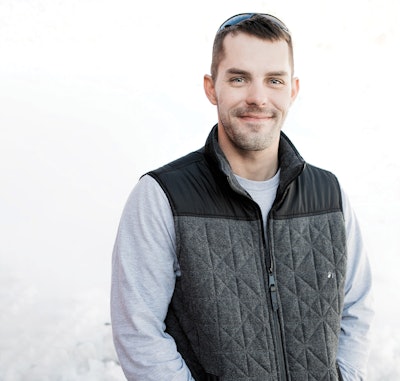
Ryan Aubin has been experimenting with growing cannabis for decades; however, it wasn’t until he discovered caregiving that he was able to convert his passion into a full-time career. As the “master grower” of his own caregiving service, Aubin is advancing his business to a leadership position in Maine’s medical marijuana community by producing an array of consistent, high-quality strains that serve the needs of his diverse patient group. Here, Cannabis Business Times contributor Anne-Marie Hardie talks with Aubin about his operation, and how he is strategizing for an expansion into the newly legal recreational market-which voters approved in November 2016, but legislators are still debating regulatory intricacies.
Anne-Marie Hardie: What initially drew you to the cannabis industry and inspired you to become a caregiver?
Ryan Aubin: After I graduated from college [from Central Florida in 2003], I traveled around the country as a sound engineer, eventually landing in Hawaii. It was there that I first became a caregiver. Being a caregiver in Hawaii was both inspiring and challenging. I never wanted to be a part of the marijuana black market. I wanted to obtain marijuana in the legal form while also helping people that needed medicine.
Being a caregiver goes beyond supplying cannabis to my patients; it has helped me understand the needs of my patients more. There is one gentleman that I’ve cared for who has Lyme disease. The disease had progressed to his brain, and he began suffering from very severe, debilitating, constant tremors. I’ve been able to help him and see firsthand how cannabis has improved his quality of life.
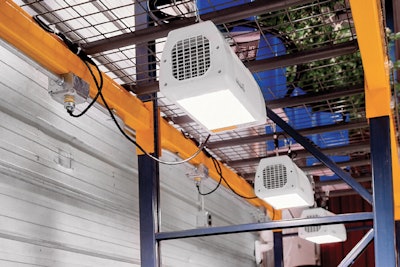
Hardie: What motivated the move from Hawaii to Maine?
Aubin: Being a caregiver in Hawaii is fairly limiting, and so [I] began to look at other opportunities within the [mainland]. I’m originally from Maine, so it was natural to look here. When I looked at its cannabis landscape, I wanted to see [if] I could expand on what we were already doing in Hawaii. Maine provided an opportunity to connect with additional patients and expand a growing operation. [I] initially [leased] a small farmhouse [in Hermon, in 2013] in which [I] dabbled with 16 LED lights from China to explore if converting to LED lighting would have a positive impact on the plant.
Hardie: Over the years, you’ve experimented with a variety of lighting. In fact, even today, you continue to use both high-pressure sodium (HPS) and light-emitting diode (LED) bulbs. What factors are important to consider when choosing lighting?
Aubin: Like most growers in the industry, I started off with high-pressure sodium lighting; however, the possibilities that LED lighting could provide in the flowering room piqued my curiosity. And so, I started to implement the initial LED lighting in the final growth stages of the plant. Eventually, these LED lights that we were using started to fail. In fact, I learned a lot more about LED lighting because of the failures that I experienced. The reality is the lights from China were not from bad companies, but it was a challenge to have to send the lights back to them to be replaced. And so, I began looking for LED light[s] that were more stable and [had] a good warranty.
I discovered my current LED vendor—Heliospectra—at my first cannabis conference. … I liked the style, output and the fact that they offered a full spectrum.
Today, we continue to use [T5] lighting during the initial vegetation stages; however, as the plant gets closer to flowering, we make the shift to LED lighting.
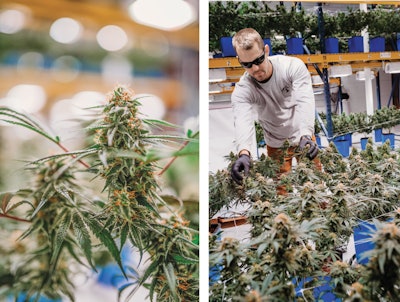
Hardie: What were the reasons that you added in LED lighting during the flowering stage?
Aubin: ... I converted to LEDs during the flowering stage to provide the consistent, high-quality plants that [my operation] is known for. Our focus is not to grow monster plants and achieve better yields. If that was the case, we would have stuck with high-pressure sodium lights throughout the grow process. In fact, the largest pot that we grow our plants in is 3 gallons. Instead, [I strive] for controlled, quality growth, which is easily achieved with LED lighting. Even though the yields are slightly less, the plants are so much more dense. But that’s not all—comparing strains with fellow caregivers] confirm[ed] that the plants themselves have a higher level of THC than when grown with high-pressure sodium lights.
When converting to LED lights, it is important to find the right light height. A lot of people in the industry are unaware that LEDs can produce huge flowers because the lights are too far away from the plant.
Hardie: What are the parameters for being a caregiver in Maine?
Aubin: In Maine, you can have one employee per caregiver. This means one person on staff that helps to maintain the business, but not an additional caregiver on staff. We can have six patients in total, however, I often keep the sixth space open in case I find someone that really needs our assistance.
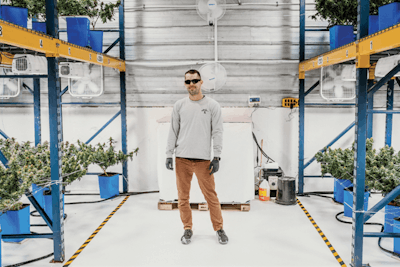
Hardie: You recently relocated to a larger facility. What were the main drivers for moving the business?
Aubin: The commercial building [I chose is] a perfect fit for growing cannabis. It was previously a meat-packing building, and all the rooms were sprayable coolers. This made it extremely easy to complete a thorough cleaning.
[My grow] is still in the medicinal market, [so] I wanted the additional space to expand into if the recreational market opens in Maine. I moved my business to the new location [in central Maine]. The new building is 20,000 square feet, and with the conversion to vertical growing, this space expands to approximately 30,000 [square] feet. ... I bought this building as a medicinal grower today, but my hopes are that with the passing of additional legislation, the operation can grow outwards and upwards.
The property also includes 9 acres, [on] which I would eventually like to include greenhouses as part of [my] operation. There is nothing better than growing plants in the full sunlight.
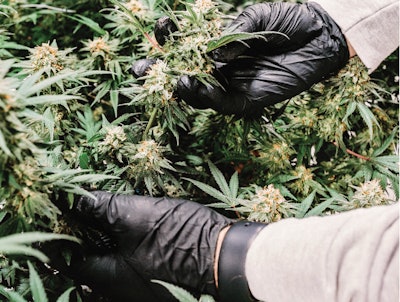
Hardie: What does it mean to have a quality facility? What aspects of your operation set you apart from the other caregivers in the region?
Aubin: When I was still new to the medicinal industry, I was lucky enough to have been brought through The Grove in Vegas. I was immediately impressed [with] how clean the facility was, so if there was a problem, you could immediately get to the root of it. Our plants are all grown hydroponically in LECA [lightweight expanded clay aggregate] and are equipped with ebb and flow feed systems. Everything is automated, keeping both quality, and health and safety, top of mind.
Hardie: With the amount of available cultivars out there, how do you determine which ones to grow in your operation?
Aubin: Over the years, [I have] tested a lot of strains to see what fits well with the needs of the business. I’m constantly monitoring the growth of the plant and asking a variety of questions including: Is the plant resilient? Does it look great? Does it smoke well?
That being said, [the] strain choices always start with [my] patients. I find myself constantly considering: What do they need? What are they looking for? I’m currently growing a S.A.G.E. [Sativa Afghani Genetic Equilibrium] plant for one of [my] clients. It has an extremely low THC content, but it is what [the] patient requested.
There are a few strains that we continue to grow year after year. We’ve been growing Northern Lights for about four years and LA Cheese for about three. I feel that we will grow Lemon Haze forever. It is the most resilient plant that I’ve ever seen. The core strains that I’ve been growing for years will always be a part of [the] operation. However, [I am] always on the lookout for better strains, newer strains, and ideally those with 30-plus-[percent] THC properties.
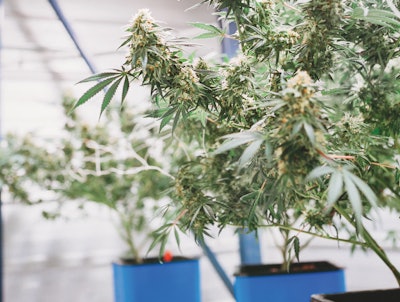
Hardie: What strategies do you use to help prevent pests and disease?
Aubin: At the moment, you can only use neem oil in the State of Maine, and there is no anti-fungal that is able to be used. This is why it’s important to know about the strains’ genetics and to actively seek out plants that are resilient, [and] in particular, those that are resistant to powdery mildew. Our highly controlled environment, including fully sealed rooms, helps to keep out any unwanted disease or pests. However, it only takes one employee to bring in what you don’t want.
[I] have HEPA filters throughout the grow rooms, a couple of carbon [scrubbers] running, and ozone generated in the change room that is constantly cleaning [our] jackets and shoes. Before entering the growing area, [my employee and I] change our shoes and clothes to ensure that no contaminants are inadvertently carried into the space. We also maintain extremely stable conditions, which go above and beyond with both the HVAC system and dehumidification. In fact, we have two Quest 255 dehumidifiers for rooms that would typically only need one.
When we do harvest, we can clean everything in the room. And if there are any problems, [the] new facility makes it easy to power-wash the space to ensure that the contaminants are not carried throughout the building.
Hardie: What is the role of sustainability in your current grow facility?
Aubin: [I strive] to be extremely future-forward, ensuring that everything [I] use is either recyclable or reusable. Even [the] grow medium gets recycled. In fact, the only waste that was thrown away was the root mass. But even that doesn’t get thrown away now; it is recycled by one of our local farmers who wanted the root zone for compost. My hope is to eventually integrate solar panels into the grow facility.