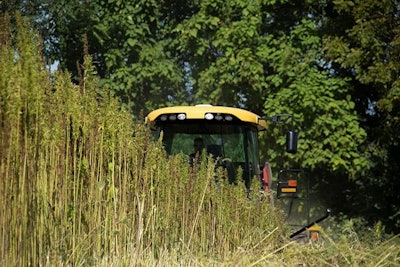
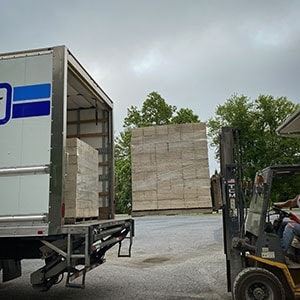
Coexist Build, a Pennsylvania-based architecture firm, has its eyes on hemp. The plant’s capabilities as a building material allow the team to take a “seed-to-structure” mentality when cultivating the crop and planning out the necessary partnerships and processing infrastructure.
Drew Oberholtzer, co-founder of Coexist Build, along with his wife and fellow co-founder, Anastasiya Konopitskaya, sees the potential as vast. They were well into their careers when they found themselves in Los Angeles three years ago, working on single-family homes and interested in pursuing some sort of prefab construction format. The materials were a problem, though: mostly petroleum-based foams and plastics.
The rabbit hole of research, as Drew says, brought them to hemp.
It helped that they are both from Pennsylvania in the first place. The couple bought a small farm on good Berks County land and took to the crop as a case study. Of course, the soil quality of eastern Pennsylvania and the proximity to the Northeast population, to say nothing of the region’s manufacturing bones, made the fit that much sweeter.
In the first year, Coexist Build and Cameron McIntosh of Americhanvre created the Hemp House on Wheels, a guerrilla marketing device, in a way, that showed off the Coexist Build proof of concept: You can construct a house from this plant material.
“That was kind of our market analysis to see what people were thinking,” Drew says. “Then we started developing and manufacturing the hemp block and looking at other opportunities to expand.” Hemp blanket batt insulation is another product that the team went to work on.
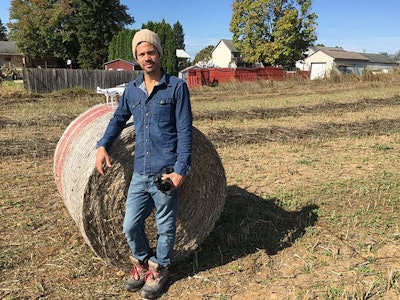
The goal is to shine a bright spotlight on hemp as a building material, to amplify the work that Drew and Anastasiya started three years back.
“This year, we're going to be certified regenerative organic through the assistance of [Pennsylvania-based] Rodale Institute,” he says. “We want to work toward understanding: By farming hemp regeneratively, and then building with it with hemp-based building materials, realistically, how much carbon are you sequestering? Then we can start looking into the possibility of instituting a plan for carbon credits and all that sort of stuff for incentives [for farmers].”
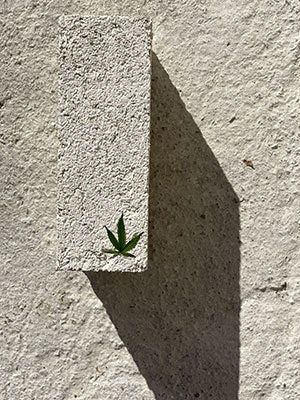
For farmers who may be interested in the idea of building materials as an end use for their crop, Drew says it’s still a matter of much-needed research to dial in the ideal varieties. Other factors that lead to strong source material include: how long you keep the crop in the ground, when you harvest, how long you ret the material and whether you round-bale or square-bale the hemp. Do you run it through a roller breaker or a hammer mill? What’s the ratio between bast fiber and hurd when all is said and done?
The tensile strength and quality of the bast fiber is dependent on a different suite of calculations than, say, what the CBD hemp farmer is navigating in the field. The research is ongoing, and that’s something that Drew says Coexist continues to hone.
He pointed out that Coexist ran tests with a well-known equipment manufacturer’s hemp harvesting gear—to see whether it could harvest and bale the notoriously thick and knotty hemp crop. It could, but Drew cautioned that growers should be attuned to their insurance policies in the case of failure.
The matter of market infrastructure for the fiber segment of the hemp industry is often presented as a chicken-or-egg scenario. Which comes first? The cultivation capability or the processing capability? With a small boost from the state and an innovative design, Coexist Build is staking its claim in the conversation and moving forward to a promising future for the whole industry.