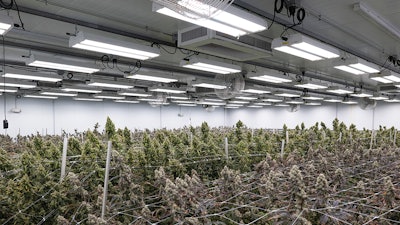
Lighting is one of the most important factors contributing to plant growth. To choose the best lighting design for your cultivation facility, it’s crucial to be able to make an “apples-to-apples” comparison between lighting designs. The challenge comes when lighting manufacturers use different analysis techniques. But by understanding key lighting considerations, you can make the most informed decision to create the best lighting plan for your crop’s needs.
To that end, CBT spoke with two experts in the impact of lighting design choices. Horticulture Service Specialist Jason Matlock, Ph.D., is a member of the Fluence Crop Science team, which melds horticultural science and hands-on production experience for plant-centric support. Chris Bezuyen, Director of Technical Services, leads Fluence’s team of Application Engineers who design and consult on facility design, including lighting plans.
Here's their advice on key things to consider in your lighting design:
1. Analysis area (or focus area) of light uniformity
While light is the most important factor for plant growth, light uniformity is the most important factor for consistent crop yield. As Bezuyen points out, uniformity and repeatability are essential to commercial success.
“It's really important to look at different portions of the lighting design, and not just look at one area alone,” Bezuyen says. “When the design’s focus is the center of a lighting space, uniformity may look exceptional. But as the analysis area increases, so does variability. Light intensity and uniformity can drop significantly around the edges of the cultivation space.”
As an example, Fluence lighting plans consider the entire room—not just the center—to make the entire space as consistent as possible. “When you get a lighting plan, you want to make sure it is not masking any uniformity issues,” Bezuyen says.
Dr. Matlock says there isn’t necessarily one “right” focus area. “You should have an open discussion with your lighting provider about what your goals are and understand how their design focus area aligns with your own expectations. Then apply that same lens to all the different lighting providers that you're evaluating, so that you get a consistent comparison across providers,” he says.
2. Calculation of surface height
While a lighting design simulation can look at focus area in terms of square footage, the calculations also consider surface height, which is highly important to lighting uniformity.
“At each phase of the growth cycle, the effect of uniformity may be more important,” Bezuyen says. That’s one reason the Fluence team encourages growers to identify critical heights for their crops at different phases of plant growth.
When comparing two lighting plans, make sure the analysis height—the distance between the light and the canopy—is comparable. If not, both uniformity and light intensity are impacted, which could lead to inaccurate assumptions and results.
Dr. Matlock asks, “So, are you interested in where the light is at and how it's behaving in the first week of growth? Or are you more interested in a finished canopy height? Are both relevant to you, and you're making decisions based on how things mix? … If somebody parks their calculation surface 6 inches from a light fixture, and somebody else does an analysis 3 feet away, you're going to have radically different [light] levels.”
3. Modeling accuracy of the cultivation space
To make the apples-to-apples comparison you want, lighting plans must accurately represent your cultivation space. Bezuyen says cultivation room materials have improved dramatically—but walls and other surfaces still absorb photons in the PAR (Photosynthetic Active Radiation) range.
“You want to ensure that your light plan is accurately representing wall, floor and bench materials, because that will contribute to your lighting system performance,” Bezuyen says. “When you analyze designs, pay special attention to the reflectivity coefficients being used. It's a fair question to ask, and more than anything, you want to ensure that two lighting designs are using at least the same coefficients, even if they’re slightly incorrect, or one may be overly optimistic.”
Dr. Matlock points out that some lighting designs assume that every photon of light coming out of a fixture arrives at the plant. “It just doesn’t work that way. We know there are ceilings and floors and benches and dirt that create inefficiencies,” he says. When you’re looking at a bid that doesn’t take those factors into account, it doesn’t reflect real-world conditions and can make a design appear better than it is.
4. Spectrum and efficacy impact to PPFD
When comparing lighting designs, understanding the spectrum analysis is essential. Bezuyen explains that LEDs that emit photons in the red spectrum are more efficient on a per-watt basis, meaning those pink, red or purple lights will produce a higher photosynthetic photon flux density (PPFD) at the leaf canopy compared to a whiter light.
“When comparing two lighting plans, it's important to look at what spectrum or spectral mix is being analyzed. One lighting plan over another may look brighter, but it's because you're delivering more red content to the canopy,” Bezuyen says. That can be problematic for many cannabis cultivars because of photobleaching.
Dr. Matlock points out that Fluence’s R4 or 40% red, what it calls the broad spectrum or broad white spectrum, is its most frequently deployed spectrum. “By and large, at the design levels for most cannabis operations, going too far past the broad white R4 creates a risk of photobleaching,” he says. “When you're competing in the fresh flower market, that’s the same as selling scabby apples.”
Like apple scab, which affects aesthetics but not consumption quality, photobleaching impacts market value. That aspect of your lighting design must align with your objectives and your intentions for the product.
5. Luminaire modeling accuracy and field substantiation
Differences in lighting plans can track back to samples manufacturers submitted to certified labs for initial testing. When samples reflect the highest possible performance, lighting plans built on that data can overpromise. That’s why it’s important to be able to validate the lighting design in the field.
Bezuyen shares that validation should involve multiple measurements, which should align with your lighting plan. He also notes to be careful how you measure. Tilted sensors, incorrect heights, distance from your body—even wearing a white shirt—can affect measurements.
“It's also important, when you're doing a field validation, are you doing the validation in an empty room where all the surfaces are cleaned and highly reflective, or are you doing it with full leaf canopy? Because that can make an impact. You need to understand the impact of both relative to the lighting plan,” Bezuyen adds.
As an example, Bezuyen says he might take four measurements in a 5-foot by 5-foot focus area. For a focus area 20 feet by 20 feet, he’d take 10. Those measurements should zero in on the intended calculation surface or critical crop heights identified by the grower, so they can be compared to substantiate the lighting plan.
6. Limitations of graphical representations
Graphical representations of light, such as color mapping and isolines, often drive lighting decisions. But, as with topographical maps used in geography, color mapping used in lighting design doesn’t reflect all the gradients or “valleys” within the isolines. For color mapping, growers should look at the maximum and minimum values mapped to the color gradient. High minimums and low maximums can mask uniformity issues. For isoline maps, the number of isolines in the figure and the difference in flux between lines is important to know. Too few lines and big-difference values mean that the map won’t capture all the variability in the design. Bezuyen and Dr. Matlock point out it’s critical to understand those limitations—and look back at the design’s focus area to understand the highs and lows your growing space will see.
“If the growers are only making a decision based on the wide view of their growing space and color mapping and isolines, or the topographical map of light, they may be missing some of the intricacies that will affect their crop or their plant morphology consistency. So, we really encourage growers to look at that focused area and understand the focused impact,” Bezuyen says.
The pair also emphasize that lighting manufacturers should always be willing to come out after the installation and validate results.
“Fluence has gone out numerous times on Day 1 of the space being commissioned, and then we've gone out the day before harvest, when the room is full of plants and flush with canopy, to validate the measurements,” Bezuyen adds.
More from our latest newsletter:
Sponsored: How Green Rose Co.’s LED Retrofit Boosted Yield and Quality While Cutting Costs
Sponsored: Maximum Light Intensity and Efficacy: RAPTR Series