Designing and constructing a large-scale cannabis production facility can be a daunting prospect to say the least. In some ways, it is seemingly straightforward, but many factors can be overlooked or underestimated. Something as simple as under-sizing environmental chilling capabilities can have disastrous results, and will cost approximately the same to remedy as doing it correctly from the start. In addition to the 20 tips provided in Cannabis Business Times’ April and May issues, here are 12 more methods for mitigating possibilities of costly design and construction mistakes, as well as production interruptions.
1. Plan for proper plumbing.
When growers expand incrementally, it is common to carry over practices that were previously utilized in small-scale growing. A mistake I often witness is the under-sizing of plumbing. I have seen many cultivators fail to properly estimate their water drainage capabilities, resulting in either slow drainage or worse—water can back up from failure to properly size drainage lines. Slow drainage can potentially cause many problems, including excessive saturation of growing media, proliferation of disease and pests (think: standing water in trays waiting to drain), and potential flooding. It can also contribute to elevated humidity levels in grow rooms.
2. Make the correct lighting choice.
Many lighting choices are available to cultivators nowadays—and whether you are growing indoors or in a greenhouse, proper lighting levels must be maintained at all times, in all stages of growth. Light levels directly correlate to the amount of biomass, as well as cannabinoid and terpene potential. In addition to determining proper light levels, implementing a specific light spectrum for a given growth stage is just as important. Today, lighting manufacturers frequently conduct studies that focus on both light levels and spectrum, specifically for cannabis cultivation. Previously, many of the lighting influences on cannabis were primarily observation-based, but manufacturers are now investing in research and development and using hard data to determine lighting recipes for optimal cannabis production.
3.Choose manufacturers wisely.
Just as in lighting, new innovations and technologies in other facility-design components are rapidly being developed, tested and proven. That said, some technologies remain unproven. You’ll want to select all your cultivation-component suppliers after conducting research about those companies. To some degree, you get what you pay for with respect to purchasing less expensive technologies and equipment.
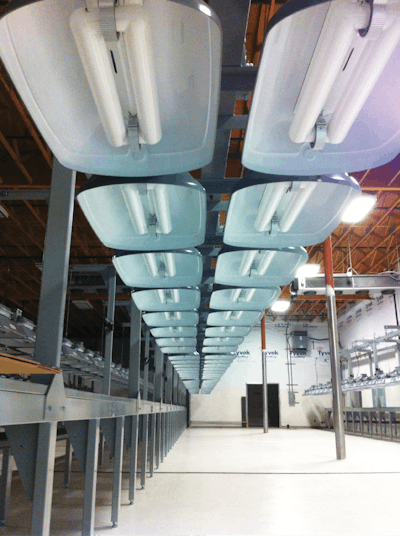
4. You must also continually evolve with new methods and technologies to be able to compete in a competitive market.
That said, you can also choose to spend your money with honest, innovative companies, which encourages further research and innovation.
5. Create your floor plan.
Conceptualize the layout of growth environments and both indoor and greenhouse bays early on, as redesigning an environmental layout is costly and labor intensive. Think hard about how you will utilize a given space and most efficiently capitalize on it. For example, having separate water sources, sinks and work areas minimizes employee movement and time spent traversing the facility in search of materials or performing duties such as cleaning tools.
6. Create dedicated environments for clones, seedlings and tissue culture.
I’ve seen growers design facilities to maximize space. To do this, they attempt to incorporate hardening off and vegetative growth stages into one room/environment. While this can be achieved on a small to medium scale, it is not preferred in large-scale production, because multiple stages of growth require varying environmental controls rather than dedicated environments for specific growth stages or methods of plant replication. By having stage-specific environments, you can focus solely on the perfect refinement of an environment for a given stage, be it seedling, clone, tissue culture or hardening off. Regardless of the early stage, these plants should never occupy the same environment as the vegetative stages do, as each stage is unique, with specific requirements.
7. Place dehumidification systems and controllers/sensors properly.
Inexperienced growers may place dehumidification systems on the floor. Heat rises, and typically takes available moisture with it; therefore, the ceiling area of a cultivation environment is the warmest area, with elevated humidity. By having dehumidification systems at ceiling height, with humidity sensors at the plant canopy level—combined with proper airflow—you can properly maintain optimum humidity levels where it is most relevant.
8. Deliver CO2 efficiently and maintain desired ppm.
I’ve witnessed large-scale facilities attempt to maintain proper CO2 ppm (parts per million) by utilizing a series of tanks that require transport to refill, which is a poor utilization of labor. It is better to incorporate a large, stationary CO2 tank that is leased, placed outside of a facility, automatically refilled as needed and synced to work in unison with ventilation or HVAC systems. Multiple companies exist that provide the tank and the environmental controls to maintain set ppm levels.
9. Determine adequate environmental chilling capabilities.
Underestimating a facility’s cooling needs can be costly at the very least and catastrophic at most. It is crucial that you convey the true cooling needs of your facility to your HVAC engineer. Something as simple as underestimating the sizing of critical equipment, such as chilling units, can have very serious ramifications. Always give realistic information regarding heating or cooling to all relevant engineers. The heating and cooling capabilities should be designed to easily accommodate both the hottest and coldest days of the year efficiently, without overworking or compromising environmental conditions in any situation.
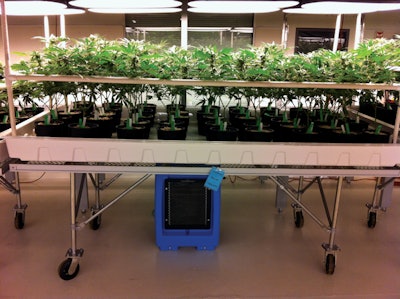
10. Establish sufficient power supply.
Before you purchase property or hire an architect to draw expansion plans, you must contact your power supplier to ensure power availability and be aware of all associated costs to upgrade your equipment or electrical system to compliant standards. Ask yourself if the power you require is currently available. Will additional power poles, wiring, etc., be needed? Or could you simply need a transformer addition? Determine what the time frame is to have necessary power enhancements completed. I’ve seen many seemingly perfect locations for greenhouse structures unable to be utilized because of the lack of available power. In some locations, getting power to the property can be excessive, and it may be a better option to look for a location elsewhere.
11. Know that your staffing plays a role in design.
Many owners have constructed facilities based on the specifications of their chosen lead, or master grower, only to find out too late that the grower was not qualified to properly design a facility due to a lack of agricultural-production experience. You must properly investigate the background and knowledge of any employee in any critical position—but especially the person in charge of facility design. He or she should understand both cannabis cultivation and real-world agricultural production. A person with both knowledge sets is the best choice to work with architects and system designers.
12. Consider the ramifications of your growing media choice.
To some degree, the growing medium you plan to use will dictate a growth method. There are multiple media options available to cultivators, from organic living soil, sterilized wood pulp/peat moss to no-till raised beds, puffed rock, soilless substrates and rockwool, just to name a few. To make the best selection for your business, ask yourself: Do you require sterilized soil, or will you incorporate predatory insects in your integrated pest management (IPM) program to manage any pests associated with unsterilized organic media, or would you prefer sterile rockwool media? Will you hand-water? Utilize drip irrigation? Use aeroponics incorporating puffed rock? Will you implement raised beds? Which containers will you choose: large for bigger plants, or small for smaller plants? Each method includes advantages and disadvantages when integrated on a commercial scale—not to mention having to adhere to stringent regulatory and testing standards for pests and diseases.
The consequences for making an uneducated medium choice can sometimes be troublesome and costly, to say the least. Puffed rock, for example, must be either sterilized or replaced after each growth cycle. Decontaminating a lot of rock efficiently can be difficult on a large scale, and replacing it after use is fiscally irresponsible and environmentally unsound if it ends up in the landfill. Re-using soil, on the other hand, is certainly environmentally sound, but also increases the risk of infection if the soil is not properly composted or sterilized prior to re-use. Raised, no-till beds are cumbersome in a greenhouse that uses rolling benches, and they require constant soil sampling and adjustment to prevent or minimize pH problems, mineral depletion or build-ups—but they are otherwise very efficient and require minimal attention.