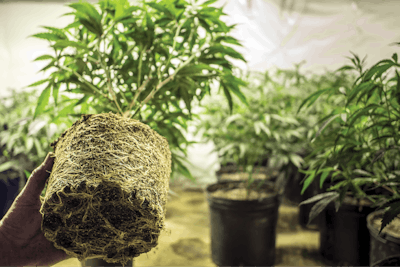
Take it from those who have made costly mistakes and learned from them—it is no small feat to establish a cultivation facility that is adequate and efficient for plant production.
In Part I of this column, we discussed design elements to consider when accommodating for pest prevention, airflow and construction. Here, we’ll touch on 10 unique cultivation-focused factors business owners must take into account before building or retrofitting their new operations.
1. Cultivar Choice
It will someday be paramount to have a strategic advantage over your competition by utilizing proprietary genetics that are not nor have ever been available to competitors. Cultivars that have never been released to the public will ultimately be considered unique by customers. To grow and sell the exact same products as your competitor provides no strategic advantage. If you know which unique cultivars you want to produce, you can then design your facility to best accommodate them and ultimately rise to the top of your market.
2. Pest-Free Soil
Many grows have been infected with aphid larvae, fungus gnat larvae or worse-from unsterilized soil. Most soil manufacturers sterilize their soil prior to packaging only to have distributors or retailers purchase in bulk and store the medium until needed. The longer the soil is stored and the more it is transported, the higher the probability of contamination. Improperly sterilized soil can harbor harmful pests as well. Whenever possible, purchase soil directly from the manufacturer to ensure that a sterile product you ordered is truly sterile (pest-free), and make sure to create space to store that product safely. Check with your manufacturer to learn specific medium storage requirements.

3. Lean Workflow
Cost of production is an important factor for any business. Understanding your complete production process allows a producer to calculate factors such as how long certain jobs or tasks take, and whether a different method is more efficient. A different method or mechanization of multiple tasks can expedite workflow and ultimately lower cost of production. Think about those processes as you’re mapping your facility.
4. Sustainability
Cannabis cultivation requires energy resources in one way or another-no matter the method-so it only makes sense to try to produce cannabis with as little an environmental impact as possible. These energy sources include the use of organic matter (i.e., peat, wood pulp, etc.) that make up the growing media, lighting, HVAC units and more. The failure to establish a set-up for the recapture and reuse of water is also wasteful, especially in drought-prone climates. Be sure to monitor elements like electricity output and thermostat calibration, water usage and more. Even better, integrate your automated systems as much as you can to save time, money and valuable natural resources.
5. Drying/Curing Facilities
As I’ve stated multiple times within these columns: One can cultivate the best cannabis only to destroy the quality components in the drying and curing process. By rapidly or overly drying cannabis, the terpene content is unnecessarily diminished, which diminishes overall flavor and smell. Improper drying/curing results in a product without optimal flavor and that is excessively dry, which can also cause the product to become brittle and burn too rapidly when smoked. Cannabis that has been dried over an extended period of time at temperatures that are too low presents problems as well, in that the resulting product retains a “green” chlorophyll smell and taste. Whether using a clothesline method, racking method or other method, design your drying/curing rooms so that they can be dark with adequate circulation. Rooms should operate at about 40- to 60-percent humidity, and between 70 and 80 degrees Fahrenheit.
6. Efficient Decontamination and Crop Rotation
This concept is simple: Less surface area in a room means less area to decontaminate. Excessive materials such as extra tables, trays, etc., take more labor and time to clean. A minimalistic approach is best. Minimizing areas to clean and making a plan for rapid decontamination between crop rotations (including flushing irrigation lines) reduces both labor costs and supply expenses.
7. Dedicated Aisles and Walkways
Some growers choose and design their facilities with dedicated aisles for workers to traverse while performing daily duties and plant maintenance. This creates inefficient use of valuable floor space. If you incorporate 4-foot aisles between each row, you are eliminating approximately 50-percent of your usable floor space, which is fiscally irresponsible considering the cost of lighting, environmental control, real estate, overhead, etc. Using a moving aisle whenever possible is always preferable over stationary aisles. Rolling benches create aisles that allow for maximum utilization of available floor space.
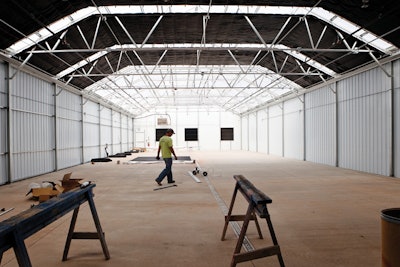
8. Containers
The larger the plant, the longer it has been growing and the greater the risk of potential pest or disease infestation. Most indoor and many greenhouse growers choose to grow shorter plants in more cycles rather than bigger plants in fewer cycles. This minimizes the risk of infection by allowing for more cleaning and decontamination cycles, giving the grower a chance to begin again with fresh stock and clean environments.
Another reason this method is beneficial is that those shorter cycles allow growers to reduce container size and use less soil/medium to fill them. Plants that will only be growing for 90 days do not require large pots, and there is no horticultural benefit to having large containers for short-cycle plants. I’ve seen grows that employ 25-gallon containers for plants that will only be in that container for 60 days. Larger containers do not always equate to larger plants. While typical for long-cycle, outdoor plants, the logic is irrelevant in short-cycle situations. Why pay for, store and/or dispose of resources your plants do not utilize? At the end of a grow cycle, container growers must inspect root balls after harvest to ensure they are getting maximum root growth, but also (and more importantly) to see if the plant roots utilized all available soil/medium in the time allowed. If not, then maybe a smaller container size is possible, which would also require less soil/medium.
9. Tissue Propagation
Cloning is a great way to replicate plants. But large-scale growers are beginning to investigate tissue culture as their preferred method of propagation. Tissue culture allows for the storage of tens of thousands of specimens/cultures in a very small space with minimal environmental controls. Tissue culture takes much longer to produce a plant than cloning-but at the end of the process, you end up with a clean specimen. Plus, clean genetics fetch a higher price.
10. Unnecessary Heating
Lately, I have seen a few commercial greenhouses being constructed on the West Coast, and a few of them have installed floor heating capabilities or heating systems to heat their beds/medium. In a properly designed and constructed greenhouse, one would never utilize the heating system in this region, ever. A West Coast greenhouse could easily maintain at least a 75-degree temperature, even on the coldest nights. Any heating equipment would be utilized rarely at best; therefore, in that specific geographic location, heating is deemed an unnecessary expense when considering both cost of equipment and the constant maintenance and upkeep that would be required.