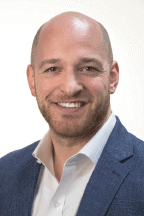
The extraction industry is booming. With more than 70 percent of cannabis and hemp retail sales coming from extract-derived products, and the CBD market alone anticipated to be a $22-billion industry by 2022, a growing number of entrepreneurs are capitalizing on this fast-growing segment.
Here, Precision Extraction Solutions’ Director of Business Development Kevin Serwatowski discusses the initial steps required to properly design and equip a cannabis processing lab.
1. My state is currently hemp- and CBD-friendly with plans to eventually allow THC processing. I would like capabilities to process both at some point. What are some considerations I should be aware of?
Properly planning a facility and your equipment selection upfront is key. This usually entails building infrastructure that supports both Class 1 Division 1 and Class 1 Division 2 areas, capable of housing both ethanol and hydrocarbon equipment. Because of the risk of cross-contamination, it’s better to segregate the CBD and THC processing areas (i.e., an ethanol CBD processing line and a hydrocarbon THC line), and design a GMP-friendly workflow that assures a proper and compliant layout.
2. What is the best solvent to use for extraction?
In general, ethanol is the preferred method for most CBD processors, with hydrocarbon (e.g., butane) being a great complimentary process. By utilizing both solvent types for hemp processing, you can increase the breadth of products you offer.
For THC processing, people generally like to use lower-quality “trim” for distillate production, which is often the most economical because of throughput with ethanol processing. Higher-quality material, like fresh-frozen marijuana, is best suited for hydrocarbon processing, which often is used in craft production for products such as live resin, shatter, and wax.
3. What is one thing anybody getting into extraction should budget for upfront and early on?
People tend to focus solely on equipment and infrastructure budget but often forget about allocating funds to the proper design of the facility. If 5%-7% of the estimated overall project cost is dedicated to hiring the right professionals to design a compliant, efficient, GMP-certified facility, you can expect to save large sums of money long term by doing it right the first time. It also ensures you are planning for the future and not just the current market environment.
4. What’s the minimum information we need to provide a manufacturer to get an accurate equipment quote?
At the very least, extraction equipment manufacturers like Precision need to know how much biomass you have available to you, how much you plan to process per day, and/or what your estimated budget is so we can advise accordingly. We released a great video (which can be found online here: bit.ly/Precision-Guide) that guides you through the types of questions we ask when you inquire about equipment.
5. What is one piece of advice you can offer when getting into extraction?
Don’t get wrapped up in the “flavor of the week.” There are a lot of misleading and opinion-based articles floating around the web. Do your research outside of standard online mediums. Get out and network at local events, talk to existing processors, attend classes, watch accredited webinars, and talk to the experts.