
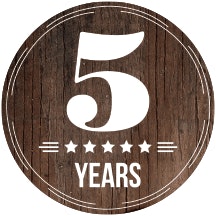
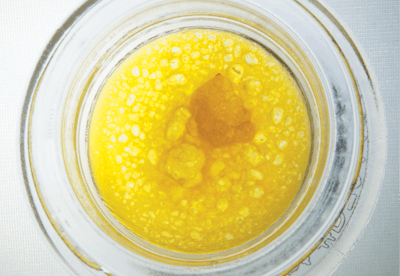
Demand for extracted cannabis products is quickly gaining traction. For example, edibles companies saw $1.5 billion in sales in major markets in 2017—and cartridge sales last year cleared $610 million in those same markets, according to Brightfield Group. When executed properly, cannabis extracts can be also used to produce other high-quality products such as topicals, transdermal patches, capsules and other concentrates. Yet, cannabis extraction can be a complex process-one that needs careful attention and a skilled workforce to be completed safely and efficiently.
The first part of this special extraction series explored the products that can be derived from cannabis’ essential oils-such as tinctures, transdermal patches, oral tablets, vaporizing and dabbing oils, and many more-and how those extract formulations can be achieved through supercritical carbon dioxide extraction (SCCO2).
The second installment of this series explores hydrocarbon extraction, butane in particular, including its functionality, laboratory requirements and what features should be considered during extractor selection.
Introduction to Butane
Before diving in, a quick review of relevant physical properties of n-butane can be helpful. Butane is a non-polar, Class 2 flammable liquefied gas that the Food and Drug Administration (FDA) has Generally Recognized as Safe (GRAS). It has a low boiling point of 31.1°F (-0.5°C), which is helpful when cold-boiling the residual solvent from the concentrate solution. This process leaves behind the temperature-sensitive terpenes. Many extraction technicians prefer to blend their butane with propane to create a gas mixture that will strip additional terpenes and purge more efficiently than butane alone. (The boiling point of propane is -43.6°F (-42°C).)
So, what features of n-butane (C4H10) make it an effective solvent in cannabis extraction? Hydrocarbons are arguably the most efficient solvent for cannabis extraction. Of the two standard hydrocarbons used for extraction (butane and propane), butane is a low-pressure system where extractions occur between 0 psi and 30 psi (pounds per square inch). One advantage of hydrocarbon extraction is the sheer number of products you can create from a single standard extraction without further refinement. Fresh, frozen extractions are the “fresh-squeezed juice” of the concentrate world. Currently, the preferred method is to separate the crystalline high-cannabinoid extract (HCE) from the aqueous, high-terpene extract (HTE). These fractions can be sold as separate SKUs or recombined at a ratio of the processor’s choosing to create a full-spectrum extract (FSE). Full-spectrum extracts are very popular.
A few shortcomings of butane exist, the primary one being its flammability and the regulatory compliance costs surrounding any hydrocarbon extraction. Hydrocarbons as extraction solvents are currently outlawed in Canada and some U.S. counties have enacted or are considering bans on hydrocarbon extraction. The second shortcoming is the lack of automated options. Unlike CO2 and the new ethanol systems, hydrocarbon extraction is still a very hands-on process, which can make extraction-outcome predictability difficult. (The hands-on nature of hydrocarbon systems puts added reliance on operator skill to achieve product consistency.) Only a few automated extraction machines are currently available to the cannabis industry; however, the price tag and throughput can be a tough pill to swallow for some. Automated hydrocarbon extraction systems will improve in quality and decrease in price as their safety features and internal monitoring systems become more reliable.
The Butane Process
Parent Material Quality
The starting material’s quality has a direct effect on the finished concentrate’s quality, regardless of extraction methodology. Always store plant material in a cool, dark place, and in vacuum-sealed or nitrogen-filled bags. These precautions limit exposure to ultraviolet rays, heat and oxygen, which are the three primary factors contributing to cannabinoid degradation.
The Wash
Cold butane is released from the solvent tank into the material column, where it slowly washes over the plant material, dissolving the cannabinoids and terpenes from the cannabis. Once the plant material has been washed, the solution can be collected directly, or it can be processed through an in-line de-waxing column.
Winterization/Filtration
Butane extractions are not typically winterized and filtered because the low extraction temperatures dissolve almost no chlorophyll and because the low temperature limits the amount of dissolved lipids/waxes. Additionally, many closed-loop hydrocarbon extraction machines come equipped with in-line de-waxing systems. Like winterization, in-line de-waxing requires a minimum -22°F (-30°C) environment, but it is a single-solvent system, where winterization uses a secondary solvent. In-line de-waxing employs the extraction solvent and takes advantage of the surface area created by baffles, stainless beads or other media to retain the undesirable materials as concentrate/extraction-solvent solution pass through.
For winterization, a polar solvent like ethanol is used at a 10:1 ratio, which is chilled until separation occurs. It is then poured over various-sized micron filters to separate out the lipids and waxes from the concentrate solution. While winterization is a more thorough process than in-line de-waxing, the polar ethanol might degrade some terpenes, which could result in a less flavorful product. Note that if the extraction system has in-line de-waxing built into the process, the technician should account for an additional 30 to 90 minutes of processing time.
Collecting Concentrate
Once the concentrate solution enters the collection pot, the residual butane is purged off passively by heating the vessel, which pushes the butane out of the concentrate solution back to the colder solvent tank. This process completes the “closed-loop.” Once the majority of the butane has been removed from the solution within the collection pot, the extraction technician collects the concentrate solution and places it on a parchment sheet or into a glass media bottle for separation.
Removing Residual Solvent
Purge methods and durations are dependent on the desired finished product. If the desired end product is wax, the concentrate solution can be whipped for a couple of hours to remove all residual butane. If shatter is the desired product, the concentrate solution is spread thin across Teflon sheets and purged inside a vacuum oven for a minimum of 48 hours.
Hydrocarbon System Considerations
When employing a flammable solvent like butane, it is important to understand that the processing laboratory-not only the extractor-must be in compliance with Occupational Safety and Health Administration (OSHA) and National Fire Protection Association (NFPA) regulations as they apply to flammable solvents and explosive atmospheres. These include implementing a Class 1, Division 1 (C1D1) extraction/manufacturing space that has gas monitoring, zero ignition points, adequate ventilation and a fire-suppression system that can negate catastrophic equipment failure. A well-ventilated space dedicated to temperature regulation where the chillers and heaters are plumbed into the C1D1 extraction space is recommended. There are also important oven, refrigeration and vacuum requirements (see OSHA 29CFR, NFPA 45, 99, 70, etc.).
Production Considerations
When it comes to the extraction system, these three variables are of the utmost importance:
- Ensure the machine is approved for use at the processing location. If the closed-loop system has not been peer-reviewed in that jurisdiction, then it will not pass inspection.
- Ensure the extraction system can handle the current throughput as well as the ability to scale.
- Control temperature. The equipment must be able to keep 25 kilograms of butane at -40°F (-40°C), while maintaining sub-cooled injection coils and cooling of the de-wax column. These ancillary chiller and heater expenses, including HVAC to vent the heat generated by these units, can run upwards of $50,000 on top of the closed-loop extraction system (CLS) price.
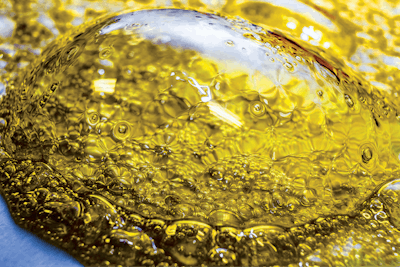
Production Bottlenecks
Below is an example of a production system followed by an identification of the bottleneck(s).
First, it is necessary to lay out the following assumptions:
- Starting material is trim
- Extractor input of 4,500 grams
- Return ratio of 0.15 (meaning the weight of extracts will be 15 percent of the weight of the plant material used)
- Five extractions per shift
- One shift per day/five work days per week
With hydrocarbon extraction, there are two bottlenecks within the process. First is the vacuum oven space required to purge the residual solvent out of the concentrate solution, and the second is packaging the finished product.
Extracting 4,500 grams of biomass every 90 minutes results in 22.5 kilograms (22,500 grams) of biomass per shift being extracted. Based on the average yield from properly grown trim (15 percent), 3,375 grams of concentrate is produced per shift. A 5-cubic-foot oven can hold about 1,200 grams of concentrate. Therefore, three 5-cubic-foot ovens would be required for each production day. Since each purging event requires 48 hours, a manufacturing laboratory would require a minimum of six ovens of that size to meet the weekly production of the extractor.
The packaging and fulfillment bottleneck is the most significant because none of the processes outside of labeling and sealing are automated. Currently, every process except labeling requires staff labor. Packaging will continue to be the most intrusive bottleneck in all successful processing facilities until the industry can figure out a way to automate handling various forms of concentrate and weighing it out to exact amounts.