_fmt_fmt.png?auto=format%2Ccompress&fit=max&q=70&w=400)
Before starting the design process for a new facility, you likely completed an in-depth market review and business plan so that you have some operational targets in mind. Once you’re comfortable with your business plan, the next step is drafting a project brief that outlines the primary goals of the facility. This brief should include what products you will make/grow, how you will make those products, the quantity of products per year, and more production details.
Build For Today
Many people start their facility designing process with a certain size building in mind. Instead, it’s best to start the design process by working backward from your production goals. This is especially important in emerging markets in states with smaller populations, as sometimes bigger isn’t always better. Decide what your annual target production is, then work backward from that to calculate the number of harvests per year and production per square foot to determine how many square feet of flowering canopy you need to achieve your goals.
Example: If your target is to hit 1,000 pounds (453,592 grams) of production per year, you think you can hit 100 grams/square foot (for easy math), and you’re only having one harvest per year, you need to have 4,325.92 sq. ft. of canopy (453,592 g/100 g per sq. ft.) If you have four harvests per year, you would need 113,250 g per harvest (453,592 g/4 harvests per year), which brings your canopy requirement down to 1,133.98 sq. ft. of canopy (113,398 g/100 g per sq. ft.)
Draw a Specific Floor Plan
Remember to size veg, cloning, mother rooms and post-harvest processing spaces appropriately for your level of cultivation. If you don’t know how to determine these figures, reach out to a qualified cannabis consultant who can help you, as mistakes in these initial calculations could lead to expensive corrections later in the build process or, worse, downtime during production to correct mistakes. Designing your facility in this manner will save precious time, not to mention the money spent on architecture and engineering.
If you haven’t already, it would be beneficial to hire an experienced cannabis design consultant to start working out the initial details and some cultivation specific equipment selections such as lighting, irrigation, rolling benches or vertical racks.
Create Building Plans and Conduct Feasibility Study
After you have a workable floor plan that will support your project goals, it’s time to engage with an architect. The architect will be able to review the plan you have and adapt it to local and national codes (if need be), as well as turn it into a building set of plans, which include the final plans on how the building will be built (framing schedules, wall schedules, door schedules, etc.) They will also be able to help get your feasibility study started. This feasibility study is extremely important. Ideally this is completed before purchasing land, but it should be conducted even if the property is already purchased. The study should include verification of the site utilities to ensure your building site has adequate power, water, sewer (in both capacity and availability), and space for parking, fire access, as well as a grid stability study to determine the need for emergency power generation, etc. Discuss the findings with your local municipality and work out any hookup requirements ahead of the design process so that you know what the infrastructure costs will be prior to moving forward. Being unable to hook into a city sewer or having to pay for a power upgrade are quick ways to blow a budget before the project even starts, so it is extremely important to understand those costs associated with your desired location.
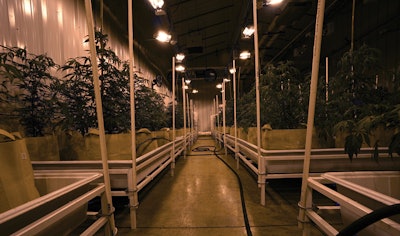
Hire a Mechanical and Electrical Engineer
Shortly after engaging with an architect, I suggest working with a mechanical and electrical engineer, preferably one with cannabis experience. This is likely going to be your most critical decision for success, as the mechanical and electrical engineering portion of the project is by far the most involved in the design phase for cultivation and manufacturing facilities. This includes reviewing and evaluating every component that requires electricity and all the mechanical equipment to maintain environment—all of it needs to be included in engineering prior to installation. Your architect may be able to help find the right engineers for the project if need be, but there are firms such as Surna that have hundreds of facilities worth of experience that is invaluable in this part of the design process.
Engineering is not only the most time-intensive portion of the design, but it also has the largest economic impact on the project cost. Do not rush through this process. Often, clients wish to cut corners at this juncture to get to the finish line quickly, but it is imperative that you take some time to review how the HVAC system will work, its energy efficiency and its maintenance costs to determine if the system is a good fit for you. By this portion of the design process, you should already know your target production and have worked backward on how much canopy and, therefore, how many plants you will have. That will determine your HVAC needs.
On the electrical side, make sure you have accounted for all the major equipment you plan to have. Major pieces of equipment that sometimes get forgotten include: irrigation pumps, water heating systems, control boards, nutrient distribution pumps, trimmers and other post-harvest processing equipment.
Additionally, many pieces of equipment common in the cannabis industry run on non-standard voltage. In North America, these systems require special transformers and other equipment to run. It is also important to ensure you have thought through outlet positioning, as to avoid utilizing extension cords, splitters and other (generally not allowed) devices once you’re operational. Finally, make sure you have battery backups on key systems such as cameras, computers, and networking, to ensure your facility remains online during grid power outages.
Plan For the Future
Keeping future growth in mind during the planning and design process is important, as a well thought out expansion plan will save you a lot of money, time, and headaches further down the road. But if there is one very important thing to keep in mind, it’s to stay flexible. Having worked with dozens of operators over the years, I have seen first-hand that business plans change a lot in this industry.
For that reason, I suggest that if your future expansion plans aren’t in the very near future (around 18 months or sooner), then don’t go too far down the design path. Very often, needs change as markets develop. You might find the extra square footage you’re planning for cultivation is more useful or profitable to your company as manufacturing space in two years.
On the other hand, make sure you’re accounting for additional processes that may be required in the future. Oftentimes in burgeoning markets, demand for flower can be so high cultivators may not cure product or have to store it in bulk, but, as the market matures, need to account for adding those steps to the process, which require space and specialized conditions. Planning for this from the start will save you from growing pains later on.
Mechanical and electrical foresight is especially important. If you need more power for expansion, it’s important to plan that from the start to ensure its availability to the site. Sometimes, it can be more economical to install the equipment upfront for your eventual needs rather than adding on or reinstalling equipment in the future.
If possible, have the infrastructure in place for your future expansion. At minimum, this means having walls, ceilings, doors and basic power and lighting completed, as the last thing you want is construction dust and debris while you’re growing. Ideally, have those, as well as your final power and HVAC, in place so all that remains to utilize the space is acquiring the cultivation equipment. Planning your buildout this way will allow you to expand into those spaces much quicker than if you needed to permit, install, and inspect all the infrastructure for the additional space, and it will allow your company to be nimble with your expansion plans.
Scale for Success
Scalability is another important aspect to keep in mind when developing facility plans. Very few operators can launch a fully operational, large-scale facility at the opening of a new market. This is generally due to either market demand or capital limitations, forcing the operator to adopt a phased-out build or grow approach.
Make sure you always maintain egress for larger pieces of equipment and an easy way to move things into your expansion areas. Plan around being able to move pallet-sized loads of equipment at a minimum. If you have larger things that need to be moved into a space (such as extraction equipment or large-scale dryers), make sure you account for it. I’ve seen operators excitedly order new equipment just to be left in frustration when they cannot fit it through the doors or around a tight hallway bend, requiring them to remove walls, cut holes or even remove roof sections to get the equipment where it needs to go.
Once your team approves the final floor plan, electrical and mechanical engineering can complete their placement drawings for final approval. At this point, your design team should have a 98% complete picture of the finished product, which marks the end of the design process and the start of the building process. The next steps involve reaching out to and vetting general contractors. I suggest interviewing at least four that specialize in commercial construction. Review their portfolio of past projects to make sure they have worked on comparable projects and reach out to past clients (if possible) to get comments on their experience with the builder. Once you have made your decision, you’re ready to submit for permitting and move into the construction phase of your project.
Andrew Lange is director of Agrios Global Holdings.