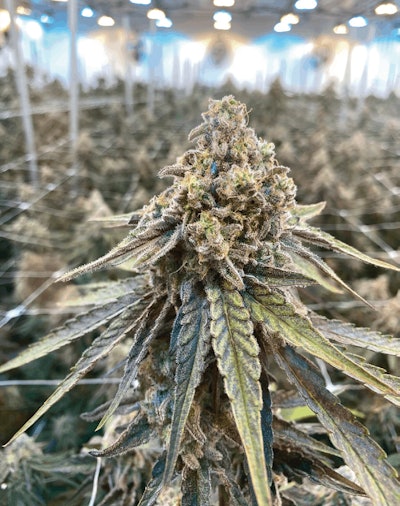
Providing your plants with an optimal growing environment is essential to getting the most from your grow. Without proper environmental control, even the best genetics can never fulfill their potential. Mojave Morelli, director of agriculture and farm operations for Washington-based Grow Op Farms, says most common cultivation problems—from pest and disease management to inconsistent humidity—trace back to insufficient environmental control.
Morelli and Grow Op Farms' facilities manager, Tyler Miller, are on a quest with the controlled growing environment for the production of the company’s Phat Panda brand. With 60,000 square feet of indoor canopy and 30,000 square feet in greenhouse, Grow Op facilities house up to 160 cultivars in production and 500 plants in R&D at any one time. Morelli and Miller are working to ensure every plant gets the optimal growing environment it deserves.
Start with Best Practices and SOPs
Conversations about cannabis environmental controls often start with HVAC requirements. But Morelli says successful control begins with solid standard operating procedures (SOPs) and practices. “If you’re not using best practices, pest and disease pressures are quite problematic. You are going to struggle,” he says.
Invoking the adage “Cleanliness is next to godliness,” Morelli warns that things can go wrong very quickly in indoor environments, where no natural balances are at play. He uses spider mites as an example of a preventable, treatable problem typically introduced on someone’s clothing or from infected plants brought in from elsewhere.
“Chain of custody with plants is always very important,” Morelli says. Grow Op’s best practice is to avoid plants for other facilities. “It’s just not worth it,” he says. “We promote starting with good clean genetics in seed form, and then making your selections based out of that.”
On the personnel side, Grow Op’s best practices prohibit outside clothing in the growing or production areas. Arriving in freshly laundered clothes prior to their work shift, employees dress down to hospital scrubs, hair and beard nets, arm sleeves, and special shoes restricted to facility use.
Morelli says a regular IPM schedule and a robust scouting team are key to keeping your pest pressure in check. “In our indoor facility alone, we have about eight plant analysts. They essentially are scouting crops all day,” he says. In his seven years at Grow Op, he can only recall three cases of mites, which were all identified while confined to a single plant.
Grow Op’s HVAC systems keep the facilities so that air inside is always at a slightly higher pressure than outdoor air. The positive pressure and an air filtration system prevent pests from entering the space, as well.
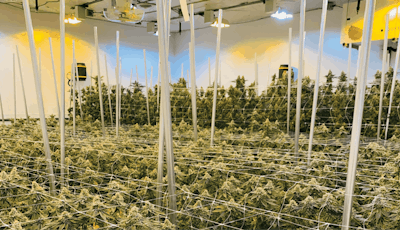
Trade Reaction for Proaction
Before joining Grow Op two and a half years ago, Miller was a cannabis-focused technician for an area HVAC company, overseeing mechanical operations at Grow Op and other facilities. Eliminating opportunities for problems is a primary goal. “We need to get away from the reactionary side and be as preventative and proactive as humanly possible,” Miller explains.
Grow Op’s environmental controls include a full-scale interface that allows growers to log into the system from anywhere in the world to monitor and control rooms. Newer Grow Op rooms measure about 1,200 square feet.
By using room data trends—refreshed every five minutes—along with 365 days of historical trending data, growers can correct environmental imbalances via a digital interface before significant issues arise. But Miller stresses that equipment doesn’t eliminate the need for the human touch.
“The preventative side is trending our rooms, being hands-on and actually standing in the rooms,” he says. To that end, the pair routinely takes 30 minutes to an hour together in a room, watching any air-related movement in plants or the surroundings and physically experiencing what’s happening as air moves through the room. Using that plus monitored trends, they can pinpoint dead spots or stagnant air, or too much moving air on the canopy, or other issues that can be resolved and improved. “Then it’s taking the next step to try to be more preventative and keep a more consistent trend with the equipment we currently possess,” Miller says.
Morelli says environmental consistency is critical in preventing endemic problems such as powdery mildew. “If you operate from the standpoint that it’s everywhere, the obligation is on the operator to manage that environment as best you can,” he says.
Morelli credits swings in temperature and humidity between day and night for most powdery mildew outbreaks. Too much biomass in a room or overtaxed dehumidification exacerbates the problem; overcorrection creates dry conditions that favor spore production.
“The biggest thing that we found with cannabis and managing powdery mildew is making sure your environment is very stable from day to night … Preventative rather than curative is always where you want to be,” Morelli says.
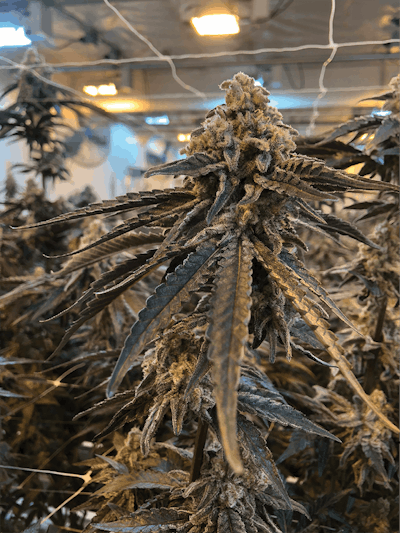
Manage Room Airflow
Miller and Morelli say they learned from experience as Grow Op grew organically. Some older rooms have standard air coolers and supplemental dehumidification. Newer rooms, typically 1,200 square feet, run off commercial rooftop HVAC units with mechanical cooling, gas heat and dehumidification all in one (referred to as an HVAC-D system). Regardless of the equipment, environmental management goals remain the same.
During the past six months, the pair has conducted extensive in-house testing on room airflow to eliminate dead space and ensure optimal airflow throughout the canopy. “We’ve tried multiple avenues,” Miller says. “Not just how we’re introducing our HVAC into the room, but how are we actually maintaining our airflow across the canopy and within the room itself.” Some experiments have included adding humidification, something they’d never done before, to see how this affects the overall environment.
An in-house formula, which includes plant spacing, rolling benches, fans and fan direction, has taken shape. “We’re just trying to figure out how we can keep that air really homogenized from top to bottom, left to right,” Morelli explains. This manipulation of airflow includes getting CO2 into the canopy instead of the substrate and driving more oxygen into the root zone as well.
“We want to ensure that the air being introduced into the room from HVAC equipment is being evenly distributed across the entire canopy,” Miller adds. “We’re making sure we do that by pushing all that air, mixing it up top, pushing it to the floor and getting it where it convects itself back up.”
Morelli says the changes correlate to healthier plants, more uniform canopy, steadier yields and better-looking product overall. “At this point, we’re seeing the results we want. So, we think we’re on the right track with some of these ideas that we have,” he says. “Some might say it’s excessive, but it’s a constant effort to always make things better and find what’s wrong and see if we can fix them.”
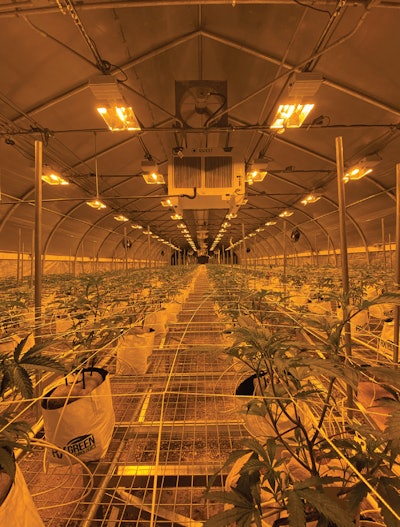
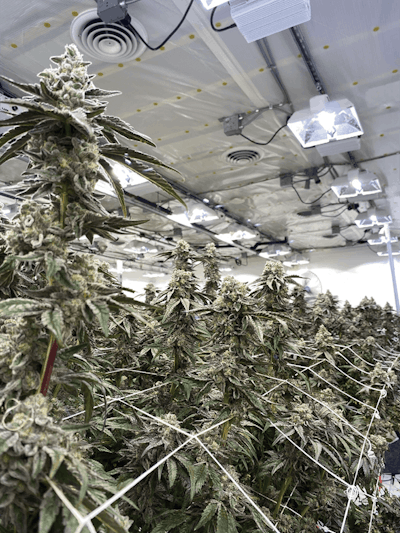
Maintain Consistency
Grow Op has 60 cultivars in flower on any given day, from menu mainstays like their OG Chem and Golden Pineapple to seasonal cultivars designed to appease Washington consumers, who shift between indica- and sativa-dominant cultivars like some beer drinkers shift from winter stouts and porters to summer hazies and pilsners.
The team focuses on an environmental baseline in which all plants will perform well. Then they tailor feeding schedules, irrigation strategies and other factors to optimize genetics. Morelli compares it to an executive chef making small adjustments to perfect each recipe. “That’s why you can never take the humans out of this game,” he says.
For growers struggling with environmental consistency, Morelli advises focusing on vapor pressure deficit (VPD) rather than temperature and humidity set points. Start with a VPD chart; then work your room limitations and manage whatever mechanical capacity you have to minimize swings up between night and day.
“Typically, in a vegetative state up through flower, to the point that the plants have stopped stretching, you want to be in a 1.0 to a 1.2 VPD. That’s a good general rule,” he recommends. “If you’re at a 1.0, which would be about 80 degrees and 68 to 70% humidity, that’s ideal.”
Once the plant stops vertical vegetative growth, Morelli says a 1.2 to 1.4 VPD is fine. “You never want to go over a 1.5,” he says, explaining above 1.5 is too dry and below 1.0 is too humid. “Staying within those pockets, as best you can, is key.”
When vetting HVAC contractors, Millers says it’s critical to give good direction, from the start, on what you want to accomplish with a room. Then let the contractor bring the information to you—and never sell short on HVAC or you’ll pay in the long run.
Morelli agrees. “We even experienced that early on, being on a shoestring budget, just trying to get into the space and get online. Every time we decided to be cheap, it kicked us in the butt,” he says. “Don’t build it until you can build it right. If that means you have 100,000 square feet of space to build out, build one room to start instead of all 20 of those rooms. Take your time with it and build organically like we did.”