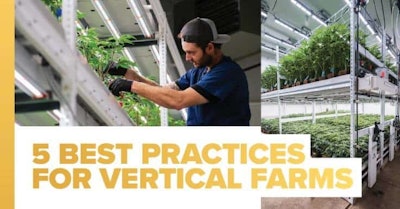

James Cunningham started growing cannabis indoors, on a single tiered surface under high pressure sodium (HPS) lights. The setup worked for more than a decade, but the advent of more efficient light-emitting diode (LED) lighting inspired him to rethink the setup at Fog City Farms.
“For a long time, LED had a bad reputation for underdeveloped flower growth,” recalls Cunningham, CEO of Fog City Farms, based in Santa Cruz, Calif. But then things changed. “We started to hear from a few different LED growers [who] were producing comparable yields and comparable quality flower to HPS.”
In 2017, citing the high cost of square footage for indoor space in Santa Cruz and advances in lighting technology, Cunningham transitioned to a two-tiered vertical system with LED lights for cannabis plants in the flower stage. In the vegetative growth stage, plants remain in a greenhouse where square footage is less expensive and lighting requirements are lower.
Cunningham credits the move with providing the space he needed to develop the Fog City Farms brand and sustain its wholesale operation.
“When you go vertical, you’re producing half the heat with [LED lights] with the same amount of cooling,” he explains. “What we used to have to build a two-story building for, now we can throw up some racks and make use of our cubic footage rather than [our] square footage.” In other words, since Fog City is already cooling the air above the canopy, it leveraged LEDs’ lower heat loads to “grow up.”
Matt LaBrier also adopted a vertical strategy to maximize the cubic footage when designing the Proper Cannabis facility in St. Louis, implementing double- and triple-stacked systems utilizing LEDs.
“[Under LEDs] we were seeing buds that were tighter and terpene tests that were higher than what we’d see with traditional HPS lights,” says LaBrier, chief operations officer at Proper Cannabis. “We knew that if we were going to build a facility and consider it state-of-the-art, HPS and a single-tiered system was out of the question.”
Adopting a multi-tiered operation is not without its challenges, however. These best practices can help growers transition to LED lighting in vertical systems.
1. Plan layouts for necessary equipment
When planning Proper Cannabis’ 90,000-square-foot cultivation and manufacturing facility, LaBrier knew that a vertical system would require workers to move scaffolding in and out of the flower room and climb ladders to access plants on the top racks. The layout had to include wider aisles to accommodate the additional infrastructure.
“One challenge to vertical farming is efficiently working on the upper tiers,” says Jeff Gumaer, Proper’s cultivation director. “The primary reason for a wider aisle would be to access these spaces with your equipment. The rows don’t need to be wider than 4 feet to execute this, but you have to have the right tools.”
Proper Cannabis uses a specially designed platform system that can fit within that space and expands to 7 feet lengthwise, allowing two team members to work on the equipment at one time.
“It also folds up so that it easily rolls in and out of our aisles when we need to move the workstation,” Gumaer says.
_fmt.png?auto=format%2Ccompress&fit=max&q=70&w=400)
2. Consider spacing
Growers must use different strategies for plant spacing in a multi-level LED system than a conventional single-tier operation using HPS lights. The reason? Depending on the fixture, light intensity drops dramatically the farther plants get from the LED lights. However, because LEDs produce far less by-product heat, plants can be placed closer to the fixtures to create an equivalent relative light intensity at canopy. The correct spacing between the light source and the plant can create dramatically different results for cannabis plants in flower.
“Under LED lights, cannabis plants growing 6 inches from the lights can thrive, showing no signs of light or heat stress,” LaBrier says. “Plants growing too close to HPS lights would be hating life.”
Proper uses a PAR meter to measure light intensity at the top of the canopy and adjusts the lighting accordingly to target a 700 to 900 photosynthetic photon flux density (PPFD) range, Gumaer says.
“The distance between your plants and lighting in any stage of growth has to do with what percentage you are running your lights on. A general answer would be 12 inches to 18 inches from the lights at 100% output,” he says.
In a vertical system, Cunningham suggests shrinking the space between the light and canopy and controlling the environment so your genetics can produce to their full potential.
3. Manage microclimates
Managing environmental factors like airflow, humidity, light intensity, and vapor pressure deficit is essential in all indoor farms, especially in vertical grows.
“The more plants there are in a room, the more chances there are for microenvironments to develop throughout the space,” LaBrier explains.
In fact, LaBrier says that there can be hundreds of microclimates within a 10,000-square-foot room. To maintain the right environment, he suggests growers install additional sensors to track data at various ceiling heights, different plant heights and even within trays.
“There is less air movement, and it’s a few degrees warmer on the top rack,” he explains. “When you think about a production plan … you have to be really cognizant of where we’re putting certain strains because there are small microclimates throughout the room. It’s true of traditional growing, but it’s exacerbated by vertical growing.”
4. Adjust irrigation
Irrigating multiple levels of cannabis plants in a vertical system can lead to disproportionate runoff to lower tiers. To avoid overwatering, Cunningham suggests choosing the correctly sized pipe diameter for each tier to balance the irrigation supply and properly sized pressure regulation emitters to ensure an even distribution of water, isolating supply channels to service different levels.
The irrigation piping also determines the height of the bottom tier, as gravity requires a certain amount of fall per foot for the water to drain. To maximize the number of levels and start the bottom tier as low as possible, it’s best to place the drain in the middle—or install multiple drains—to minimize the drop needed to drain the water, Cunningham adds.
5. Adapt cultivation schedules
The intensity of LED lights combined with growing environment modifications can lead to faster plant growth. One study published in Agronomy Journal found that plants grown under LED lights produced up to 800 grams of cannabis compared to 300 grams for HPS-grown plants.
Faster growth might seem good for growers transitioning to LED lights in a vertical system, but it requires managing to ensure plants don’t get too close to the light in the flower stage. Growers also have to consider how it will affect their workflow, LaBrier adds.
“LEDs help push plants along a little quicker in a positive way, and things that used to take nine weeks were finished in eight or eight-and-a-half-weeks,” he explains. “You have to think logistically about how that will work in a commercial operation where you harvest every week and how it interacts with hang times and cure times.”
While the approach to vertical farming in flowering is different than a traditional single-level, transitioning to a multi-level farm is worth the effort and investment, Cunningham says. He believes it’s the future of cannabis.
“There are huge advances being made with LEDs,” he says. “As power becomes more of a regulator in the indoor farming space and farmers educate themselves, everyone is going to go to LED in vertical farming.”