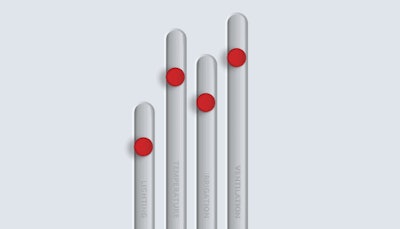
Cultivating cannabis indoors involves replacing sunlight, maintaining target environmental conditions, and providing water and nutrients to optimize plant growth and development. Indoor grow operations can prioritize using control systems to increase precision for finely tuned production operations.
Today’s United States cannabis market presents a very diverse policy landscape. Producers in younger markets may use controls to maximize yield, while others in mature cannabis markets— with decreasing wholesale prices—plan for competition by reducing operating expenses. Increased demand for products and cost compression in cannabis markets have led to new attitudes about efficient and optimized controls systems. Growers are increasingly considering resource efficiency and productivity to rise above the competition by reducing operations and maintenance costs through using high-performance systems and controls approaches.
Environmental, irrigation and other control systems represent profit potential. Various types of business costs, including human resources and rent, never decrease. In contrast, a number of factors can be significant drivers toward profitability, including lower resource consumption, increased product yield, and improved quality. High-performance facilities with integrated control of HVAC, lighting, and water management systems can reduce operating costs by 15% compared to traditional approaches like manual control and data tracking, according to data from the American Council for an Energy-Efficient Economy (ACEEE). Implementing systems that coordinate peak energy use by managing the power demand can generate savings of up to 30% from resource efficiency, according to Schneider Electric, a European utility company.
Take Control of Your Systems
Maximizing the benefits of controls systems involves thoughtfully implementing a range of cost-effective solutions and sequencing equipment to operate in harmony.
In the U.S., capital expenditures for high-performance indoor cannabis cultivation operations range from $250 to $300 per gross square foot (the square footage from outside wall to outside wall, not just canopy space), and controls hardware and software solutions for managing these mission-critical building systems can add to buildout startup costs.
That said, these systems can provide long-term savings through more stable grow conditions by sensing slight changes that humans would not notice until they are significant. Cultivation teams can monitor systems closely and program alarms to check conditions and send instant alerts when issues start to arise. Controls systems allow growers to easily correct problems before it’s too late.
Controls systems also allow cultivators to review high resource use and adjust schedules to avoid peak electric demand times, thus lowering any additional utility bill charges incurred as well as overall energy costs. With some systems, growers may even be able to shift or lower loads during extremely high peak demand periods, a strategy known as “flexible load management.” Growers can work with local energy utilities to develop a plan on areas where slight adjustments, such as maintaining vapor-pressure deficit (VPD) at a higher temperature and humidity setpoint or lowering light levels, may help lower the energy use for a set period of time to reduce demand.
Lighting, HVAC, and water management equipment manufacturers may install onboard controls at the factory. Cultivation facility operators can choose how those controls solutions integrate with building-level controls of varying levels of sophistication. The data coming from standalone sensors can be gathered by building automation systems that analyze grow room conditions and system operation to maintain target environmental conditions like light intensity, room temperature, and watering rate. Integrated controls systems are better able to maintain the optimal conditions for cultivation in your facility, crucial for successful crops and achieving expected yields. Coordinated facility systems work in harmony for optimized plant growth. Cannabis plants reward optimal system performance with higher yields and better quality. Plants in optimal conditions are healthier, reducing the risk of crop loss while requiring less labor.
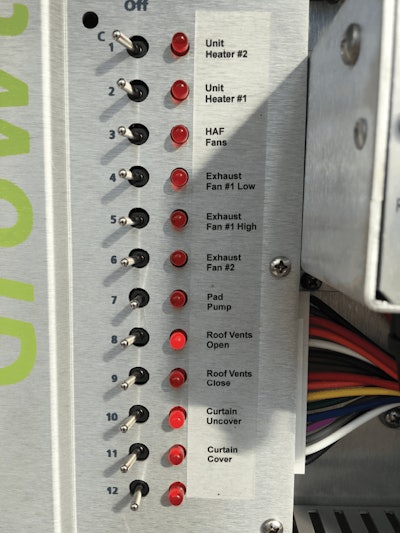
Crucial Controls for Indoor Grows
Before selecting an overall controls strategy, it is essential to know the difference between cannabis facility productivity and facility efficiency. When optimizing productivity, growers aim to maximize output per energy input (for example, by increasing annual grams produced per kWh of electricity, or kBtu if operations use fuels like natural gas). When optimizing efficiency, growers try to maximize the output of the facility’s canopy by increasing grams produced per square foot of flowering area.
Many optimizations will improve both metrics, but at a certain point, they can be opposing strategies. Operators need to understand the difference and select which balance they would like to strike to find the sweet spot for revenue, expenses, and environmental impact that is right for their grow. Local market conditions, the capability of the facility and staff, and cultivars’ genetic potential inform this decision. In most new cannabis markets, where cannabis prices can exceed production costs, operators will lean toward productivity. However, as prices compress and competition increases, operators adopt an efficiency mindset to decrease production costs and maintain healthy margins.
Increasing efficiency often revolves around equipment upgrades. While this is an essential factor, it is just one of three pillars of the output potential of a facility—the other two are the processes and the people executing them, and the cultivar’s given genetic potential.
As a facility improves, it is crucial to measure, fine-tune, and repeat the production cycle consistently. Control systems are a cultivator’s best friend in this regard and help ensure that each process is as close as possible to the last. If these conditions are poorly controlled and inconsistent, it is nearly impossible to determine optimal settings and improve past a certain threshold, leaving output, quality, and ultimately money on the table.
Control systems can continuously monitor intra-canopy conditions throughout a sea of green or multi-tiered racks and automatically respond. For example:
- Sole-source lighting equipment can be controlled on a schedule and dimmed manually or through a centralized building automation system.
- HVAC equipment can be controlled independently or may be integrated through a centralized building automation system.
- Water management and irrigation systems can be separately controlled and may be integrated and automated.
Building owners can review this data and see how their plants react to even the slightest change. They can detect small, easily corrected issues such as temperature changes before significant plant damage has occurred. Rooms also can be easily adjusted by having pre-set conditions for the various grow cycles plants go through. Growers can change their settings from vegetative state to flowering state, all with the press of a single button.
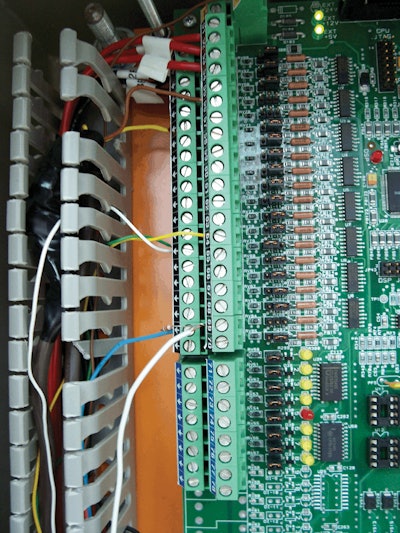
Dial In to Achieve Targets
Realizing the benefits of control systems is made easier with a “tweak-and-peek” approach rather than a “set-and-forget” one. When configuring setpoints in your lighting, HVAC, and water controls systems, start collecting data to understand how setpoints serve your plants. Review historical trends periodically to identify opportunities to dial in setpoints and more consistently achieve desired outcomes for plant biomass production and quality characteristics.
Building automation systems monitor and collect data from distributed and integrated equipment so that historically trended information can be summarized for facility operators using various data visualization methods.
Set yourself up for success with these tips on lighting, HVAC, and water controls systems:
1. Measure environmental conditions at the plant canopy-level, and consider intracanopy sensors to map microclimates at several levels. Many controls systems designed for indoor agriculture now include the option to have multiple sensors in the same room, revealing nuances of the room conditions.
2. Choose response rate and sensitivity levels for each system. These settings will determine how fast controls should respond. Known as deadband, it is a system-level decision and affects energy use and equipment lifespan. Start with wider, less stringent settings and incrementally “tighten” over time. For example, a grower could set a deadband on their temperature control system of 4 degrees Fahrenheit. If the room is set at 76 degrees, the temperature control system won’t kick on until it hits 80 or 72 degrees Fahrenheit.
3. Configure controls hardware to the desired reporting frequency for each system. More mission-critical systems may need to report values more often. For example, cultivators may choose to get temperature readings every 15 minutes, but growing media EC readings only twice per day.
4. Zone lighting controls to tailor light levels specifically for cultivars. When using LED lighting, adding dimming control to have multiple lighting zones in a room is relatively inexpensive. Using this, growers can optimize zones for each cultivar instead of having to run lights at the conditions of the most sensitive strain.
5. Submeter water system data to track actual irrigation rates. Use the data to limit overwatering and identify an optimal root zone moisture content for each cultivar. Watering rates are often too high in cannabis facilities, sending hundreds or thousands of gallons of water down the drain, which wastes money and strains your septic, sewer, or reclamation system.
6. Integrate systems to communicate information between closed-loop systems so equipment can anticipate changes. If you have LED lighting, dim fixtures 15 to 30 minutes before turning lights off. This strategy begins to reduce transpiration rate and more gently transitions building systems to night mode. Avoiding abrupt and immediate reactions of HVAC systems when lights suddenly go off saves energy and prolongs equipment life.