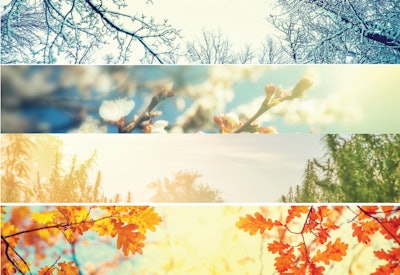
The Heirloom Collective’s tagline is “gently grown,” shares Patrick Cloney, its chief financial officer, “because we want to be as close to organic as possible. We care about the earth and climate change and to the best of our ability and what existing technology allows, we built our facility to reflect that.” The Heirloom Collective reuses all HVAC condensate in its fertigation, reuses excess irrigation, and has plans to implement solar panels on its roof, Cloney says. Its 20,000-square-foot space—which includes one triple-tiered and four soon-to-be double-tiered grow rooms—are “super insulated, and we grow under LED [lights],” he adds.
The Heirloom Collective chose Surna to design and equip its HVAC system. Surna’s chilled water system provides precise temperature and humidity control but also utilizes unique designs aimed at energy efficiency.
However, Massachusetts’ climate does present challenges for the operation. “We have four true seasons—and they are all very different, and the season can change within a week or even a few days,” Cloney describes. “We go from one extreme to another: Winters can be very cold, very snowy and very dry—while summers can be very hot, very rainy and very humid.” Nonetheless, the team also faces challenges that any indoor cannabis grower would. Here, Cloney shares how the team addresses five of their top HVAC-related challenges.
1. Temperature
To keep product quality consistent, The Heirloom Collective must keep its temperatures consistent, Cloney says, despite extreme external temperature swings. To make sure its indoor temperatures don’t swing with Mother Nature’s whims, the facility’s HVAC was built to “always maintain proper levels for growing” despite outside temperatures, Cloney says. “You want to keep the temperature inside your grow environment within certain bands,” he says. “Because if you don’t, then you’re going to get a different product at the end of the cycle.” The ductless HVAC system allows for grow spaces to be completely sealed, not allowing for outside variables to affect the critical indoor environment.
2. Airflow
To grow the healthiest plants possible, the right type of airflow is also a concern for The Heirloom Collective. “Air movement inside the grow room is critical for a proper growing environment,” Cloney says. But airflow from external sources is prevented. “Our rooms are super tight, super airtight—they’re basically coolers within a cooler.” To control airflow, The Heirloom Collective’s outer building is insulated, he describes, while “we built little buildings inside the bigger building that are also airtight.”
3. Humidity
Just as it addresses airflow, insulation also helps The Heirloom Collective deal with Massachusetts’ humidity, Cloney says. (In Boston, Massachusetts’ capitol city, the average humidity ranges from about 62 percent in January to 72 percent in September.) “Regulating humidity in the grow rooms is the biggest challenge in any grow operation because too much humidity will lead to fungus and disease and crop failure,” he explains.
Therefore, dehumidification is the biggest challenge in these cultivation facilities. The Surna chilled water system is designed to handle the huge, constant dehumidification load while at the same time being energy efficient.
4. Pest infiltration
There are many pests in Massachusetts that could affect The Heirloom Collective’s grow. But one way The Heirloom Collective combats pests, Cloney describes, is by “eliminating places for pests and mold to hide.” When The Heirloom Collective’s team chose its HVAC system, they decided to do away with ducts. “If you had nothing in the room, it would be easier to clean the room,” Cloney admits. “But that would mean you have tons of duct work outside the room, and that duct work poses all sorts of places for pests and mold, funguses to hide. [We decided to] do away with ducts and compromise on our keep-everything-out-of-the-room principle and put air-handling equipment in the room.”
5. CO2 levels
The Heirloom Collective also works to keep its CO2 levels at an optimal level. One way it maintains the right amount of CO2 is through its air handlers. Additionally, the facility also utilizes multiple air handlers to ensure one is always functioning. “Traditionally, you have one giant air handler moving all the HVAC air into one room through all that duct work, and I was uncomfortable with that because if you lost a handler, it could fail—and you just lost your room. But in the system we went with, you have a little bit of an insurance package because there are multiple air handlers, so if one of them fails, you still have a whole bunch that will be active and keep the room operating while you get to the end of the harvest and make repairs.”