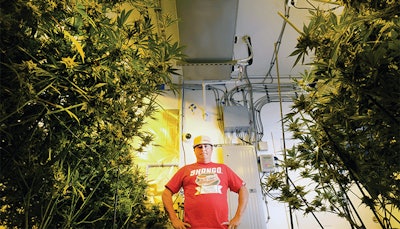
This article originally appeared in the October 2017 print edition of Cannabis Business Times. To subscribe, click here.
As a cultivator for major markets such as Washington, Oregon and Nevada, I’ve had the opportunity to learn how to avoid the pitfalls that face large cultivation facilities, as well as experiment in creating an environment that adapts to mechanical failures or attempted interventions from Mother Nature. Here are a few keys to indoor HVAC success I’ve developed along the way:
1. Construction.
The trick from the get-go is to properly build or retrofit your facility. A poorly planned grow is a formula for disaster. The most critical element is to build the right environment, and the cultivator will succeed. Work with a mechanical engineer who has experience building large-scale cultivation facilities. Don’t assume contractors know how to design one. It takes a team of contractors and cultivators, it takes multiple minds, and not many people have it down perfectly. Most HVAC engineers have not worked on large-scale cultivation facilities, for example.
Sealing the environment is also critical. Do not allow exposure to outside elements because your system can’t be dependent on the weather. In addition, make sure there are enough units in your grow to get the job done. (To determine equipment requirements, consult with your designer as well as a mechanical engineer.) What I’ve learned is that the problem with one or two units is that if you lose one, there goes 50 percent of all of your HVAC. If you have to wait for a repair, your grow can suffer greatly. At Shango, we use four with multipliers for space and temperature that assure we provide adequate amounts of AC.
To read the full article in Cannabis Business Times' October issue, click here.
Top photo courtesy of Shango Premium Cannabis