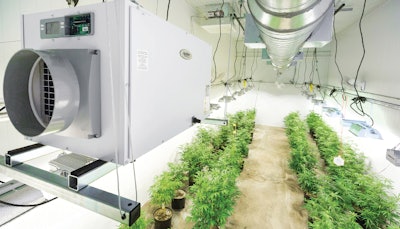
As with most aspects of the commercial cannabis industry, technologies related to heating, ventilation, cooling and dehumidification are undergoing significant change. Cultivators, too, are becoming increasingly savvy as they grow in experience running commercial-scale operations. Cannabis Business Times reached out to a few select growers to get their insights on climate control, lessons learned and advice for other cultivators as well as HVAC-related technology innovations they’re excited to see.
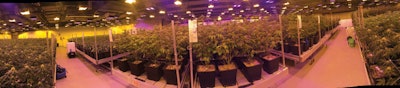
Cody Anderlini, Owner and CEO, Sugarleaf Cannabis. Skagit County, WA.
For Cody Anderlini, owner and CEO of Washington-based Sugarleaf Cannabis, HVAC has come a long way since his biggest concern was finding someone who could install a system without asking too many questions.
“When I first started growing, like many, I used Carrier 5-ton ducted units because they were cheap and the local hydroponic store carried them,” Anderlini recalls. “Now that we are able to treat this like a business, we can prioritize equipment procurement based on real data.”
When reviewing HVAC technologies for his current cultivation facilities, Anderlini’s main considerations were performance, reliability and efficiency. “We needed a system that could handle the ever-changing conditions that our commercial grows produce, without sacrificing power efficiency or noise,” he says. Having the ability to set “day” or lights-on temperatures and “night” or lights-off temperatures was crucial.
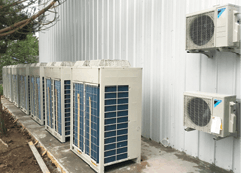
Sugarleaf ultimately chose the Daikin VRV commercial systems because of their multi-functionality and the ability to monitor and control remotely from almost any device. The Daikin units also tie into Sugarleaf’s proprietary cannabis cultivation software, allowing the team to write auto-corrects based on outside temperature and moisture readings.
Anderlini urges growers looking at HVAC to be prepared. “Every time we go to design and build a new facility, we are always asked to have a mechanical engineer take a look at the HVAC system. The problem is the engineers have never built anything like this,” he says. Meetings often involve more time spent educating engineers than moving forward productively. Anderlini advises having information such as light specs, fan specs and building R-ratings (measurements of insulation capacity, thermal resistance) ready—and suggests you trust your gut. “If you are not confident and prepared, you can almost count on doubling your equipment cost,” he warns.
Anderlini also encourages growers to provide as many specifications as possible, spread the load and understand that what worked at home doesn’t translate to commercial applications. “Give yourself at least a 20-percent buffer from what you were used to,” he advises. “If you have the opportunity to buy two 10-ton units as opposed to one 20-ton unit, do it. Even while spending hundreds of thousands of dollars on HVAC systems, equipment failure can still happen.”
Sugarleaf is currently working with Legend Brands’ Dri-Eaz team to beta-test the company’s new Total Humidity Control (THC) line of grow-specific products. “They are setting an industry standard with under-table fans that move the air without stirring up dust on the floor. They also have a desiccant dehumidifier that is going to change the way our industry cures herb,” he says.
Anderlini is also enthused about new Dri-Eaz standard-size dehumidifiers. “Keep an eye on their grow-specific products to hit the market soon,” he says. “These guys are extremely intelligent and are able to isolate [measures of grow room moisture and pressure] like GPP (grains per pound) and VPD (vapor pressure deficit), allowing us to both advance or retard plant transpiration rates in the garden.”
Final word on HVAC: “Anybody can grow mediocre cannabis, but growing great herb is about doing everything right. Every time your rooms dip down in temp at night or get hot during the day, you are affecting cell tissue and introducing stress to the plant,” Anderlini says.
Chris Harris, Owner, Emerald City Wellness. Colorado Springs, CO
_fmt.png?auto=format%2Ccompress&fit=max&q=70&w=400)
Many of the lessons Chris Harris, owner of Colorado-based Emerald City Wellness, shares about HVAC were learned the hard way. Now in his third facility, Harris, who has a construction background, had to re-engineer the climate control systems installed in his first two facilities because they lacked the capacity and correct design needed for commercial cannabis cultivation.
“The main consideration for anyone looking at HVAC systems is to have a design professional that specializes in the marijuana industry work with them,” Harris says. “There’s a vast difference between a building geared to commercial cultivation of marijuana versus a regular building. The heat sources are varied, and it’s just way more extreme. With HVAC, you need someone that’s done this before.”
Correct climate control is crucial to successful cultivation. “A lot of people incorrectly think that as long as temperature is correct, things should be fine. But having your humidity at the correct percentage—at the correct phases of growth—is just as important,” Harris stresses. Understanding the incremental requirements of this sensitive plant and having equipment with the capacity to meet its extreme needs are essential. Harris explains, “For optimum yield, you must make sure that each component is provided. Temperature is first. Humidity is next.”
Harris warns against cutting corners on climate control systems. “Don’t shortcut. The potential dollar loss far outweighs the savings. You have to have a correct and reliable system. If equipment goes down, you can lose crop in a heartbeat,” he says. Harris uses a full-time monitor system with alert texts that allows the team to give issues immediate attention. “Short exposure to extreme conditions may not kill the crop, but it may stunt it. Instead of 100 percent, you get 80 percent. Equate that to dollar volume,” he says.
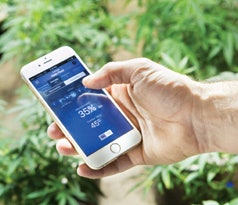
When considering HVAC, Harris notes the limitations of conventional equipment. “You have to remember that traditional, commercial-grade HVAC equipment is designed for people comfort, not plant growing. When it comes to commercial marijuana, most HVAC companies are learning from scratch,” he says. “Our lowest humidity levels run at 40 percent and go up to 70 to 80 percent. You need a special thermostat to allow equipment to operate in that range. Most humidistats don’t even go that high.”
Harris is excited about advancements by Aprilaire, at work in his grow, and the company’s soon-to-be-released models that he says are geared toward the extremes that commercial cannabis demands. “[They fill] a much-needed niche,” he says. “… They are made to handle capacities needed for commercial marijuana growing.”
Harris expects HVAC innovations to flourish as established companies move into cannabis. “Until we see a maturity in the industry as a whole, each of the different systems within the industry will continue to evolve. Lights, nutrients, HVAC, design of pots—they’ll continue to evolve. There will be a lot of adaptation from big agriculture, but innovation will continue,” he says. “As these larger companies enter in with their resources, there’s going to be more engineers and more research. HVAC will be part of that.”
Final word on HVAC: “Consistency and stability in your growing operation is key to producing quality product. Correct and reliable HVAC is essential. It starts with conditions first,” Harris says.
Brian Lade, President, Smokey Point Productions. Arlington, WA
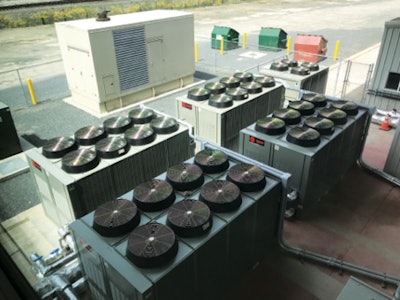
When Brian Lade, president of Washington-based Smokey Point Productions, shops for HVAC systems, he says, “It has to provide the right environment for my plants. So regardless of price or how cool it looks, the environment has to be right. And I have to be able to rely on it,” Lade says.
Lade is also concerned about the effect on people who work for him. “Two things are important to me in this world. My plants and my people,” Lade says. “I want to have a lot of both of them. I don’t ever want to lay off my people, so I try to have really steady, consistent work. To do that, I have to be able to rely on my HVAC systems. That’s No. 1.”
Lade is currently working on his third project with Surna systems, with previous projects including the now “retired” The Clone Zone, a clone-selling company. The current system he uses “is a chiller system as opposed to traditional, forced-air HVAC,” he explains. “It has helped with cost savings, but also I don’t exchange air like a forced-air system does. I don’t bring in any pathogens—molds, mildews, bugs, air-borne bacteria, anything like that—because my rooms are sealed.”
“One thing I’m excited about is that I have control panels for each grow room, and I have access to those with my cell phone,” Lade says. “I get up-to-date information—alerts, text messages and emails—if any of my variables are not where I want them. Temperature, humidity, CO2 and my lights; those four things are the big ones. So I have access and get remote information, and that’s all interrelated with the HVAC system and the lighting and all environmental controls.”
Lade recommends finding an HVAC contractor or engineer that can help you get started the right way. While cannabis experience can be helpful, he feels finding someone willing to listen and learn is important. “You need somebody that’s willing to work with you. Unfortunately, a lot of these engineers and professionals don’t respect the cannabis grower’s opinions or knowledge,” Lade explains. “Coupled with the fact that this is a brand-new industry with new laws and new building code changes that affect the engineers and architects, it’s a real learning curve. They think they know everything about architecture, construction and HVAC, but they don’t know anything about marijuana. You have to have both, or you won’t succeed.”
Lade urges growers not to make common mistakes: not spending enough money upfront, underestimating needed tonnage, trying to save money and cut corners along the way, and, in the end, not having complete control of your environment. “I came up from nothing, from less than nothing, less than a dollar, so I understand not being able to buy even a $5,000 air conditioner, but you have to understand you’ll make your money back. It’s just a requirement. The proper environment is required—and without it, you will fail.”
Final word on HVAC: “It is everything to growing. It’s absolutely everything,” Lade says.