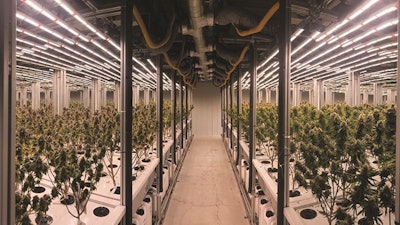
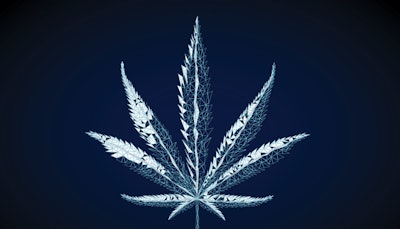
In an industry where the only constant is change, growers are looking to improve current processes and even set new goals.
Valuable employees remain on the frontlines of cultivation facilities every day, but it often makes the most sense to entrust computers, sensors and smartphones to complete certain tasks, like the daily collecting and correlating of millions of data points, such as room temperature, relative humidity, and nutrient and water uptake. Plus, data collection typically isn’t your or your employees’ primary skillset. Even so, each variable in a cultivation operation generates volumes of data that could take days, even weeks, for a person to analyze and put to use.
This is where smart technologies such as the Internet of Things (IoT), artificial intelligence (AI) and machine learning come into play. IoT has become commonplace in manufacturing to monitor machine performance and output. Likewise, utilities companies are deploying sensing technologies to the grid to balance supply and demand and identify potential outages before they happen. Similar technologies can help transform the cannabis industry.
With IoT, CannabiDOL Consulting owner John Dol says head growers, directors of cultivation and assistant growers can connect their laptops or phones to greenhouses and grows all over the world to remotely monitor and respond to potential issues.
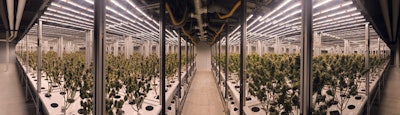
IoT Brings Real-Time Visibility
In short, IoT involves the use of physical objects embedded with sensors that collect and relay information via the internet.
A climate control system in a grow room or greenhouse takes measurements from sensors that measure conditions such as temperature, humidity, lighting, fans/airflow and CO2 levels—and sometimes substrate pH and electrical conductivity (EC), and vapor pressure deficit (VPD), Dol says. Information transferred via sensors to the climate control system, then to head growers off-site, demonstrates IoT use in cultivation.
Real-time access to data is critical for head growers on the go because it allows them to make remote changes to their climate control systems when certain parameters get out of hand, Dol says. They can set alarm parameters so their systems will alert them if something is wrong. Then, they can log into the systems from their phones, laptops, or either—depending on the systems—using their passwords. The systems log who made changes and when.
“For a grower managing multiple sites, this can be a key differentiator to effectively be ‘on site,’” Dol says.
In expressing the importance of IoT, Dol provides an example where an HVAC company could be servicing a grow room. When they finish, they forget to turn the unit back on. “When the lights come on the next morning, all of a sudden your room is at 100 degrees,” he says. If you are receiving real-time data, this can be prevented.
Cultivators also can give permission to other key decision makers, including consultants, Dol says. “Maybe I can only look at the climate side of things; or maybe I can look at climate and irrigation; or maybe I can look at climate, irrigation and heating,” Dol says. “Or they can set me up so I can also make changes.” However, as making those adjustments is the grower’s responsibility, Dol recommends against relying on consultants to make changes when possible.
Many developments in grow optimization came from the ornamental and produce greenhouse industries, the latter of which Dol worked in from the early 1990s until he joined the cannabis industry about four years ago.
For the most part, head growers have more opportunities to use IoT in greenhouses than grow rooms, Dol says. “In the greenhouses, you have to control more things,” he says. “Therefore, it’s more sophisticated and more widespread throughout the greenhouse. In a greenhouse, you have screens, you have ventilation both on one side of the peak and on the other side of the peak.”
That said, many IoT systems are in use in grow rooms, he says. Some outdoor growers use them, too, to respond to data from weather stations, and monitor and adjust irrigation.
“There are very sophisticated systems, and then there are some systems that only tell you, ‘Okay, it’s this warm, you’ve got this humidity, you’ve got this VPD and your lights are on,’ ” Dol says. “It can be that simple, too.”
As it stands, IoT has its limitations, Dol says, noting that AI and machine learning present future opportunities for cultivation. He points out that teams from around the world are conducting trials to autonomously grow tomatoes using AI. “The teams only have access to the climate computer,” he says. “They can’t physically go into the facility.”
A ‘Single Source of … Truth’
Redbud Roots, a vertically integrated cannabis company that operates more than 50,000 square feet of canopy in Buchanan, Mich., uses multiple types of sensors, including environmental control sensors, HVAC climate sensors and canopy sensors to collect and correlate climate and light data. Employees then manually correlate that data and create rules. “One of the challenges we see is determining a single source of climate truth,” David Frankfater, the company’s chief technology officer, wrote in an email to Cannabis Business Times.
One rule that employees set is the timing of dehumidifiers to react accordingly to separate environmental adjustments. “We have a rule to drive the humidity down in the rooms before the humidity spikes at lights out when the plants release more moisture,” Frankfater says. “This rule engages a second sensor trigger ... two hours before lights out. All of these rules rely on data collected from IoT sensors, and dehumidifiers run until the desired humidity setpoint is reached.”
Redbud Roots uses wireless sensors that provide data to “mitigate microclimates and enable growers to make changes via an app that affect light, temperature and humidity levels,” Frankfater says.
The company’s 88 employees include cultivation technicians who use “traditional farming sensors” to measure the pH of water and soil. In addition, Frankfater says, employees look for “the development of microbials microscopically during the last four weeks of flowering.”
On the cultivation side, Redbud Roots’ technology helps the company grow crops with added precision and improve employee productivity, Frankfater says. Employees also can work shorter days because of it. Information technology has also enabled the business to communicate information to its customers and to Michigan regulators.
When communicating with regulators, Redbud shares a “virtual flow” of its inventory and workflow “from seed to sale.” The cultivator uses a handheld device with a Radio-frequency identification (RFID) reader that utilizes IoT to locate and track plants.
At retail, including at its Williamsburg provisioning center that it opened in January to serve medical patients, Redbud Roots uses various programs to advertise and fulfill orders.
“Information technology’s key deliverable is visibility,” Frankfater says. “Visibility and insight are required to quickly identify and solve problems, to reduce costs and above all, to enhance end-user experience and business productivity.”
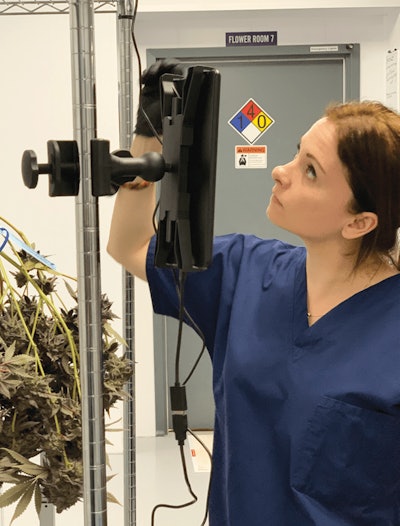
AI Enables Smart Growing
The power of AI and machine learning is playing a more significant role in cultivation. AI allows machines to learn from data to perform specific tasks. Machine learning is a subset of AI that allows computers to learn from past trends. An example of machine learning in the consumer world could be a streaming music or video service that recommends certain songs or movies based on past listening or viewing experience.
In the cannabis industry, AI and machine learning technology are becoming more common in cultivation facilities, says Andrew Lange, president of Ascendant Management and chief technical officer at Agrios Global Holdings. Agrios provides management and consulting services, equipment and facility leasing to licensed growers, while Ascendant provides buildouts, and engineering and design services.
“Depending on what you’re attempting to analyze, AI has the ability to detect and identify patterns and outliers in real time,” Lange says. “The computer will start to learn from your data. That’s machine learning. It can look at all these data points over the course of a harvest, and then input all of your yield metrics, and it can learn from the outcomes. You can do it again and again and again, and the computer is monitoring it each time.”
In addition, AI and machine learning can improve pest and disease scouting by putting “eyes” on plants all the time, Lange says, rather than cultivators having to rely on the subjectivity of employees and trusting that they will scout as diligently as they should. Another process that Lange currently doesn’t use, but is exploring, is using AI and “volumetric cameras.” Although these cameras largely resemble 2D cameras, growers can combine three or more of them to provide 3D imaging that can measure plant volume and predict yields. “It does always require multiple sensors to [create] that 3D image that the data is based on,” Lange says.
Using AI, cultivation facilities can sort through data they otherwise wouldn’t be able to, Lange says. For example, AI helps him manage multiple grow rooms in a 70,000-square-foot Washington facility. Every day at the operation, sensors used in cultivation and to monitor mechanical systems collect about 100 million data points—including 32 environmental points measured every two seconds. These points measure levels of temperature, relative humidity, VPD, CO2, airflow, pressure and more.
“But data points [alone aren’t] really useful,” Lange says. “You have to be able to correlate that data. You have to be able to analyze it effectively. It used to be you would utilize data analysts … then we’re getting into trending software. Now comes AI. AI is really taking that data, looking at it in real time and giving you real-time answers, instead of having to fully analyze everything every time you do a grow. You’re getting faster results, faster data.”
AI then takes information—humidity measurements, for instance—and quickly adjusts levels to create better growing conditions, Lange says.
“It’s able to comprehend the data, analyze it and make changes in real time to affect our environmental outcomes—[it] could be more toward [the] target with less spikes,” he says. “Essentially, you’re just trying to lower any curves inside that data set, so you can utilize the technology to do things like that.”
AI can “identify patterns or anomalies” in data that sensors and IoT technology provide to growers, he says, adding, “This ability can help reduce downtime, lower operational costs and increase production.”