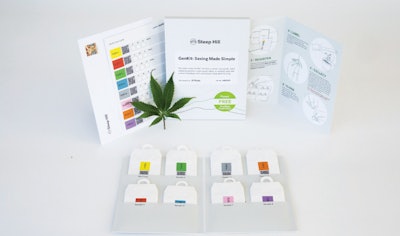
This article originally appeared in the June 2017 print edition of Cannabis Business Times. To subscribe, click here.
In addition to labor costs and overhead, the cost of energy in the form of fuel, natural gas or electricity will be a large expenditure for a cannabis production facility. Recognizing that fact and planning for it can be a strategic advantage to your bottom line. There are many choices to make, and decisions will have far-reaching effects regarding eco-friendly, large-scale cannabis agriculture. It’s not big news that outdoor and greenhouse cultivation, in general, are two of the most obvious ways to save on energy costs over indoor cultivation—by utilizing only or mostly the sun for lighting—but there are a number of other considerations that apply, regardless of the facility type in which you are growing.
Lighting: Advancing Technology
For starters, the lighting industry catering to cannabis production is just now catching up with technology, but as cannabis legalization spreads, the incentive to create superior growing technologies increases.
Many lighting choices are currently available—from single- and double-ended 1,000W metal and sodium halide lights to high intensity discharge (HID) lights, LEDs and convection lights—many with dimmable and spectrum-adjustable capabilities. But I suspect that as cannabis legalization expands and companies can specifically study both indoor and greenhouse lighting requirements for cannabis, they will be able to further tailor industry-specific products to grow cannabis to its fullest potential at the lowest energy cost. (Better yet would be to have large bodies of true scientific research regarding lighting’s impact on cannabis plant growth and composition.)
Heating, Cooling and Storing
How to heat and cool the growth environment is also a major consideration. Think outside the box whenever possible, and investigate all realistic options and emerging technologies such as geothermal heating, which utilizes heat from the earth’s core to circulate throughout a greenhouse; or utilizing steam from geothermal activity to produce electricity as the Calpine electric company does. Wind turbines are not a real option, as you would need a very big wind turbine, and greenhouses are not typically built in excessively windy areas.
For those using traditional power sources, you can at least explore options in costs. In California, for example, Pacific Gas and Electric (PG&E) recently proactively announced that it will be offering existing agricultural power rates to licensed cannabis producers. (See the Guest Column, “(Sustainable) Power to the People,” for more information on reducing power costs.)
But what happens in the case of an interruption in electrical service? The question leads to the subject of backup power generators, which typically run on natural gas or diesel fuel. Obviously natural gas is the logical option. But not all natural gas generators are created equal. Houweling’s tomato greenhouse in Camarillo, Calif., is the first in the United States to use a General Electric Jenbacher J624 two-stage turbocharged natural gas engine with a GE-designed CO2 fertigation system. The generator provides heat, power and CO2 to Houweling’s 12.5-acre greenhouse. The 13.2-megawatt (MW) heat and power co-generation technology captures traditionally wasted heat, water and CO2 for use within the greenhouse. This technology far exceeds the company’s power needs, according to the company’s website, allowing them to supply electricity to the grid.
To read the full article in Cannabis Business Times' June edition, click here.
Top photo: ©druvo | iStockphoto.com