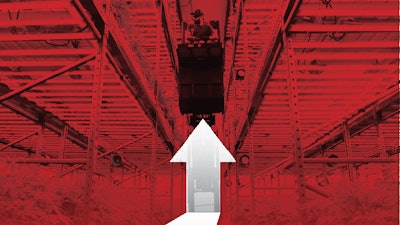
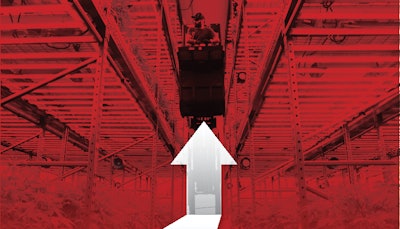
When cannabis is grown vertically, environmental controls are crucial tools for keeping consistent temperature, humidity, and airflow on all levels across the plant canopy. Microclimates will occur in multi-level grow rooms without careful design and sufficient control systems to keep them uniform.
Cultivation systems need to be fine-tuned to respond to changing and complex environmental conditions and ensure stacked crops experience optimized climates for maximum yields. It all starts with proper design.
Design and Equipment Considerations
Vertical growing systems for cannabis vary widely and can be two to five-plus levels tall. According to Cannabis Business Times’ 2021 “State of the Lighting Market” report, 37% of participants use vertical rack systems in vegetation, while 21% use tiered grows in flowering, with the highest number of cultivation companies growing on two levels.
The elevation diagrams above show how in flowering and propagation, vertical cultivation techniques can maximize canopy area for indoor farms.
During facility design, consider how staff will access each level in a vertical cultivation room and how each racking system tier should be laid out so employees or automated systems can effectively harvest the entire canopy. Consider how employees will reach into the center of each tier to access plants. Scissor lifts, for example, can be important tools to help employees monitor plants and signs of stress from environmental conditions. They must be operated properly by trained employees to ensure safety and compliance. (According to a 2016 “Hazard Alert” from the Occupational Safety and Health Administration (OSHA), the agency “investigated ten preventable fatalities and more than 20 preventable injuries resulting from a variety of incidents involving scissor lifts.”) Facilities with taller canopies may require staff to clip into harnesses connected to structural support, and there must be adequate floor space to position and stabilize lifts properly.
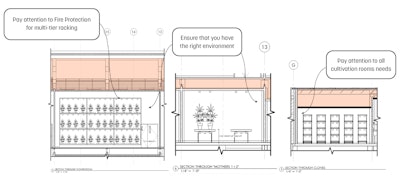
Climate Control Demands of Tiered Systems
Microclimates present challenges in cannabis facilities. Given that hot air rises, warmer air tends to move to the upper levels of racking systems. Without both strategic design and proper ventilation systems, this hot air can get stuck in cultivation rooms and cause plants on different tiers to experience different temperatures. This “stack effect” is a major contributor to microclimates in vertical grows.
To prevent trapped air, reserve 18 inches to 36 inches of headspace at the top of flowering rooms (which should be below a properly insulated ceiling). This clearance prevents the top tier from getting too hot. Consider locating cultivars that prefer warm and dry environments and require less-frequent care on upper levels.
Optimize room design for effective cultivation and harvest, and leave ample walkways for personnel and air mixing between racks.
Control Systems for Vertical Cultivation
Vertical cultivation can throw off target environmental conditions and how growers use zoning controls.
Airflow is the most critical element for maintaining consistent yields and optimal plant health in vertical cultivation. Account for early and late stages of plant growth in the room to track airflow patterns, as plants significantly change how air moves as they grow taller and leaves get bigger.
Rather than depending on HVAC ducting alone, ensure air is actively pulled into the racking systems. Avoid overly integrated airflow solutions that add ducting to the main HVAC systems and consider employing in-rack components to move and circulate air.
Choosing the right type of lighting in vertical racking systems for each grow room also is crucial to ensure the proper environment for optimal crop development and flower production.
Keep lighting, fertigation, and airflow zones together on integrated controllers. If possible, keep all zones on the same vertical plane, even though it is potentially inconvenient for installation. Ensure one or more sensor monitors and reports on zone conditions. Because it can be challenging to see all plants in racks, consider installing cameras to monitor plants up close.

Maximizing Productivity and Efficiency
Standard operating procedures for vertical cultivation spaces require adjusted plant care strategies. Resist “over-vegging,” or letting plants get too big before transitioning them to flowering. Keep plants and canopy density manageable because plants in upper tiers will inherently be monitored less often. Bushier plants can create more drastic microclimates, so decide on a topping and pruning strategy that maintains proper airflow. Choose cultivars that don’t need as much support and defoliation, as it is more challenging to work on plants in racks than on single-level tables.
Optimizing vertical operations to achieve forecasted yields can require unique designs and controls strategies so that these facilities can meet expectations for productivity. Vertical farms that mitigate stack effect and avoid microclimates can optimize for consistent cannabis yields and quality characteristics.
However, growers should set realistic expectations about what vertical setups can produce. A realistic range for performance is 50 to 80 grams per canopy square foot (gsf), according to Zartarian Engineering. One hundred gsf may be an overly optimistic goal because racked grows inherently yield less on a canopy area basis because the plants tend to be smaller, and the volume of the canopy of the flower-bearing area is smaller, too. Growers can budget 1 ounce (~30g) per cubic foot of vertical canopy.
While focusing on flower is essential, indoor cannabis cultivators can benefit from balancing efficiency with productivity. Consider what operational expenses and environmental impact are acceptable for a gram of product. Set key performance targets and benchmark actual facility performance to quantify year-over-year trends in key performance indicators (KPIs) for resources like energy, water, and emissions like solid waste and greenhouse gases.