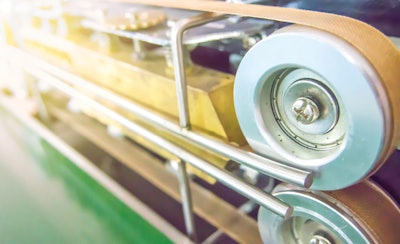
Labor expenses represent a major percentage of operating costs for commercial cannabis producer/processors. Efficiency levels from plant to packaging ultimately determine whether you can stay both profitable and competitive. Many producer/processors are looking toward automation in packaging processes to improve these efficiencies. Cannabis Business Times spoke with two such producer/processors in the Northwest’s highly competitive market about their experiences with automating various aspects of their packaging workflow.
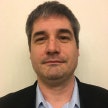
Jason Smit, Co-Founder and Head Grower, Avitas – Arlington, Wash., and Salem, Ore.
With facilities in Washington and Oregon, producer/processor Avitas has a combined indoor grow and processing space of almost 20,000 square feet. Each month, the company individually packages about 40 pounds of flower in Washington and distributes about 200 pounds of bulk flower in Oregon, along with pre-rolls. Topicals and other products are planned for the near future, but the company’s primary product in both states is vape cartridges.
When the company considered moving toward automation in its packaging process, oil-filling machines were an obvious first choice. “We automated our oil-filling and labeling process about one year ago,” says Avitas co-founder and head grower Jason Smit. “Our employees were filling cartridges by hand, and they were complaining about fatigue. That was a clear bottleneck for us. So that was our first investment in automation.”
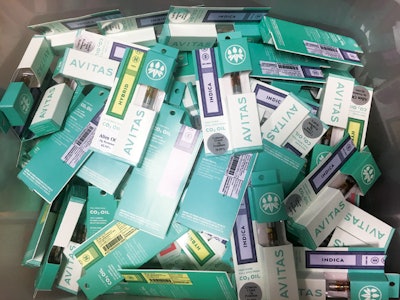
The company’s investment has paid off. “Since we automated our oil-filling processes, we’ve been able to approximately double our cartridge unit count per month without hiring more labor—and our crew doesn’t have sore hands anymore,” Smit says. He estimates the company’s packaging costs at more than 50 percent of the cost of goods on their cartridges. “By doing twice as much with the same amount of labor, we’ve dramatically lowered our operating costs, and that absolutely allows us to compete,” he says.
The company currently works with two types of automated filling machines. One is a hopper-based, single unit. The second is an indexing-type machine that can fill 256 cartridges per batch. Each batch takes about 15 minutes, as opposed to a few hours of labor prior to automation.
Of Avitas’ 47 employees, about 15 work with the machines in some capacity. Operator training is fairly simple. “The operator doesn’t need a lot of skills, but these machines are not without their own challenges. We definitely rely on our facilities crew to be involved with the training and especially the repair,” Smit explains.
Smit shares that the move to automation wasn’t entirely smooth. “There’s been a little bit of trial and error obviously,” he says. “We had one machine … for a couple of weeks, and it just wasn’t working—and another one as well. You have to be aware of what that means before you decide [what to buy]. What are [your supplier’s] return policies, and how are things going to be handled if things don’t work out?”
Despite a few unexpected challenges with packaging automation, the team is sold on its benefits and has plans for more. The next step is integrating the filling and the packaging of its cartridges. “Right now, our packaging isn’t integrated with our filling and sealing,” Smit explains. “We fill and then seal, and then we hand-package because our packages aren’t designed around the packaging machine.” A package redesign will soon solve that problem.
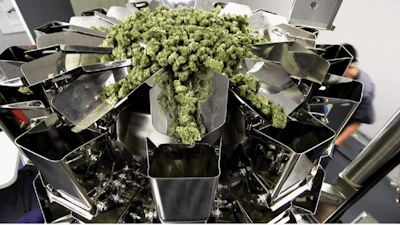
While the company has considered automating the flower weighing and packaging process, that’s on hold for now. “In Washington, we don’t have enough flower volume to justify the expense. In Oregon, we sell flowers to the retailers in bulk, so packing automation is not needed,” Smit says.
For producer/processors looking at automating their packaging processes, Smit advises conducting research up front. “Definitely know how repairs and technical support will be handled and be comfortable with those processes before purchasing. Get your best technical people involved in training and repairs. You should have someone on your staff who is good with mechanical, electrical and plumbing. CAD [computer-aided design] skills and a working knowledge of machine shop machinery is a big plus.”
He also stresses the importance of knowing the seller. If possible, meet with your potential supplier and visit their facilities, and remember that equipment returns may be more difficult the farther you are from your supplier. “The relationship doesn’t end with the purchase; it is just beginning,” Smit says.
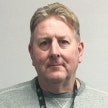
Dan Taylor, President, THC Farms – Tacoma, Wash.
At its 46,000-square-foot grow/process facility, Washington-based THC Farms is constantly looking to automate processes and reduce expenses. The company processes flower from its indoor water-culture grow, as well as processes for other producers. Under state regulations, only processors can sell to retail stores, and delivered product must be pre-packaged for the consumer.
Not surprisingly, packaging labor represents a large expenditure for the company. “The flower is packaged in a lot of different sizes, from 1 gram to 1 ounce, so we were spending a tremendous amount of time with multiple people all in a row with their little scales weighing out into Dixie cups,” THC president Dan Taylor explains. “This was very time-consuming, so we looked into automating that to step up the process.”
The company chose a system built around a PrimoCombi multi-head weigher, customized with two discharge chutes to double the output. Operators program the system to the weight they want to package, then pour in product, and the multi-head weigher sorts the weights. With a bin of poly bags on one side, packagers take a bag and hit a foot pedal to release product from the bin above. A quick finger zip across the bag, and the package is dropped into a bin on the other side.
Prior to automating the process, six of the company’s 45 employees worked in the packaging area. Now, the same work requires two people, freeing up four to work on other projects and other types of packaging. “In our first tests when we got the system in here, in a period of 45 minutes we could [complete] 500 packages, which was a real comfortable working rate for two people,” Taylor explains. “Before, that would take us a day or two with multiple people packaging, so the time savings was dramatic.”
In addition to bags, some glass jars can be used with the system. But hand-packaging still plays a role in more expensive, high-end product in glass. “We’re worried about even the placement of the flower in the jars, so we haven’t fully automated that. But for the most part, 95 percent of everything we’re packaging on the flower [side] is now going through the system,” Taylor says.
The company’s experience with its supplier has been positive. Operator training was quick and easy, and day-to-day operation is straightforward. “This is equipment that’s been used in the food and agriculture business for many years. This manufacturer has put them all over the world, and it’s extremely reliable. It’s just been adapted for the difference in our products,” Taylor says. Technical support through remote diagnostics allows the manufacturer to troubleshoot issues, but problems have been small and few, says Taylor.
Plans are to add a second system as soon as a build-out creates extra space. “The next two things that need to be automated that can all be tied in with this machine is an automatic feed system, where it’ll feed the bags in, fill them and then seal them,” Taylor says. “[Right now], we’re still having to grab the bag manually and hold it up, place it on that system, and then pull it off. We’ve taken care of the biggest time-saver that we could, but we still could take it to the next step. It’s just that we needed more room.”
Typically, the system would allow for extra steps or modules to be added to it. However, THC Farms had its initial unit (which doesn’t manually hold the bags and seal them) customized so employees could sit down while packaging. This eliminated the extra height needed to add the additional components to the existing machine, but Taylor says they plan to use two systems in the future.
To stay competitive, the company is pursuing solutions to automate packaging for its concentrates as well. “We really haven’t seen anything out there with the ability to handle that. That’s still a 100-percent hand-labor job to get that done there,” Taylor says. They’re also looking for an automated system to fill vape cartridges. “It’s a very time-consuming process to fill the little vape cartridges just with a syringe, so we’re trying to find a good auto-fill system. There’s a couple out there, but we haven’t made the decision and acquired one yet,” he says.
The Bottom Line: Labor Savings Increase Margins
For Avitas and THC Farms, the benefits of automation in packaging help the companies compete. “In our particular market, the pricing is so low and so competitive, it just helps us maintain a workable margin,” Taylor says. “Our manpower is our most expensive cost, and being able to reduce the man hours going into the process helps us dramatically keep our margins in line.”
As the cannabis industry matures and competition increases, automation in packaging may be a defining step to keep your cannabis company in contention.