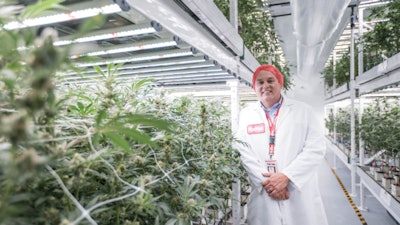
Damian Solomon didn’t start his horticultural career in the cannabis industry. As a 1998 graduate of the University of Arizona’s first class of controlled environment agriculture program, he started the next year working for a Dutch hydroponic tomato company. He refined his agricultural practices and a few years ago saw a need in the cannabis industry for professional commercial experience. At first, he consulted, but for the past 2½ years has worked as director of cultivation for MedMen, a national cannabis firm/management company that offers solutions to license holders in cultivation, extraction, production and retail operations.
In his retrofitted 10,000-square-foot, two-tiered hydroponic vertical grow, he uses Fluence Bioengineering LED lights, which have a thin form factor, close-proximity mounting height to the canopy and reduce the heat load on plants, so he can get the most out of the tight space. “We’re using LED tech because we want to have a compact system,” he says. “I come from a commercial ag background, so I’m all about optimizing systems.”
For Solomon, using an effective lighting setup is just good professional procedure, like using steel racks and aluminum grow benches instead of wood.
“We’re just making sure that we’re growing cannabis as though we’re growing lettuce or tomatoes,” he says. “There’s a lot of tools and tech that can be transferred over from commercial agriculture, and you don’t see that level yet in the cannabis industry.”
Those practices start by looking for lighting products that have been developed for the larger agriculture industry, specifically for indoor vegetable production. Legacy growers can sometimes end up overpaying for specialized products, says Solomon, and he prefers working with companies that develop products for other industries.
“Often, if you’re growing vegetables, you’re operating on very low profit margin,” he says. “These solutions have to deliver high-efficiency because you’re trying to get as much light out of it as possible. If you take the same principles to marijuana production, you can get a really high level of efficiency.”
He measures that efficacy not by production per light, but by grams per square foot. “Different manufacturers have different distribution patterns. Some will illuminate a 4-by-4-square-foot section and others will illuminate a 5-by-5-square-foot section,” he says. “You’re going to have varying amounts of volume under those situations.”
Even more important is the amount of micromoles of light hitting the leaf surface per second, numerically measured in photosynthetic photon flux density (PPFD). Each growth stage has a target PPFD number to aim for, he says. The cloning stage should get 100 to 150 PPFD, and the vegetative stage gets 500 to 700 PPFD. In the flowering stage, try to reach between 1,000 and 1,200 PPFD, he suggests.
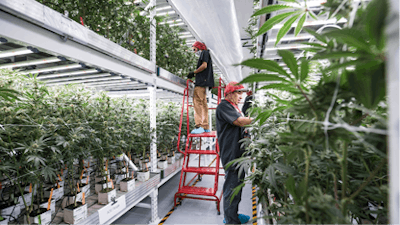
Research and Tips for Testing
Solomon does heavy research before trying new technology. Beyond looking to see if the product is used in other commercial agricultural facilities, he talks to multiple manufacturers at trade shows. He also reaches out to engineers and to other growers with similar lighting designs for their perspectives.
“When you talk to manufacturers, ask ‘Can I come visit a customer?’” he says. “Talk to those customers, and drill down to details, because lighting systems are not cheap. You’re spending hundreds of thousands of dollars. It would behoove you to do due diligence.”
He asks manufacturers to provide research papers, if they have them, on studies they’ve done on their lighting systems. But one of the most important steps for Solomon is running his own in-house trial of the system.
“Everybody’s situation is slightly different, and the results you can expect from new technology are going to be different,” says Solomon. “Also, when it’s something new, you might not necessarily know how to make the changes to the system to optimize your results. A lot of that trial and error is going to come from getting the equipment in and doing small trials.”
A trial space will differ based on the amount of space available in the grow, but Solomon recommends at least a 4-by-8-square-foot section, set apart from the rest of the grow. A larger trial area means a larger sample size, which makes collected data more reliable. But a grower shouldn’t run trials at a size that causes too much risk of lost crops, he says.
If possible, each trial should only test one variable, like light intensity, he says. Trying out multiple changes at once will make causes of increased or decreased growth harder to pin down. And even a test that doesn’t bring expected results can be useful in allowing you to fine-tune later tests.
“Just because the first trial ended up failing, you can figure out why it failed and try it again,” he says. “And then do it another time, and another. Then you get a stronger sample set, and a stronger data set with your results.”
Especially if the trial concerns flowering time or technology a grower hasn’t used before, he recommends running through four or five cycles at a minimum before judging the results to see if they can be applied to the whole grow.
“It’s all about getting consistent results, which then apply across the entire operation, so you can get a high level of confidence that you’re going to be able to repeat those results over and over,” Solomon says.