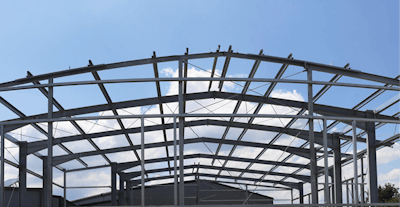
Construction of cultivation facilities presents many unique challenges for any construction team in any market. However, the exacting requirements of cannabis cultivation facilities have no parallel in any industry, which means the process of constructing the “perfect” facility is in a constant state of evolution, and deep expertise remains limited.
While our industry continues to evolve and gain experience, its incremental expansion on a state-by-state and country-by-country basis means that each new market often brings a new set of design and construction professionals with limited or no experience in cultivation facilities—both within the municipality and on the facility operator’s own construction team. Operators entering the industry with their first facility in a new market can be at a disadvantage because they don’t have any experience on which to draw as it relates to building a commercial cultivation facility. And while multi-facility operators have the luxury of relying on experience with previous facilities, their businesses face the same challenges as single-facility cultivators on a magnified scale.
Facility design and construction challenges for multi-state operators expand beyond the construction of one specific facility and impact the entire business, from budgeting to brand identity. Management of capital expenditures is exceptionally important when multiple facilities are being constructed. Cost overruns on a single facility are painful enough, but they can be devastating when multiplied across markets. Operating expenses also must be predictable and further refined with each new facility that is brought online. And cultivation processes must be consistent in order to maintain brand consistency and predictable yields across all markets. But there are solutions and strategies to mitigate these common challenges.
Building New vs. Acquiring Used
Cultivators who operate in multiple markets typically have a strategy of both acquisition and new construction. This usually leads to a hodgepodge of design decisions. With acquisitions, the cultivator is stuck with what the previous owner chose to build.
Acquisitions also require a deep-dive review of the infrastructure already in place to ensure that the facility will work the way the new owner wants it to operate. The most critical component (and the most difficult to evaluate) is the climate-control system and whether it can handle the latent loads resulting from the new owner’s irrigation strategies at the desired parameters, as well as identification of biosecurity risks inherent to the mechanical design.
With new construction, educating design professionals with little to no expertise as it relates specifically to cannabis cultivation can be a long and costly process, especially if engineering mistakes are made as a result of misunderstanding certain requirements.
In new facilities, the architect is responsible for understanding the cultivator’s needs as it relates to the size of cultivation spaces, support spaces, number of employees, construction material preferences and exterior space requirements, to name a few. While certain design components are going to be required across all commercial buildings (American with Disabilities Act (ADA) compliance, for instance), cultivation facilities have very specialized architectural requirements, and individual operators have a very specific laundry list of architectural requirements that serve their own unique processes.
Mechanical design is the engineering discipline that requires the most specialized expertise in new facilities. It has the most influence on the ultimate success or failure of the facility. HVAC design also has major implications on capital and operating expenditures. Managing the climate and doing accurate load calculations in any indoor cultivation facility is exceptionally challenging. Added to that are the specific desires of the cultivation team, which can include ventilation strategies, biosecurity, climate parameters and irrigation schedules. These can all influence load calculations and design decisions, as well as the direct impact that mechanical design has on other engineering disciplines (civil, electrical and structural for instance).
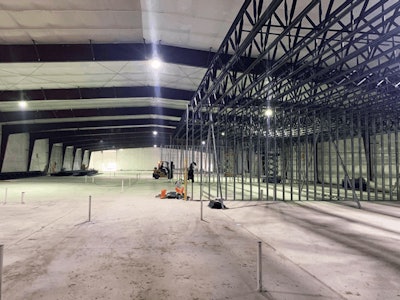
Key Team Members
Thus, for all the reasons noted above, Surna has found that the two most critical engineering and design disciplines are typically architectural and mechanical (HVAC), both for accurately assessing infrastructure in acquired facilities and eliminating the learning curve in new facility design. Whenever possible, cultivators would do well to retain an architect and a mechanical engineer experienced in cannabis cultivation who can work across multiple states or provinces, so the core team stays intact as cultivation facilities are constructed in new markets. This ensures familiarity, not just with cultivation in general but also with the cultivator specifically, and creates a core team that can build on previous experience with no learning curve or re-education required.
Many mechanical engineering firms can deliver electrical and plumbing designs, as well. However, electrical and plumbing disciplines don’t require the cannabis specialization that mechanical does, so familiarity with the cannabis industry and with the cultivator’s specific preferences for electrical and plumbing are generally less critical to success.
While it’s extremely beneficial to bring the core mechanical engineering and architectural team along on each new project to ensure that design expertise is carried over to each new facility, it can also be helpful to identify general contractors with some direct experience within the municipality where the facility is being constructed. Local contractors usually already will have a relationship with the inspectors and plan reviewers, and will have insight into the nuances of how the municipality operates.
Operating expenses also must be predictable and further refined with each new facility that is brought online.
It’s not always feasible for every contractor on the site to be local, but some local experience at the contractor level is advantageous. A combination of cannabis and cultivator experience at the design level and local experience at the construction level tends to strike a good balance for navigating the requirements of the individual municipalities.
Constructing cultivation facilities across multiple jurisdictions can be an obstacle to developing construction budgets and consistent operational expenses across markets. There are the obvious differences like variances in labor rates and cost of electricity to consider, as well as the less apparent considerations like freight costs and access to qualified contractors. On the operational side, often cultivators in individual markets are given autonomy for cultivation decisions, such as climate parameters, lighting selections and irrigation strategies. The inability to standardize on cultivation methodology precludes the ability to standardize on facility design decisions, which will result in substantial variance in capital expenditures during the construction process, as well as energy costs and other operational expenses.
To surmount these challenges, identifying a central point of responsibility for developing cultivation and irrigation strategies to make decisions around climate parameters, water use and lighting decisions, and to liaise with the facility design and construction team can be enormously helpful to streamlining the design process and managing capital and operating expenses by extension. This is easier said than done, as developing and standardizing those strategies is an iterative process, and it usually takes many years to perfect the exact cultivation “recipe.” (That’s not to say that cultivators shouldn’t strive for continuous improvement once their recipe is developed, but identifying what those improvements look like is the role of an R&D or test area, not a production area.)
Once a central strategy across all facilities is developed, the facility design strategy surrounding that cultivation process is simplified as a result. This means that typical lighting selections, climate parameters, rough HVAC loads and at least a basic skeleton of floorplans are generally understood at the very beginning of the design process. Understanding these major components allows for greater understanding of infrastructure requirements at an earlier stage, which allows for faster evaluation of available real estate, more accurate early-stage budget development, and fewer coordination delays during facility design and construction.
_(002)_fmt.png?auto=format%2Ccompress&fit=max&q=70&w=400)
Mitigating Local Challenges
Dealing with different municipalities for permitting and inspection is another area of the facility design and construction process that can be particularly onerous for multi-facility cultivators. The permitting and inspection process is different from municipality to municipality, and relevant building codes can vary significantly, as well. In new markets, a lack of familiarity with cannabis cultivation can mean an exceptionally easy permitting process because the plan reviewers may not know exactly what they’re looking at (or an exceptionally burdensome permitting process for the same reason).
On the design side, engineering disciplines will pull the relevant codes for the municipality in which they’re working and ensure their designs meet those requirements. It’s in the permitting and execution of the design when things can get tricky. For example, operators may breeze through permitting in one municipality and go through round after round of plan-check comments in another, even with nearly identical designs. In one municipality, waste nutrient water may be disposed of down the drain, and in another, wastewater retention and treatment might be required. One municipality may require a certain amount of ventilation in cultivation spaces for occupancy or economization, and another may allow for a largely sealed cultivation environment. And the list goes on.
To ensure the smoothest possible permitting and construction process, cultivators should ensure their engineering partners have included responses and corrections to all plan-check comments, as well as construction administration, in their design contracts. This ensures that coordination with the municipality and the construction team will be seamless and ongoing, with no surprise engineering costs during permitting and construction. The more experienced the design professional, the better, as they will understand how to compose responses to individual municipalities to satisfy objections or demonstrate that the intent of the code is being met when the plan checker is in uncharted territory.
With the right combination of partners and teammates, any cultivator has the tools to be successful in a competitive market. With the right team, even first-time commercial cultivators can minimize construction delays and budget overruns and build a facility focused on maximizing the value of capital expenditures and minimizing operational expenses. However, despite the distinct challenges of operating in multiple markets, multi-facility operators have an added competitive edge. With disciplined focus and by leveraging their own experience as well as the experience of their design and construction teammates, operators of multiple facilities have a playbook for turning their own unique challenges into big opportunities.
Navigate the Build Your Grow Special Report
Critical Considerations When Launching a Cultivation Facility