy to operate and can allow employees to move fast enough to efficiently complete most tasks. They generally run eight to 10 hours on one overnight charge. Most employees pick up how to operate them quickly after training and initial use; however, they can be very dangerous if not used properly.
Whether working on a scissor lift, mobile platform or removable platform, working at heights requires additional safety considerations.
Scissor lifts can be outfitted with tool holsters, safety equipment, or PPE supplies to reduce the number of times employees have to climb up and down. Lift floors should be non-slip because many cultivation tasks involve water. Scissor lifts require firm, level floors away from hazards, guardrails in place to prevent fall accidents, and regular safety inspections.
3. Labor Management
Managing employee workflow in a vertical cultivation facility is exceptionally important. Shared equipment use combined with limited personnel access for higher tiers requires excellent task-planning. There are multiple task management apps that make workflow planning simple and successful. One option is workflow software that utilizes Kanban (Japanese for ‘signboard’) technology-a lean production system first utilized by Toyota in the 1940s. Kanban boards have been applied to IT and software and create project management systems that visualize workflow using virtual whiteboards to list and track task progress in a “To Do, Doing, Done” format.
These virtual boards can track progress and assign tasks, equipment and time limits to individual personnel. They can house categories such as “issues,” ‘inventory needs,” and ‘data points.” They work well for standard operating Procedures (SOPs,) training materials and safety guidance, plus pesticide mix rates, product labels, and safety data sheets (SDS) can be linked to the virtual board for quick reference. For a small- to moderate-sized staff, there are multiple free software options, though they may have limitations that paid versions do not.
Vertical grow rooms often contain large plant populations, so restricted entry intervals (REI) required after spraying pesticides can keep employees out of rooms for long periods. Planning around REIs is critical to labor assignments. Maintenance personnel may need to use lifts or production space, so good interdepartmental planning is necessary to keep teams moving and avoid delays because they are waiting for safe access or equipment. Occasionally urgent maintenance situations arise, and cultivation teams must be able to pivot.
Keep pest and disease management in mind when directing workflow. When employees move between rooms, they may also unknowingly transfer pests or microbial contaminants. Implementing preventive steps, such as requiring a change of clothes or PPE, handwashing, and bleach trays or sticky pads for footwear is important. If workers can’t be isolated and must access multiple spaces in the grow, a good strategy is to create personnel movement patterns from areas with younger plants toward those with older ones throughout the workday. Younger plants should be cleaner- free of pests and disease—than their older counterparts.
Task management for cultivation personnel is key to staying cost-efficient in the labor category. When workers walk in the door aware of their daily assignments, there is zero down time. Staggering shifts helps with managing access to equipment. Starting one shift two hours prior to the next can provide more time for equipment use throughout the day and across breaks. This also allows time for scouting plants and completing tasks that may be essential to the following shift, such as cutting trellis prior to a harvest, or applying a foliar spray so that the next team can work in the room after the restricted entry interval is over.
4. Scouting
Monitoring plants for quality issues is different in vertical formats. Plants on higher tiers cannot be readily observed, so it’s important to make sure that there is a well-planned strategy for detecting any issues that could affect quality or yield.
Scissor lifts and other access equipment are in high demand for other tasks in vertical farms, so it is best if scouting is outside of the primary production work shift. Scouts should be armed with all the tools necessary for their inspections—loupe, microscope camera, phone/tablet, marking stickers—before climbing onto a lift. And it’s critical to know exactly what checkpoints, which include plant health and facility issues, need to be assessed.
Plant checkpoints include wilting, signs of light or wind burn, physical plant damage, presentation of pests or disease, and herming (when a female plant grows male flowers). Facility issues include mechanical issues with lights, fans, or HVAC components, leaks, irrigation equipment failures, and operational problems with access equipment. It usually works best to have a specific checklist to refer to while performing crop room inspections.
A scout should note checkpoint location, percent of canopy affected, plant tag, and time/date. It’s great to upload pictures directly into crop inspection reports in workflow or IPM software. A color-coded sticker system is handy for various issues to alert other staff and avoid re-reporting, or to indicate that certain plants need to be handled with care. Scouting thoroughly and effectively keeps plants healthy, critical for crops in higher tiers that can go longer unseen, and offset shifts to reserve valuable access equipment time for production uses.
5. Genetic Selection
Managing the growth habits of cannabis crops in a vertical farm can present challenges. Some strains can stretch or elongate stems more than 300% of vegetative plant size when forced into the flowering cycle. These plants require different pruning methods, such as additional topping and training through trellis or other support. Even when plants are well supported, leggier cultivars can require additional hours, especially when growth becomes tangled in trellis netting or plants reach lights.
Topping a plant two or three times roughly two weeks apart during the vegetative cycle can help to keep plants at the appropriate final height for vertical formats while delivering the best yields of premium flower. Trialing various genetic varieties for individual systems often illuminates which cultivars produce best. Placing more compact plants on higher tiers can help to reduce labor, thus use of access equipment. Some cultivars may not be appropriate for stacked tiers, and shortened vegetative times are often essential in reducing total plant height and keeping all flower sites at optimal light levels.
Growing in vertical farms presents a new set of challenges, but close attention to equipment use, plant surveillance, and cultivar choice can greatly improve both quality and yield. Labor—one of the greatest costs in any business—can be optimized to significantly reduce costs in tiered grows, particularly when people are provided with the correct tools, training, and direction. Growing in the cube can substantially reduce resource and energy costs, and the associated workflow challenges of growing vertically can be solved with proper planning and personnel management.