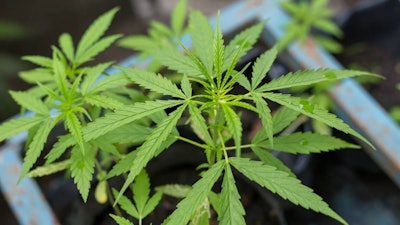
Editor's note: This article was originally published in 2017, and costs of production and other dollar figures reflect what was current at that time.
As cannabis supply increases, product prices decrease. As prices decrease, the cost of production becomes even more important, and producers are forced to adopt more efficient practices.
Extremely low costs of production, which are difficult to compete against, are already being achieved. Recently, a Canadian cannabis producer announced its new cost of production of raw, dried cannabis: now $1.11 per gram, down from $1.73 per gram—a 36-percent reduction. An Israeli producer I consulted for was able to achieve a 50-cents-per-gram production level utilizing greenhouses more than five years ago, with no compromise to the quality of the finished product.
As they say, “Time is money,” so you must direct your workflow efficiencies to cultivation, processing, extraction and super refinement.
For starters, consider how much time it takes to properly decontaminate and clean every surface in the growing environment between crop rotations. TIP: If you were to intentionally minimize surface areas to eliminate unnecessary cleaning, you would then minimize cleaning effort and labor. Filling a cultivation environment with anything not required is inefficient.
TIP: Another time- and labor-saving practice is to, whenever possible, design your facility to allow vegetative growth and flowering to take place in the same spot. It is an inefficient practice to move plants from one area to another unless you have one common vegetative area that feeds multiple flowering areas. TIP: In that case, it is much more efficient and cost-effective to employ seeding and potting machines, and have conveyor belts, not people, to move the plants. Incorporating such automation may make sense if your facility is 10,000 square feet or more; for smaller facilities, this type of automation is cost prohibitive and cumbersome.
Lately, I see many new large greenhouses being built with little or no realistic forethought. I recently viewed online construction photos of a cultivation facility’s greenhouse foundation. I called the person who posted the photo and asked why they had installed floor-heating capabilities when their geographic location would never require or utilize it. I asked other specific questions regarding the layout, design and construction of their greenhouse. The person’s reply was that the investor had dictated to the greenhouse manufacturer the exact specifications of the project and had requested “all the bells and whistles” without accounting for location-based needs.
In addition to wasting money on the floor heating, the investor failed to ask the grower for his input on the true facility requirements, from cultivation aspects to pest and disease prevention, let alone addressing any type of efficient practices. Nor did the investor see a necessity to construct a completely sealed structure, increasing its susceptibility to pests and diseases.
Their greenhouse may be successful in cultivating plants, but it will not do so efficiently. TIP: It is important to consider all environmental and cultivation needs during facility design, and spend money where it will be most effective, while eliminating spending on unnecessary expenses, such as floor heating in a warm climate.
As prices fall, it will become more difficult for indoor producers to compete with properly grown product from an efficient greenhouse. But, if you are a greenhouse grower who is not efficient, you mitigate the strategic advantage of utilizing a greenhouse which is, ultimately, less costly for energy needs. Again, if a greenhouse is not properly sealed, it is seriously susceptible to both pests and diseases, increasing labor and costs invested in pest prevention and treatment.
The efficiency of a greenhouse begins, however, with geographic placement. TIP: It is most efficient to construct a greenhouse where it is cheapest to heat and cheapest to cool, with major consideration given to the availability of skilled labor, supplies and points of distribution. Consider additional production costs, such as shipping supplies to a remote location, or transportation costs and employee time to deliver product to retail customers from that location.
TIP: You must also design your facility with a lean workflow in mind from the beginning, whether you are growing indoor, in a greenhouse or even outdoor (for some applications), and whether for cultivation or for processing into concentrates. TIP: For example, how close are your trimming and curing rooms in relation to your flowering room? Shorter distances lessen the movement throughout the facility. The same goes for your extraction lab.
TIP: Simply implementing automated systems will do wonders for your facility’s efficiency—from automating irrigation and feeding, to centralizing your climate control, switching to full or part machine trimming, using drive systems for your blackout curtains, and more.
TIP: Also consider where your automated controls are centralized, for HVAC and for irrigation, for example. You want to be able to access these points easily.
TIP: Even the location of your headhouse is worth considering. While storing supplies away from grow rooms is advisable, locating them too far from where they will be used also adds to additional labor and time in moving supplies from storage.
All aspects must be considered prior to construction.
Efficiencies Beyond Flower Cultivation
Production efficiency obviously translates to processing, extraction and refinement, as well. Ten years ago, all cannabis buds and desirable materials were dried or turned to water hash, and sold. Today, future cannabis production is trending toward processing product into concentrates of one form or another, for a multitude of uses. This typically translates into no drying, trimming or curing because wet plant extraction yields higher percentages of the available terpenes—very valuable components for many products and uses. TIP: This type of production method is much more efficient than drying, trimming and curing all the cannabis produced. It requires much lower labor costs, and the costs of building drying areas are minimized.
Carefully consider which extraction-produced offerings you plan to create, so that you select equipment that makes sense within your business plan.
I recently saw a social media posting by a vape pen cartridge distributor using two filled cartridges as examples. One cartridge had been processed once, utilizing a thin film-wiped distillation apparatus. The other cartridge had been distilled three times. The single-distilled cartridge had a darker-amber color caused by flavonoids, pigments and other undesirable compounds. The lighter-colored cartridge had those compounds removed via triple distillation. The person posting the photo was pointing out the difference in both the color of their distillate and the THC percentages of both cartridges. He also was noting price differences, from a cost of production standpoint, stating that each time it is refined and distilled, the cost of production increases. Thus, the cost of production of the triple-distilled example had almost exceeded its wholesale value, but still has to compete in sales with every other cartridge on the market.
Clearly, the manufacturer with the lowest cost of production has the potential for the highest profit margin. Combine that with the fact that distillation produces a generic flavor with no strategic advantage over a competitor, and the vape pen cartridge market will soon become very competitive, to say the least. The only realistic option one would have in this situation is to scale up production, efficiently.
Large-scale extraction equipment and associated materials are expensive. TIP: When you purchase quality equipment, you first must seriously evaluate exactly which products you want to produce, and what is the most cost-effective and efficient method to produce such goods without any compromise in quality.
TIP: Some methods of extraction require very skilled labor, especially when you are aiming for production in the most efficient manner that can result in superior quality. Some alternative methods may require only skilled labor. Price differences in dollars per hour between skilled and very skilled labor can range from $25 to $50 per hour.
One example of an extraction apparatus that requires only skilled labor is the Red Rabbit Extractor from StartrikeStainless.com, which works by using ethanol alcohol to basically dissolve and wash off the resin glands. This process also would require someone fluent in the use of additional equipment, such as a rotary evaporator to allow for recovery of product and of the ethanol for reuse, as well as a cryogenic freezer to enable winterization, which then requires filtration. After all that, the resulting product would then need to be distilled to produce a superior and refined product.
A skilled operator of sophisticated apparatus can cost as much as $25 to $50 per hour and require training with the equipment manufacturer as well as further refinement training later. This can mean a costly investment in that employee. A potential risk to consider is that you will have made an investment in that technician who, when her free education ends, can decide to look for better opportunities because she is now properly educated. She could also decide to start her own competing business. Therefore, you would have just paid to create your own competition.
TIP: So, it is important to choose your extraction technician carefully. Search for someone who is a legitimate chemist with a degree, or a candidate who is already familiar with the equipment and processes you end up employing. Treating employees well and offering good benefits can also help ensure your newly educated employee will stay.
With all that said, you must logically approach the design of the processing facility with a constant focus on cost of production without the compromise of quality. You must also diligently do your homework regarding the products you intend to manufacture from a demand standpoint. Do not make anything you’re not sure the market desires.
Kenneth Morrow has been writing cannabis-related articles and books for more than 20 years. He owns Trichome Technologies, a cannabis R&D company. He also is an award-winning grower and breeder. He has made contributions to many of today’s extraction methodologies and holds multiple patents. He consults on all cannabis-related subjects. Find him on Facebook at: Trichome Technologies or Instagram: TrichomeTechnologies.