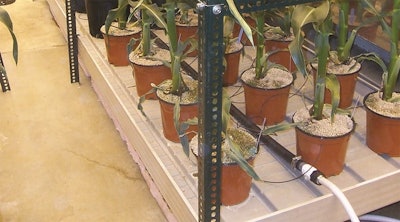

As a former research greenhouse manager at Purdue University for 20 years, I grew more than 150 species of plants. Even with 27 rooms and 60 growth chambers at the university’s disposal, we weren’t able to provide unique environments, substrates and nutrition programs for each of these species. What that taught me was that most plants can be grown with the same inputs: We grew more than 95% of those species in one of three peat-perlite mixes that varied mostly in their textures, from fine to coarse. We used the exact same fertilizer formulation for every single species, only adjusting strength by alternating with clear water irrigations. Most of the rooms were kept between 68 and 75 degrees Fahrenheit.
Corn was one of the few exceptions. This field crop was never bred to be grown indoors in a container. To grow it that way required all new protocols, and the story of how we developed them was how I learned about calcined clay. It’s a story that may be relevant for cannabis growers who mix their own substrates.
Calcined clay products are illite (non-expanding) clays that have been kiln-fired and ground to various sizes. The heat stabilizes them so that they don’t swell or turn soft with water. They are made in a process similar to expanded clay pellets that are popular in hydroponic growing but are much smaller and from a different clay source. They possess unique chemical restructuring that is “dependent on the nature of the clay and the temperature and duration of firing,” according to a 2014 paper by Dr. Bruce Bugbee of Utah State University. Interestingly, popular brands of calcined clay products are not designed for growing plants in containers. They are sold for improving drainage on baseball diamonds and horse-racing tracks.

Insights From Greenhouse Corn
Researchers grow corn in greenhouses in order to apply a uniform environment for their experiments and to increase crop cycles per year. Likewise, breeders conduct initial crosses under greenhouse conditions and assess traits before investing the time and resources required for field trials. Some of the challenges involved in growing greenhouse corn may sound familiar to cannabis cultivators. The crop exhibits an explosive growth period with a high demand for water and nutrients. It is prone to micronutrient deficiencies. Corn is susceptible to multiple root diseases, exacerbated by over-watering. Multiple stages of the crop are grown in a single room, including hybrids, inbreds and research mutants, requiring hand-watering decisions to be made on a pot-by-pot basis. These watering decisions are easy enough for an experienced grower, but the size of some operations requires multiple employees rotating shifts, some of them less experienced.
Lastly, growing corn in greenhouses is too often based on anecdotal information. Many facilities had a protocol based on “artistry” rather than measurement. Some used soil or amendments only available locally or non-standardized containers.
We wanted to develop a protocol for greenhouse corn that was repeatable and scalable, to be used by any size operation, with standard components that would be available across the country. We hoped this would not only help us but push plant science forward, beyond what we were doing at Purdue University.

Research had validated calcined clay as a potential soil amendment or hydroponic medium since at least 1987, and both NASA and the Canadian Space Agency had experimented with it. As a soil amendment, calcined clay improves drainage like sand or perlite, but can hold and release nutrients to plant roots with its high cation-exchange capacity (CEC). The water-holding capacity is surprising for something that looks like gravel. After the heating process, calcined clay is mostly made up of air. It has 74% pore space, more than half of which can store water that is available for roots to extract.
Additionally, its stability keeps it from degrading as quickly as other ingredients.Despite these benefits, the weight of the calcined clay has kept it from being commonly used in commercial horticulture production. Shipping costs of plants in containers is often based on weight. (Reducing the weight from soil and sand was the primary reason the horticulture industry adopted light-weight substrates of peat and perlite in the 1960s.)
The cost of calcined clay is also a factor: It is typically much more expensive by volume than a commercial soil mix.
_fmt.png?auto=format%2Ccompress&fit=max&q=70&w=400)
A Protocol for Clay
I took a backwards approach to developing our greenhouse corn protocol. Most growers start with a substrate and then develop an irrigation and fertilization program from there. Because water is the most problematic greenhouse input, I started with an irrigation and fertility schedule, then built a substrate that could be compatible. I wanted to water automatically with drip irrigation multiple times per day using fertilizer solution at every watering.
Incorporating field soil into peat was commonly suggested for corn, but I wanted to avoid soil. One reason was the cost and time to identify a suitable site of clean soil, then to dig, dry, grind and pasteurize it to eliminate weed seed and harmful organisms. Cleanliness and aesthetics were other considerations: Nearly every facility I’ve been in that grinds and mixes with field soils has a fine film of silt coating the walls, floors and equipment, which smears like mud when wiped down. Lastly, field soils reduce the drainage of a container mix, even if incorporated at just 10% of the volume. Their use would not allow frequent automated irrigations.
Calcined clay granules could be poured straight from the bag for mixing, provide a high CEC and improve drainage for frequent irrigation. I began trialing it and other soil mix components at rates of incorporation of 25% to 100% final volume.
After conducting 24 controlled studies, we concluded the best root substrate was a commercial bagged soil mix incorporated with calcined clay granules at 50% final volume. This allowed us to irrigate the plants automatically, with the same programming for entire rooms, despite differences in size, vigor or growth stage. Plant quality and size improved visibly. Measures of leaf greenness with a chlorophyll meter indicated a 60% increase over plants grown in a commercial peat-perlite mix. Iron chelate drenches were not necessary.
We reduced hand-watering, saving labor. Fungus gnat infestations were reduced. Other insect infestations were reduced indirectly by not having a worker brushing up against plants while hand-watering. Root diseases were no longer an issue, eliminating any need for fungicidal drenches. We could still sow seed directly into the soil mix and observed excellent germination.
We were able to reduce pot size from 5-gallon to 2-gallon, as the larger pot had been necessary to reduce dramatic swings in soil moisture. Our system was, for all intents and purposes, hydroponic, so the substrate was always moist but contained suitable oxygen due to the pore space between substrate particles and within them.

Calcined Clay Considerations
I want to be careful that I am not prescribing calcined clay as a silver bullet. One study showed that 1:1 mix of field soil and peat moss had greener leaves and higher seed yield than our recommended mix with calcined clay. But, as I’ve previously described, that system depended upon excellent hand-watering otherwise prone to nutrient problems and disease, as well as other management challenges. Essentially, adding calcined clay to a soil mix doesn’t make a perfect substrate, but makes one more forgiving of human error.
In his 2014 paper, Bugbee describes the potential for manganese (Mn) toxicity with calcined clays, particularly the smaller-sized particles that are about the size of river sand. He suggests calcined clay materials be pre-rinsed to reduce this possibility. We did not observe toxicity in our corn studies, even though we didn’t pre-rinse the calcined clay. This is most likely because we used the larger granules, diluted it 50% in the soil mix and irrigated frequently with high leaching rates. However, we did observe Mn toxicity growing rice in the smaller-grade calcined clay. We didn’t pre-rinse, and our sub-irrigation protocol greatly reduced leaching.
We shared our corn protocol with the global research community in 2010. It included materials and method descriptions, photographs and data. We published the recommendations as a series of e-publications in FAQ format that were discoverable through standard search engines. Written in plain language, our audience was not just professors, but their technicians and students, as well as researchers and breeders in the commercial ag industry. These e-pubs have been downloaded more than 30,000 times in more than 103 countries. Many of our colleagues at universities in North America adopted and improved the method.
Again, while not wanting to present this amendment as a panacea, we did find other crops benefited from calcined clay incorporation, such as rice, turfgrass, switchgrass and other biofuel crops, as well as crops with high iron demands such as petunia and citrus. We often added it to seedling mixes if the species was prone to root disease.
Growers who are interested in experimenting with calcined clay should note that some brands are OMRI-listed. Mother plant production might be a particular target of trialing, as the stability of the granules would improve the longevity of the substrate.