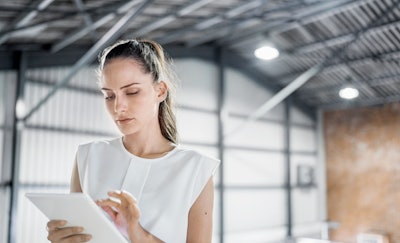
Whether we like it or not, we live in a world full of hostile individuals and organizations. We also live in a regulated world. At this point, you’ve likely heard about standard operating procedures, or “SOPs,” and of current good manufacturing practices, or “cGMPs”—although, they may have never been a particular focus of your time and energy. In the larger world of American commerce, ingestible products are manufactured in accordance with cGMPs, which require written SOPs that describe production processes.
So what? Well, the American companies that manufacture these other ingestible products want to avoid consumer complaints and negative publicity. They do not want to be accused of fraud, or worse. They do not want to waste money on the mad scramble for solutions to problems that they never anticipated. They do not want consumer complaints, invasions by regulatory agents, regulatory enforcement actions or lawsuits. That’s why we’re talking about SOPs.
Let’s agree that a company cannot operate compliantly without SOPs. So, if you don’t have any, do yourself a favor and buy some. A starter pack will run you $49 on the internet and will include templates for document management, out-of-specification and variance management, corrective and preventive action systems, audits, inspections, training, complaint management, change control and equipment management-basically, all the tools you’ll need for a quality-management system to control all your SOPs, quality metrics and operational procedures.
But once you have the SOPs, what do you do with them? The answer, in short, is to integrate them into every process in your operation so that each employee instinctively knows to reach for an SOP to complete a task. If employees aren’t using the SOPs properly, you must identify the root cause and fix the situation. If they continue to not use the SOPs, then you may need to consider hiring different employees.
Be sure to update the SOPs frequently to avoid compliance issues. Some SOPs should contain information on dealing with the applicable regulatory agencies you come in contact with as a cannabis production company. Those regulatory agencies could include, but are not limited to, your state cannabis regulatory body, the Occupational Safety and Health Administration (OSHA); the Environmental Protection Agency (EPA); if you use any pesticide with an Agricultural Worker Protection Standard (WPS) requirement, your local agricultural/farming regulator; and your state’s labor department.
Some SOPs might identify methods for compendial (pharmacopeial) limit testing that aren’t required by your state’s cannabis regulations, but that might get you in trouble otherwise. For example, if you are using alcohol for extraction, there are some things you’ll need to know. For example, the United States Pharmacopoeia (USP) identifies mandatory requirements for residual limits and product labeling. And since alcohol residues are notoriously difficult to purge, you’ll need a reliable method for production, testing and reporting alcohol on your extract labels.
Also regarding extraction, did you know that compressed butane or carbon dioxide gas used as an extraction solvent must be controlled and tested like other raw materials and excipients used in your manufacturing practices? It’s a cGMP thing. Look it up, and write an SOP for it.In other regulated industries, an inspection will begin with the inspector asking for the company’s SOPs during the opening meeting. The regulator will then ask to view each manufacturing process while following along with its respective SOP. To assure harmonization between the SOP, the regulation and the operation being performed, the auditor will document observed deviations into a final report, which will then be used to penalize or fine the company.
This is how agencies like the Food and Drug Administration (FDA) or the United States Department of Agriculture (USDA) keep our products safe and pure like we expect them to be. The quality system and its SOPs provides the inspector with a snapshot of the company’s health with respect to compliance. There is a strong correlation between companies with world-class, quality systems, strong compliance and superior products.
In the cannabis industry, the inspection process is a little different. Regulators typically focus more attention on security matters and inventory control, with less attention paid to cGMPs. How many cultivation facilities do you know of that employ a quality-assurance guard at the front door?
Whether you’re cultivating for medicinal or adult-use consumption, our industry could benefit greatly from some basic cGMP uniformity. Having cultivators adopting SOPs because of the intrinsic benefit they offer would be a great place to start. Here are some points to consider in your compliance system.
1. Understand what SOPs in a cGMP setting can do for you.
If you are interested in avoiding dispensary complaints, boycotts and legal actions; consumer complaints, illnesses and negative publicity; and avoidable waste, lost profits and scrambling for solutions when everything goes wrong, then a cGMP SOP system is for you.
2. Don’t reinvent the wheel.
Resources for “how to write SOPs” can be found through Google searches and are for sale on many websites.
Models exist from similar industries that can save time and money. Consider using compliance systems from industries like pharmaceutical, medical devices and aerospace.
3. Don’t be penny-wise and pound-foolish.
Get help from capable and experienced people, and don’t be afraid to pay for it. Just because your Aunt Diane once helped draft the church’s employee handbook doesn’t mean she should administer your human resource policies.
4. Organize your files in permanent systems.
This is serious. If you don’t want to get sued or fined, organize your files. Binders, tabs, color coding and labels are your friends.
5.Invite scrutiny of your SOP operation.
Dragging out those SOP binders will make a statement to your regulator, who won’t expect you to produce a stack of records upon demand. Make sure to show off training records and other logs that demonstrate your system’s strength.
6.Stay in perpetual motion.
A sophisticated SOP system will grow with the volume and scale of your business.
In the past year, we’ve also read about extractor explosions, pesticide-laced organic concentrates, and even a patient death attributed to a microbial contaminant. These situations were the result of mistakes that could have been easily prevented with proper policies and procedures. Without those policies and procedures documented in SOPs, you can be quite certain lawsuits will follow.