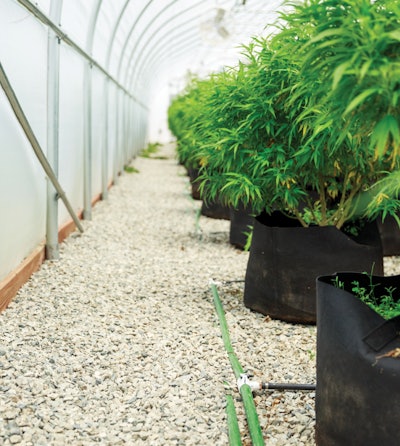
At the end of any facility-design and construction project, cannabis cultivators may feel eagerness and excitement to execute the next steps of their business plans. However, despite the anxiousness, many can’t help but look back with a sense of regret on the things they would have done differently had they known at the start of design and build-out what they know today.
Whether it’s something as seemingly mundane as what containers to use for your growing medium or something more serious and irreplaceable such as low-ceilinged rooms, follow these final facility-design tips to avoid feeling remorse at the conclusion of your build-out.
1. High ceilings must be incorporated into any sealed environment.
Low ceilings are a poor choice for both indoor and greenhouse facilities, as they can be detrimental for environment control. Cultivation areas with low ceilings heat and cool more rapidly compared to high-ceiling environments. Some greenhouse manufacturers recommend 18-foot ceilings to aid in environmental temperature and humidity control; others recommend 16-foot greenhouse ceilings. It is easier to control rapid temperature and humidity fluctuations between night and day in a larger environment.
2. Choose simple and high-quality irrigation systems.
An ideal irrigation system is simple, easy to maintain and efficient. Many high-quality drip emitter options are available today, all of which offer varying GPH (gallon per hour) delivery capabilities, designs and benefits to the user. Some require less replacement and maintenance than others. Drip emitters deserve thorough investigation prior to purchasing and are not something on which a grower should skimp. Nutrient delivery or dose meter systems, along with ebb-and-flow systems, require thorough research as well. Hand-watering allows for great water-delivery control, but is very labor intensive and requires a staff that understands all aspects of watering and deficiencies, including over-watering and under-watering ramifications.
3. Ensure that you have environmental-control-recording capabilities.
The ability to record all environmental aspects, yields and related information from the outset is paramount. You must have all relevant information at your fingertips. A review of all available information is the only way a cultivator knows if he or she is doing better or worse throughout harvest cycles. It provides an analysis of the different influences on yield and compound concentrations, and how they contribute to yield, cannabinoid and terpene profiles, and more. Therefore, the ability to log, record and track all aspects of a grow must be incorporated from the beginning, not as an afterthought.
4. Include a research and development area for trials and concept proving.
It is a nice luxury to have, whenever possible, an area dedicated to research and development where you can test new technologies, equipment, facility components or methods that may better suit your needs.
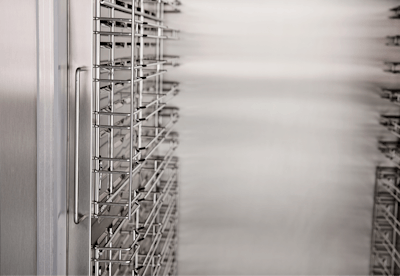
5. Keep in mind your media/medium container.
From fabric pots to root-development pots, many container choices are available to cultivators. Each requires consideration regarding your exact needs. Consider factors such as whether your ideal container will be utilized once, or sterilized and reused. Disposing of containers after each use has increased replacement costs, but cleaning and sterilizing for reuse are costs to consider as well.
The choice to grow large plants in large containers or small plants in small containers resides with the grower and is most often influenced by his or her methodologies—although, it is sometimes dictated by the facility design or the situation. (Read more about container size in part II of this series in the May issue of Cannabis Business Times.)
Regardless of your preferences, always consider the pluses and minuses of all of your options regarding container type, size and associated costs.
6. Don’t forget to incorporate automation.
Legalization has enabled legitimate cultivation-equipment manufacturers to design, market and sell equipment to cannabis producers—from potting machines to conveyor belts to trimming machines and more—and also for producers to seek investment, making it possible for them to purchase automation equipment. With wholesale margins for cannabis dropping at a rapid rate, cultivators must seek out automation methodologies to minimize labor costs.
7. Know your prospective facility's water availability.
Many factors determine a potential property's viability for horticultural use. Besides power availability, water availability is also a major determining factor. Water composition, storage, filtration, sterilization capabilities and the water source’s GPH availability must also be considered. And don’t forget to consider whether you have the ability to collect, capture and reuse all water including water collected from the greenhouse roof. (Read more about resource availability in the April issue of Cannabis Business Times.)8. Consider added security features in remote locations.
Large-scale greenhouses are being constructed predominately in remote/rural agricultural areas. Remote locations, however, require time to reach, and law enforcement works on a priority basis; therefore, cultivators should design their facilities with security measures to slow down thieves as much as possible and give law enforcement ample time to arrive. Whether that means incorporating secure double-fencing, audible alarms or a combination of technologies, find what works best for your location and budget.
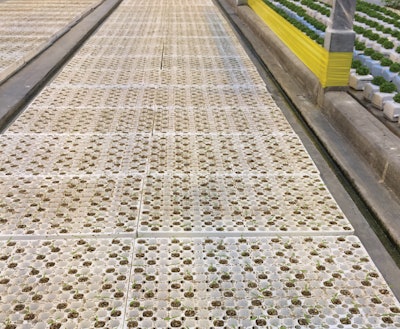
9. Dedicate a cleaning and equipment-decontamination area.
The first part of this series explored the need for employee-decontamination areas, but dedicated equipment-decontamination areas are also essential for any cultivation facility. It is imperative to be able to thoroughly disinfect all equipment with minimal labor. This includes overhead boom sprayers as well as floor drains that allow employees to spray, scrub and rinse equipment efficiently.
10. Think about product storage.
After working hard to produce good product, it makes perfect sense to store it properly in a purpose-built storage area. Subzero walk-in freezers are preferred for storing dried and cured raw cannabis, material intended for extraction or finished extractions. Therefore, when designing your facility, consider incorporating a large subzero storage area, preferably near the extraction, drying/curing and packaging areas to minimize distance traveled by employees each day.