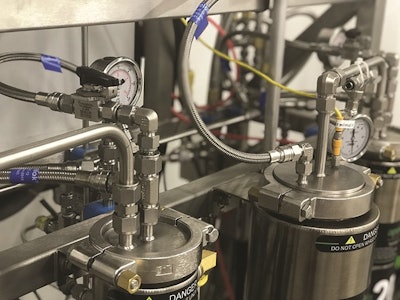
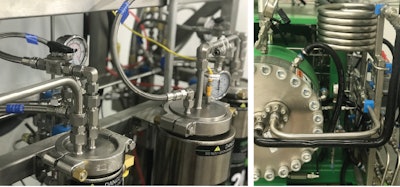
Regular cleaning and maintenance of cannabis extraction equipment is key to ensure optimal performance and yield. Here are four things to consider when developing your cleaning and maintenance protocols.
1. Identify key components that make up your extractor.
These likely include extraction and separator vessels, solvent supply tanks, lines and connections, temperature controllers/chillers, and compressor pumps.
Familiarize yourself with each component and gain an understanding of how they work together to perform the extraction. This knowledge will help you to identify unique parts within each component that become dirty or worn during use and will need to be periodically cleaned or replaced. Understanding the system will also aide in troubleshooting should any problems arise.
2. Determine the cleaning/maintenance needed by each component and the frequency at which it needs to be performed.
To keep your extraction system running properly and avoid downtime, determine what cleaning and maintenance needs to be performed and when. Much of this information can be found in the user manual for your extractor, including recommendations on timing. However, differences in run parameters can impact wear and tear, so it is best to closely monitor your equipment and set a schedule based on your specific needs.
Regular cleaning of your extraction system is critical for optimal performance. Don’t cut corners—perform all cleaning procedures to meet or exceed manufacturer’s recommendations. Common cleaning procedures include performing extraction runs with no cannabis present, rinsing separator vessels and connecting lines with ethanol, and checking downstream lines/filters for carryover of cannabis extract. Proper cleaning will minimize the occurrence of many common problems including clogged lines/valves, poor separation and low yield. If you use the same extractor to run multiple strains (e.g., high CBD strains and high THC strains), it is best to thoroughly clean in between extraction runs to minimize cross-contamination.
Scheduled maintenance is also very important. For example: maintenance of a CO2 gas compressor pump. On a weekly basis, the oil level and running oil pressure should be checked and recorded. Changes in noise level or vibration while running also should be noted, as this could indicate a potential problem. Every month, the pump should be inspected for any loose connections and/or leaks, and the belt tension needs to be checked. The oil filter should be changed every six months, and the diaphragm replaced every 18 months. These activities will ensure that the compressor pump will operate reliably and minimize downtime.
3. Set a schedule and keep a maintenance log.
Once you identify what needs to be done and when, create a maintenance calendar for each extraction system you’re running so you know when routine maintenance should be performed. Ensure each extractor has its own logbook, and document all maintenance activities for easy reference.
4. Keep a supply of replacement parts/consumables on hand.
Anticipate maintenance needs–for any parts that may become worn or break over time (valves, belts, o-rings) or consumables (filters, oil, coolant). It is advantageous to keep a supply of these materials in house. This allows for quick repairs and minimizes extractor downtime. Keep an inventory log of spare parts and replenish as needed.