
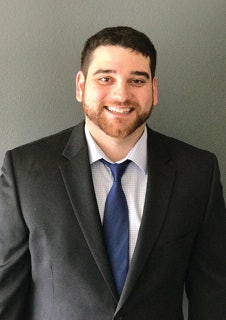
At Agrios Global Holdings’ 70,000-square-foot indoor facility in Shelton, Wash., a license holder—Onyx Agronomics—operates a 65,000-square-foot ISO9 standard clean room, growing cannabis using Agrios’ automated aeroponic cultivation technology.
Despite its size, “the facility uses 63 percent less energy than a typical facility of its size, while requiring 80 percent less labor through automation,” says Andrew Lange, Agrios’ chief technical officer. “Extensive water-saving and reclaiming technologies allow the facility to be totally water-neutral—and all climate control is done through a closed glycol-loop chiller system, provided by Surna.” Next up, a second phase of construction is underway at the facility, “using a water-to-water multi-stack chiller unit with an evaporation tower to further drive down energy usage,” Lange says.
Here, Lange shares how you, too, can build while keeping HVAC in mind, along with common mistakes growers make when building an HVAC system, how to set your climate control settings correctly, and more.
When you survey a space—or build anew—what must you keep in mind structurally for an HVAC system and other climate control?
Andrew Lange: There are a few things you definitely want to keep in mind for your mechanical systems when building new or retrofitting. First is the location of your outdoor units. Having a mechanical slab—a slab of concrete where the largest HVAC components are located—at ground level is ideal [because] it is much cheaper than placing [units] on the roof (at least from a construction standpoint) and they are also easier to maintain on ground level. Your mechanical slab should be close enough to the building so as to minimize the expense of running electrical and plumbing, and have enough room to not only place the units but easily service, add or move units in the future—especially if you have an expansion plan. In addition, I like to place these mechanical areas near the primary power distribution to minimize the expense of running very expensive primary feeds to it.
Inside the facility, we like to utilize overhead space in cultivation rooms for mechanical systems. This keeps the equipment out of the way of employees and minimizes or eliminates interference with cultivation equipment, allowing for the largest possible canopy in the space. This means that your ceiling system has to be rated for the load of the mechanical systems so that [it is] strong enough to support [them]. Ideally, we also want taller ceilings. I try to avoid going below 10 feet, with the ideal height at about 12 feet to 13 feet. This, of course, is all dependent upon the cultivation method being deployed. It is always important to think about future accessibility when installing the overhead systems. Clearly mark valves and place them in areas that can be easily accessed even when plants are in your space.
What is the biggest mistake you see people making when they build an HVAC system—especially if they plan to expand one day?
Lange: One of the largest issues I see is [a lack of] proper redundancy [otherwise known as the duplication of critical components, like a fail-safe]. When a good engineer designs your mechanical system, they will build in a proper amount of redundancy, which could be 15 percent to 30 percent [of your required capacity]. This extra mechanical capacity is extremely important if there are mechanical failures with air handlers or dehumidifiers or even heaters in colder areas.
Ultimately, many people building facilities have fixed budgets, and by the end of the design period they are often looking for ways to cut expenses. As this redundancy is often viewed as “extra” instead of a necessity, it is often reduced or eliminated. HVAC is the single most important system to determine one’s ability to successfully cultivate indoor. Don’t skimp on it.
When you’re setting up an HVAC system with the intention to expand, what should you keep in mind before you expand?
Lange: Obviously, if you’re planning to expand your HVAC systems in the future, you need to go into the initial design with at least an idea of what you want to accomplish when that time comes. Let’s say you’re planning on doing two phases of construction: an initial 10,000-square-foot [facility] and then a second phase of equal size. In this situation, you may have the layout of the first phase done but not the second, as you aren’t sure if you will want to change anything. Generally, that is fine as long as you have a good idea of your loads. Calculate the maximum amount of load you could have [in the future, at full build] and plan for that—at the very least.
Now, when you design the system for the first phase of construction, you very likely can build for the future capacity fairly cheaply, and certainly cheaper than having a dedicated system-per-phase of construction. If possible, engineers can simply increase supply and return line sizes to accommodate future growth, allocate extra space for future equipment in mechanical rooms and pads, and other low upfront cost items to dramatically reduce price and installation time for the second phase of construction.
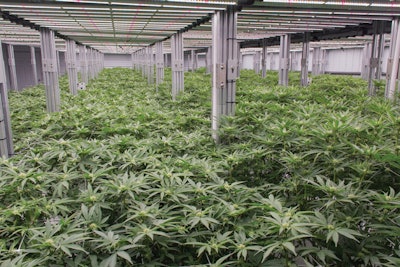
Can you share your top three considerations when building an HVAC system with the intention to expand?
Lange: First, make sure you have enough room in your mechanical spaces for future expansion.
Second, ensure you have enough power at the pole to accomplish your expansion. Check with the utility company to ensure you have the power there. It may be cheaper to bring in all the power you need at once instead of at two separate times.
Third, future-proof all systems. There are many aspects to an HVAC system besides cooling, so remember to look at dehumidification and where that condensate is going. If you are capturing it, remember that you must store it, and if your facility gets bigger, so does your storage. Do you have the room? Heating can also be an issue in colder climates. If you plan to double the size of your cultivation in the future and you heat your facility using natural gas, make sure your gas line is large enough to accommodate that future growth.
When you do expand—either by expanding your existing grow room or adding another room to your operation—what should you keep in mind?
Lange: One very important factor to consider when adding cultivation spaces to an operating facility is how it will affect your work flow and overall scheduling. Many operators run on a flip schedule, meaning only half of your 12-hour rooms are running at a time. When you go to expand, ensure you have the capacity in your HVAC system to accommodate the extra load without reducing redundancy.