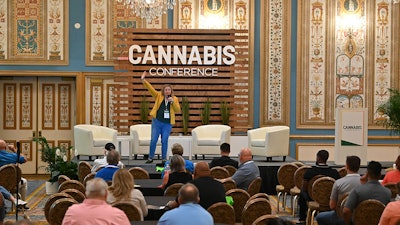
What are the elements of a thriving indoor or greenhouse environment for cannabis plants?
At Cannabis Conference 2022, Nadia Sabeh, founder and president of Dr. Greenhouse, answered this question and discussed crucial environmental control factors that cannabis growers should consider, from managing heat loads to dialing in vapor pressure deficit and more.
Sabeh said most cultivators want their plants to be productive, healthy and desirable—that is, aesthetically pleasing for the end consumer.
Cannabis is unique in that growers want happy plants until the very end of the grow cycle, she said. Then, cultivators want to “stress them to death,” which is what causes them to produce the desired qualities.
HVAC systems, in general, are meant to manage the growing environment through air conditioning, Sabeh said. Most cannabis growers use HVAC equipment to control climate—the temperature and humidity—as well as air movement and air quality, which can impact carbon dioxide levels, pests and pathogens.
Ultimately, she said, growers use HVAC systems to control the environment and thus control plant responses, such as photosynthesis.
“First and foremost, we are managing the energy balance of the room,” Sabeh said. “If you gain heat in the room, that equates to your cooling needs. If you lose heat from your space, that’s your heating needs. Moisture gain is your dehumidification, and on and on. We want to know: What is the balance of heat gains, heat losses, moisture gains [and] moisture losses? [That way], we know how to design, select, and operate your HVAC equipment to manage these energy inputs and outputs.”
Getting HVAC right in a cultivation facility can be difficult for a variety of reasons, Sabeh said. First and foremost, engineers and equipment manufacturers are not growers, and they may not understand the plants’ needs. On the flip side, growers may not understand energy balance or the limits of HVAC operation. And, to top it all off, plants are dynamic, living organisms that need help thriving.
“They can’t go walk over to the wall sensor and change the setting,” Sabeh said. “We have to do that for them.”
Finally, HVAC equipment can be expensive; Sabeh recommended that growers budget 25% of their capital expenditures to costs related to HVAC.
With so much money—and the overall health of the crop—riding on the successful operation of HVAC equipment in a cannabis cultivation facility, how can growers set themselves up for success?
Here, Sabeh offers five key considerations for selecting and dialing in HVAC systems to help cannabis plants thrive.
1. Sensible vs. Latent Heat Loads
It is important for cultivators to understand basic HVAC terminology, Sabeh said, including the terms “sensible energy” and “latent energy.”
Sensible energy is heat produced by the interactions, friction and motion of dry air molecules that can be sensed by thermometers, she explained.
Latent energy, Sabeh said, is heat trapped in or released by water molecules, triggered by water changing from solid to liquid or liquid to vapor form. When the heat is transferred from the air to liquid water molecules, it causes them to evaporate and the air to cool. Latent heat cannot be sensed by a thermometer and must be measured by a humidistat, Sabeh explained.
Sources of sensible heat are the lights in an indoor grow and the sun in a greenhouse, she said, and sensible heat loads are best removed by the facility’s HVAC system.
Sources of latent heat are evaporation from the plants, which converts sensible heat loads into latent heat loads, as well as misting or fogging in grow rooms to cool the space and increase humidity, Sabeh said. Latent heat can also come from ventilation systems that bring humid air in from outside, as well as from any wet surfaces in the facility, such as damp soil or drainage puddles on the floor.
The sensible heat load in a facility is managed by heating and cooling, she said, while the latent heat load is controlled through dehumidification and humidification.
“We’re managing the loads in the room to manage the energy of the plant,” Sabeh said. “It’s all about the plant. We’re indirectly conditioning this space here, this volume of air that you’re sitting in, to make you comfortable. Same thing with plants. The leaf absorbs and releases energy with its environment. The goal is to balance the room energy in order to balance the leaf’s energy or the plant’s energy.”
Modes of heat transfer include radiation from the lights, convection from the air, and evaporation from the plants and water in the facility, she said.
“The energy balance of your leaf depends a whole lot on your source of light,” Sabeh said, adding that high-pressure sodium (HPS) lamps tend to produce more radiant heat than light-emitting diode (LED) fixtures.
To maintain the same energy balance on the plant’s leaf under different lights, she said that growers must maintain different air temperatures; for HPS lights, cultivators should aim for lower air temperatures of 75 to 80 degrees Fahrenheit, while those growing under LED lights should raise the air temperature to 78 to 83 degrees Fahrenheit.
“The goal is to have the same energy balance of your leaf no matter what your source of radiant energy is,” Sabeh said.
2. Evapotranspiration and Vapor Pressure Deficit
Going hand in hand with sensible and latent heat loads are evapotranspiration (ET) and vapor pressure deficit (VPD), Sabeh said, which growers must also factor into their plans for a thriving growing environment.
ET converts sensible energy to latent energy, she explained. Heat is absorbed by the plants and is then used to evaporate water into the stomata. Evaporation from the plants’ leaves has an evaporative cooling effect, causing temperature to decrease and humidity to increase—essentially lessening the sensible heat load and increasing the latent heat load.
ET impacts several elements of the cultivation operation, Sabeh said, including water and nutrient delivery, plant growth, and plant immunity. It can also affect plant structure, leaf temperature and photosynthesis, which can ultimately impact growth and yield.
When it comes to VPD, Sabeh defined vapor pressure as the water vapor content of the air. VPD, then, is the difference between the vapor pressure at saturation (when water passes through the plants’ leaves) and the vapor pressure in the plants’ environment.
VPD is essentially the pressure on the plants to transpire, Sabeh said.
High VPD means the environment is dry.
“We don’t want our plants to be high and dry,” she said.
Low VPD means the environment is wet and humid, with a lot of water vapor in the air. This is also not ideal for the crop.
VPD and ET are intertwined, Sabeh said; high VPD means high ET, low VPD means low ET, and a dialed-in VPD means a dialed-in ET for the grow.
“High VPD usually means high evapotranspiration because there’s not a lot of moisture in the air, and so your plant wants to evaporate more water,” she said. “You better make sure you have a lot of water available for it to do that. Otherwise, it’s going to wilt. Low vapor pressure deficit means you’re going to have a low rate of evapotranspiration. And just right VPD will give you the right ‘Goldilocks’ VPD rate.”
Sabeh said some growers have asked her why they should focus on VPD instead of relative humidity (RH). If a cultivator manages the correct VPD in the room, she said, RH will then be controlled according to the room temperature.
“We can always have the same VPD regardless of the temperature by managing the relative humidity to that variable,” Sabeh said.
Ultimately, VPD affects plant growth and yield, Sabeh said, based on research done on other crops.
“With tomatoes, reducing the VPD significantly increased the relative growth rate and the net assimilation rate of nutrients,” she said. “It also increased fruit yield by 23 percent. If we can dial in the right VPD for the cannabis plant, imagine what your yield could be.”
VPD is also tied to plants’ nutrition and immunity, Sabeh said, using calcium deficiencies as one example.
Calcium gets transported through water, she said, so if ET is too fast or too slow, the nutrient will not be properly transported to the plants.
“If the VPD is too high, water could move so quickly through your plant that it doesn’t have time to absorb the calcium and the calcium just gets left behind,” Sabeh said. “If your VPD is too low and it’s really humid and there’s not much transpiration, calcium doesn’t have another way to get to the plants, like through ion exchange. So, you see often leaf tip burn, … and with tomatoes and peppers and cucumbers and other fruiting crops, we see blossom end rot.”
VPD also impacts leaf energy balance, she said. Low humidity means low vapor pressure, which leads to high ET, high latent heat loads and high water use. High humidity, on the other hand, means high vapor pressure, low ET and low water use.
“If you had vapor pressure deficit right, you could actually conserve water and other consumables and need less energy to do [more] dehumidification,” Sabeh said.
So, what is the right VPD for cannabis cultivation?
Sabeh said that depends on plant type and plant maturity, but overall, growers can follow a few basic guidelines. These include low VPD for clones (since they have no roots), medium VPD for veg (since they need to produce biomass), medium-to-high VPD for early flower (to stress the plants enough to steer their growth) and high VPD for late flower (to “stress them to death,” Sabeh said.)
3. HVAC Equipment Options
With a basic understanding of heat loads, ET and VPD, growers can confidently select and purchase HVAC equipment for their facilities, Sabeh said—but they must know about a few equipment options first.
One option is decoupled systems, or standalone AC and dehumidification units.
“You have the cooling and the dehumidification decoupled,” Sabeh said. “[It’s] two different pieces of equipment for doing those two different operations—the sensible and the latent heat.”
The second option, of course, is coupled systems, which include packaged direct expansion cooling (DX) or chilled and hot water units.
“This is the direction the industry is going as we get bigger and bigger rooms to manage,” Sabeh said. “What we’re doing with these systems, especially with the coupled ones, is we are dehumidifying the air by running it across a really cold coil. If it’s a DX unit, then it’s refrigerant—it’s an evaporator coil. If it’s a chilled water system, like an air handling unit, then it’s chilled water. And that cold fluid is removing the heat from the air.”
These systems lower the temperature down as low as 36 degrees Fahrenheit, Sabeh said, because the air temperature must fall below the dew point, or the temperature when water condenses out of the air. This means the air leaving the coils is too cold for the facility and often must be reheated to the desired temperature to manage the sensible heat load.
4. Dehumidification
Dehumidification, of course, is moisture removal, and it results in condensate that growers can choose to recycle for their irrigation needs, Sabeh said.
When selecting dehumidification equipment for cannabis cultivation, Sabeh cautioned that the systems’ moisture removal capacities (MRC) are typically based on conditions of 80 degrees Fahrenheit and 60% RH—and not many cannabis grow rooms are operating at these conditions.
“The lower the temperature and the lower the humidity, the less moisture that dehumidifier can [handle],” Sabeh said.
Grow room schedules are also difficult for dehumidifiers and HVAC systems to handle, she said. During week one of cultivation, for example, many grow rooms operate at 84 degrees Fahrenheit and 75% RH with low VPD, and that puts growers at risk of over humidification. On the flip side, during weeks seven and eight of cultivation, many grow rooms operate at 70 degrees Fahrenheit and 45% RH with high VPD, which puts growers at risk of under humidification.
Cultivators can take a few steps to avoid the risk of over humidifying or under humidifying the room, Sabeh said. First, growers should select equipment with multiple stages or variable speed drives. They can also install multiple pieces of equipment to serve the same room, running different pieces of equipment based on the plants’ maturity. And, perhaps most important, Sabeh said cultivators can manage airflow within the room.
“Airflow is probably the most underutilized management technique, whether you’re an indoor grower, a greenhouse grower, a vegetable grower or a cannabis grower,” Sabeh said. “In week one of flower, we can increase the airflow—the fan speed—to push air way more quickly across those cooling coils and remove more heat from the lights but do less dehumidification. Also, maybe you don’t use [horizontal airflow (HAF)] fans. Maybe you have variable speed or staged HAF fans.”
Sabeh said as a general rule, growers should maintain higher HVAC airflow and lower HAF airflow during week one of flower for lower ET, and should maintain lower HVAC airflow and higher HAF airflow during weeks seven and eight of flower for higher ET.
“Now you’re in flower weeks seven and eight, and you have a lot of dehumidification, but you have this really low temperature,” she said. “Now, you reduce the airflow across the coils, and you remove more moisture but you increase the speed of your HAF fans because … air movement increases the rate of evaporation. … You can actually help your plants transpire more and be stressed out more by blowing air more quickly across them.”
5. Sensor Placement
Finally, Sabeh said that sensor location matters—and is a critical component to creating a thriving environment for a cannabis crop.
Cultivators must keep in mind that the sensors are meant to target, measure and control the plants, and so they should be placed as close to the plants as possible.
For example, Sabeh said a sensor placed in a return air duct will typically register a lower temperature than one placed in the canopy due to evaporative cooling. Similarly, she said a wall sensor will read a higher temperature than a sensor in the canopy due to the lack of evaporative cooling in that area.
In the longer term, Sabeh said more HVAC equipment needs developed specifically for the cannabis industry to help cultivators more accurately measure and control their growing environment.
“We don’t have the right HVAC equipment yet to serve this industry,” she said. “We need way more R&D.”
Join us this year at the Paris Las Vegas Hotel & Casino for Cannabis Conference, the leading education and expo event for plant-touching businesses.