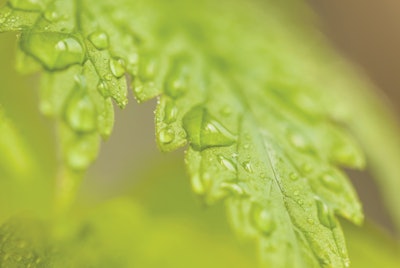
In cultivation, we often talk about Vapor Pressure Deficit (VPD) and the relationship between temperature and humidity as it relates to plant health and transpiration, but rarely do we focus on that relationship and its impact on our financial bottom line. However, decisions around both parameters will have a substantial impact on both capital costs and ongoing expenses, so it’s something that all cultivators should understand.
The most common dehumidification systems are refrigerant-based. These work by pulling air into a chilling system that cools the air to below the dew point (the temperature at which moisture condenses into liquid) and then drains that water out of the facility. As such, air conditioning and chilled-water systems are also dehumidifiers—the air temperature drops below the dew point temperature, and condensation/dehumidification is a byproduct. Conversely, air conditioning is also a byproduct of refrigerant-based dehumidification, which is why you must reheat the air if you’re controlling your mechanical system in dehumidification mode.
What’s important isn’t just the temperature and humidity that you’re trying to achieve, but what you’re trying to achieve simultaneously. The lower the temperature and/or humidity in your space, the lower the dew point temperature, the harder any dehumidification system must work to maintain the chilling coil below that dew point.
The ratings on dehumidification equipment are based on Association of Home Appliance Manufacturers’ (AHAM) recommended conditions of 80 degrees Fahrenheit (F) and 60-percent relative humidity (RH), which is a dew point temperature of 65 degrees F. As soon as either the temperature or RH decreases, the output of that unit (whether it’s an air conditioner or a dehumidifier) also decreases. For example, if you try to operate your cultivation facility at 68 degrees F and 40-percent RH, you would have a dew point temperature of 43 degrees F, which means the output of your dehumidification equipment decreased substantially. The impact on your wallet is that you’ve increased your capital costs by being forced to outfit your facility with more equipment, and you’re paying substantially more in electrical costs to operate that equipment. (To figure out different dew point temperatures relative to different ambient temperatures and RH, you can visit bit.ly/dew-point-calculator.)
In some cases, cultivators request a temperature and humidity target that results in a dew point temperature that’s below freezing. In those cases, we can’t use typical dehumidification systems, as we’d simply be creating ice on the coils. Instead we must implement an absorption method (desiccant). These units are designed to absorb moisture rather than condense it and are both energy efficient and effective at reaching lower temperature and humidity targets. Unfortunately, these units cost typically three to five times more than the typical dehumidification systems and require a substantial amount of heat to recharge the desiccant media. Also, they only work as dehumidifiers and require a bit of a double-up on infrastructure, as you’ll still have to provide a source of cooling. There are custom air-handling options where desiccant is incorporated into the air conditioning system, but the capital expense component is equally significant.
Weigh Your Options
It’s important when you’re designing your cultivation facilities that you focus on what you really need. We often talk to cultivators who communicate that they’d love to reach a specific temperature and humidity, but when they learn what it will cost them to do that, they quickly back off to a more practical target for their budgets. The key is to make sure you’re working with a mechanical designer who clearly understands the impact of your decision and can articulate the budget and energy considerations to you clearly so you can make a well-informed decision early in the process.