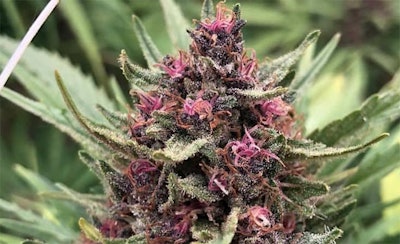
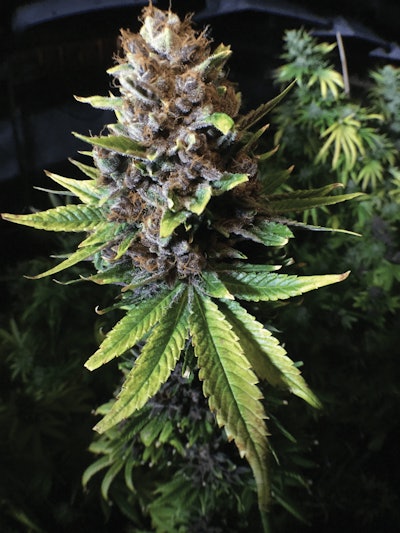
Cultivar Details:
Plant physiology:
Raspberry Boogie’s structure is classic indica: She is short and bushy, growing between 36 and 48 inches tall and just as wide. Raspberry Boogie’s branches are highly productive, and flowers fill the entire length of the branch. Flowers range in color from magenta, pink and purple to green hues.Average yield:
Raspberry Boogie can achieve more than 1 gram per watt indoors and also performs well outdoors.
Flowering time:
Indoors, Raspberry Boogie finishes in a quick 58 days. She will finish by the end of September outdoors in northern climates from Washington to Maine.
Ideal light-intensity setting:
Raspberry Boogie grows well under light-emitting diode (LED) and high-intensity discharge (HID) lighting when the plants’ branches are trained open to allow high intensity light to penetrate the canopy and maximize yields.
Ideal cultivation environment temperature:
When growing under LED lighting, Raspberry Boogie can handle temperatures of up to 82°F. However, when using HID lighting, it is recommended to keep room temperatures below 78°F to preserve the aromatic profile.
Water needs:
Raspberry Boogie produces a high amount of bud sites that fill in. Frequent, even watering is highly recommended (one to two liters per day if a coco medium is used).
Ideal cultivation environment relative humidity:
Keeping relative humidity at less than 55% is recommended to avoid mold and mildew.
Nutrient needs:
Raspberry Boogie likes to eat! Don’t be afraid to feed her well with a special emphasis on silica and calcium/magnesium. Aim for an EC level of 1.5 to 2.0 depending of growth stage, with the 2.0 figure being the target in flowering.
Cannabinoid profile:
Raspberry Boogie has high amounts of THC-A ranging between 25% and 30%.
Terpene profile:
Raspberry Boogie has distinctive aromas of rich, raspberry scents with citrus notes.
Susceptibility to diseases/conditions:
Air circulation is an important aspect when growing Raspberry Boogie, as tight flower colas make plants susceptible to powdery mildew.
Mosca Rick (aka Mosca Negra) is the driving force behind Mosca Seeds.