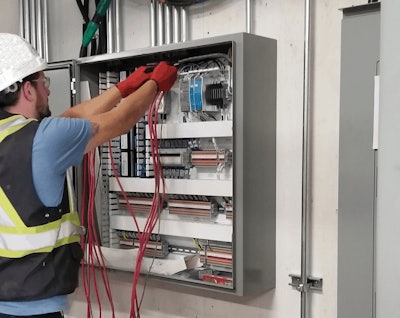
At Surna, we speak often about how decisions around heating, ventilation, air conditioning, dehumidification (HVACD) and humidification touch every component of a cultivation operation, at all phases of development. Budgets, architectural floorplans, construction, facility operation, operating costs and revenues are affected directly by the design and implementation of the mechanical system.
Good design starts with a clear understanding of the goals of ownership, cultivators, and the operations team. Each part of the team should have the opportunity to chime in before a specific direction is decided upon. Ideally, your HVACD mechanical designer should have the expertise to understand the team’s goals and articulate the various technology options available to afford the ownership team the opportunity to compare options. It’s important they understand how each option best meets the team’s goals around budgets, operating costs, operating complexity and maintenance, precision and capacity, biosecurity, odor control, and more.
Unfortunately, not every owner has had that opportunity, and in many cases, operators are working with what they’ve got. So, how can cultivators go about getting the absolute most out of their HVACD systems?
Maintenance
First and foremost is the absolute need to maintain systems in the facility to ensure optimal performance. HVACD systems in cultivation facilities are increasingly sophisticated, requiring maintenance far more complex than simple filter changes. In addition to the proper cleaning of all components, management of refrigerant charges and pressures, controls systems and sequence programming, chemical treatment, lubrication, and more are all part of a correctly executed HVACD maintenance plan. Improperly maintained systems will begin to underperform in ways that aren’t easy to detect at first. While outright failure is certainly a possibility, it’s more common for the early indications of improper maintenance to be more insidious. Diminished capacities caused by improper maintenance first impact energy use—the systems begin using more energy than they need to do the job. This cuts straight into the cultivator’s bottom line in the form of increased operating costs. Like most of the suggestions on this list, improvements in performance and energy use will go hand in hand.
As these maintenance issues progress, systems may begin to fail to maintain climate parameters consistently. Brief departures from setpoints may not be noticeable or particularly concerning at first, but parameter inconsistency can lead to inconsistent yields, as well as create biosecurity risks, as fluctuations in humidity and temperature can leave plants particularly vulnerable to fungus and other pathogens and pests. If filters, ducting and air sterilization equipment associated with the HVACD system haven’t been properly maintained, this increased vulnerability is exacerbated by increased infiltration of those same pests.
As these maintenance-related issues persist, performance will usually continue to degrade, ultimately leading to an expensive emergency service that could have been avoided with far less expense (and stress) had the maintenance been properly managed in the beginning. Sometimes the emergency service is limited to performing long overdue maintenance, and sometimes it results in premature failure of equipment, such as compressor or fan motor failure. In any facility, this is disruptive and expensive. In some, it’s catastrophic. Ensuring that your systems are properly maintained to manufacturer’s specifications will ensure that you can get the most out of what you have, regardless of system type.
Setpoints (VPD)
Vapor Pressure Deficit (VPD) is the difference between the amount of moisture in the air, and the amount of moisture the air can hold, and is the driving force behind plant transpiration. If your climate control system is struggling to maintain setpoints, consider adjusting the setpoints wherever possible to raise the effectiveness of the HVACD system without negatively impacting VPD. Obviously, plant health is always going to be priority one, but the same VPD can be maintained with various combinations of temperature and humidity setpoints. In general, the higher the temperature and humidity setpoint, the more effective the climate control system is going to be at maintaining those setpoints.
For instance, a setpoint of 75 degrees F and 55% relative humidity (RH) is roughly the same VPD as a setpoint of 78 degrees F and 58% RH, at approximately 1.33 kPa (kilopascals). However, the 78 degree/58% setpoint can reduce the HVACD capacity required to maintain those parameters by more than 10%, and in some cases even higher. Ideally, your systems should be designed correctly when you launch to meet your desired setpoints. However, that’s not always the case. If your system is struggling to maintain target conditions, or if your energy bills are excessive, minor system setpoint adjustments can have a major impact.
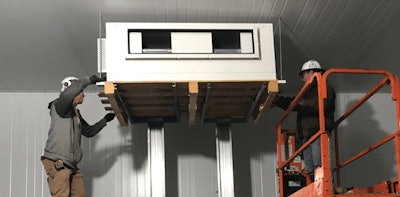
Staging Lighting
Staging lighting systems can assist with the peaks and valleys of the load on the HVACD system, both at the facility level (operating rooms on a “flip,” or opposing 12/12 lighting schedules) and at the room level, by turning lights on and off in stages as opposed to turning everything on and off at once. If your dehumidification system is becoming overwhelmed when lights initially come on or off, powering lights on and off in 5 to 10 minute stages can give the dehumidification systems time to adjust to the changing conditions instead of forcing them to operate in catch-up mode after the fact. This is especially useful if there is no sophisticated controls system in use.
This strategy also serves to minimize peak electrical usage, for which there is an upcharge from most electric utilities, where the cost per kilowatt hour is calculated based on the highest amount of electrical usage at any given time, even if the peak is just for a few minutes. Operating the facility on a flip minimizes peak usage associated with both lighting and HVACD and can have a substantial impact on utility bills.
Controls Systems
While a good controls system can be a bit of an investment, most operators will tell you it’s money well spent. For starters, a good controls system can be a great early warning sign for maintenance requirements. SentryIQ®, a sensor, controllers and automation product suite from Surna, for instance, tells cultivators at what capacity the major components of Surna systems are operating. Anomalies in power use, run times, or other changes in equipment behaviors are displayed and can be a canary in the coal mine for maintenance needs. Similarly, the data collection around room conditions provided with most controls systems can also be helpful as it relates to system maintenance—reviewing climate conditions and identifying anomalies or unusual drifting can be a trigger to check the components of your systems to ensure they don’t need maintenance.
And that’s just one of the many benefits of utilizing controls systems to maximize HVACD performance. The most effective HVACD systems are operated based on a controls sequence—essentially programming that dictates “when this happens, do this.” Simple thermostatic control only allows for enabling and disabling functions of each piece of equipment being controlled by that thermostat (or humidistat, etc.). In some cases, that means slamming an air conditioner on and off at full capacity when conditions aren’t satisfied, regardless of whether the full capacity of that unit is really needed at any given time. With a real controls system, sequences of operation can be adjusted to maximize output when the full power of the equipment is needed, and minimize it when the systems only need to run at partial load, or to stage units when all pieces of equipment in the space aren’t needed.
Some controls systems also provide significant data collection options, inclusive of how the equipment itself is operating, which allow the users to run all manner of reports and trend data to inform decision making. This information can be used to identify areas where energy use spikes and can be mitigated, or where equipment loading may be disproportionate. SentryIQ® products also use predictive algorithms to begin responding to a change in conditions before room conditions are impacted. For instance, the climate control system will respond to the inevitable humidity changes of lighting being turned off, before there is a spike. When a climate control system operates in catch up mode, responding to conditions after they’ve drifted out of spec, it uses additional energy and will take longer to bring the system back down to setpoint than if it is able to respond proactively.
While it’s extremely difficult to retrofit an HVACD system in a fully operational facility, installing a good controls system in a launched cultivation operation is not nearly as disruptive. This should be considered if it’s in the budget to help maximize the systems that are in place.
Get help if you need it
If you are struggling with your existing system and don’t know where to turn, companies like Surna are happy to help evaluate what you’re working with and help you get the most out of what you have. For folks who are planning a cultivation facility, partnering with experienced professionals for design, equipment integration, installation, controls and facilities maintenance will always result in the best outcome for your facility. HVACD systems are one of the most vital components of the cultivation operation. Starting off on the right foot, and staying on it, will ensure the best performance at the lowest cost, and that your facility will generate the maximum returns for decades to come.