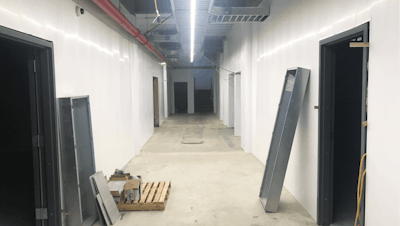
As you plan your first cannabis cultivation operation or as your company expands and you are deciding how best to expand your operation to satisfy increasing market demand, you will have many critical decisions to make. Choosing between retrofitting an existing facility or building from the ground up will be one of the biggest choices you will make for your business. Here are a few things to consider when making your decision.
Retrofit:
1. Maximize existing spaces: For expansions, focus on maximizing square footage you already have. This also applies for new operations retrofitting facilities. Look into vertical solutions for cloning or vegging plants. In post-harvest, automation can dramatically lower your required space. For example, by automating trimming, you can trim the same flower volume more quickly and with fewer employees working at tables, potentially freeing up hundreds of square feet for cultivation.
2. Downtime: Almost any retrofit is going to have some impact on existing operations’ production, from minimal day-long to multi-week shutdowns to replace major systems. Have a plan for disruptions, as one of the most often overlooked aspects of a retrofit is the extent of the downtime required to complete work.
3. Efficiency increase: For expanding operations, increases in efficiency can be just as profitable as production increases. Look at big energy users such as lighting and HVAC and consider more efficient equipment. This can help new businesses get off the ground more profitably as well.
4. Employee amenities: Make sure to account for employees (and adding employees as the business grows) when planning (or expanding) restrooms, locker rooms, parking spaces, break rooms and office spaces.
Ground Up:
1. Reflect: If this is not your first facility, objectively look at what you did right and wrong on your first facility. Consider hiring an architect and engineering professionals—ideally with cannabis industry experience—to help improve upon your vision. Professional guidance can be invaluable to startups as well. A lot of early operators in the industry didn’t have sufficient capital to hire professionals nor did many professionals have cannabis experience. You can’t be an expert on all aspects of the building process, and bringing in experts will not only lead to a better facility design for the long term, but less stress.
2. Modular building: Future-proof your investment by building in a modular fashion. Most pre-engineered steel buildings (the most common building method) can be designed to add additional structures to one or more sides of the building with very little, if any, additional cost. This allows you the flexibility to build out what you need now and then add additional sections as your needs increase, without
having to start from scratch.3. Build in efficiency: A brand new build is the perfect time to increase or maximize your operation’s efficiency. Building from scratch gives you nearly unlimited options. Efficiency doesn’t stop at energy usage. Look at things like workflow efficiency. If you can, sit down with a process engineer or consultant and optimize your facility’s workflow to see profitability and employee happiness increase. An example is movable cultivation tables, which can free up dead space to less than 15% of a room.
4. Location: Will you need to collaborate or transport goods from your first location? If so, consider the distance and travel time between locations. If building in a new area, make sure to consider your hiring pool. Locating an extraction and food processing plant in a rural area may save money, but it could be difficult to secure the technical labor force that would be required.
Read the Cultivation Startup & Expansion Guide