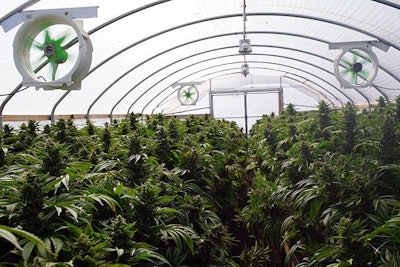

Authors’ Note: This article is the second in a series of guest columns by Resource Innovation Institute (RII). In Part I of the series, we introduced the “LED Lighting for Cannabis Cultivation and Controlled Environment Agriculture Best Practices Guide” and “HVAC for Cannabis Cultivation and Controlled Environment Agriculture Best Practices Guide,” which were examined by 29 peer reviewers. Key terms introduced below are italicized and described in more detail in the guides at ResourceInnovation.org/Resources. In three more editorials this year, Cannabis Business Times will feature snippets from Resource Innovation Institute’s Best Practices Guides to highlight more important considerations for growers and the supply chains serving them.
Special factors influence the targets engineers use to design the systems that heat, ventilate, air condition (HVAC) and dehumidify indoor grow rooms. The HVAC systems serving these operations also are impacted by several variants, and the factors affect environmental conditions in cultivation spaces and interact with and impact one another as plants move through growth cycles. Getting all the pieces working in the right sequence can be challenging, as moving targets are hard to hit without systems designed for varying conditions. To succeed, growers need to understand the key environmental elements and how they change one another, as well as their impact on capital costs, operational expenses, and yield (COY).
For starters, plants use light as an energy source for growth, and the amount of light needed each day changes as they grow. Plants also transpire like humans sweat, using cellular structures called stomata. Grow room air temperature and relative humidity directly affect plants and effective transpiration. When lights are on, room conditions are quite different than when lights are off; plants transpire differently when the sun is down, and it is important to know why and how.
Plant transpiration is impacted by several things including cultivar type, plant size, and amount of pruning (leaf density index). When cannabis is in late flowering, with its greatest leaf structure, a grow room will have its peak transpiration rate. For example, a 3,500-square-foot flowering canopy could transpire 500 gallons of water per day. However, when plants are in vegetative or early flowering stages, the rate may reduce by 80%, to 100 gallons per day. This is why it is so crucial for HVAC equipment to be able to satisfy widely variable room conditions.
Temperature and relative humidity impact vapor pressure differential (VPD), and influence plant vitality and yield.
To keep grow rooms within the environmental ranges preferred by cannabis plants for optimal production, sizing HVAC equipment properly is essential to ensure the systems perform their best. To size HVAC equipment accurately, calculate heat loads using target grow room conditions for various stages of plant growth.

Understand Your Loads
Cooling loads describe the energy that is continuously generated in the air as heat (affected by sunlight and electric lighting system (if used)) and moisture (affected by plant watering rate and hours of light and dark), which will need to be removed by the HVAC system. Sensible loads and latent loads are terms that describe the amount of heat and moisture, respectively, that need to be removed from the air to attain optimal conditions.
Sensible load is the dry load, as it deals with temperature, not moisture. Sensible cooling loads are caused by the sun and lights heating cultivation spaces (called sensible heat). Off-the-shelf HVAC equipment is usually designed for high sensible loads. Temperature targets for larger grow rooms result in higher sensible loads.
The type of light used to grow cannabis substantially impacts the amount of sensible heat in cultivation spaces. High intensity discharge (HID) light fixtures using fluorescent metal halide or high-pressure sodium (HPS) bulbs produce more heat than newer light-emitting diode (LED) light fixtures. Older LEDs produced more heat than today’s models, but usually produce less heat than HID light fixtures.
Latent load is the wet load, as it is driven by moisture in the air. Latent cooling loads are caused by plant transpiration and water evaporating in cultivation spaces, which are affected by watering rate.
Cultivation facilities are unique because the latent load is often greater than the sensible load (meaning more moisture than heat needs to be removed from the air), but off-the-shelf HVAC equipment is usually designed for low latent loads. Lower relative humidity targets result in higher latent loads.
The number of hours in which plants are exposed to light (photoperiod) is usually determined by cultivation approach, stage of plant growth, and facility location. Conditions in cultivation spaces change when lights shut off, decreasing plant transpiration, and varying the latent load the HVAC equipment must manage.

Sizing Capacity
The sum of sensible and latent loads determines the total cooling load a facility needs to offset with HVAC capacity. HVAC capacity can be described in a few ways, including tons, which is a unit equal to 12,000 British thermal units per hour (BTUs/hr).
Cultivators can use performance specifications from the HVAC manufacturers to evaluate how the systems can respond during different plant growth stages, as well as when lights are on and off. Manufacturer literature often lists total capacity, the rated heating, cooling, and/or moisture removal HVAC equipment can handle. Growers should examine both the sensible and latent capacities of the system, too. To achieve good operational efficiencies while maximizing yield, closely match sensible and latent capacity to the grow rooms’ cooling and dehumidification loads.
Sizing HVAC means choosing systems that can satisfy loads at design conditions. Growers’ target design conditions (for example, temperature and RH at which they want their rooms to operate) inform engineers of the peak load HVAC systems must handle. This is when target environmental conditions are at their most extreme and loads are at their highest. Engineers and equipment manufacturers should match equipment capacity closely to peak load, but also provide equipment that operates efficiently at part load conditions.
The table above illustrates the impact of target environmental conditions and light source on the required capacity of HVAC equipment to offset heat loads. Columns two through five describe dry bulb temperature, humidity, dew point temperature, and corresponding VPD for four different scenarios (rows). The three rightmost columns show three lighting system types commonly used for cultivation that result in three lighting power densities (LPDs) ranging from 35 to 60 Watts per square foot. These three values represent three grow room scenarios: LED light fixtures alone, hybrid LED and HID lighting systems, and HID light fixtures alone.
The values in the pink cells show the percent change in HVAC system capacity required to satisfy the target conditions for grow rooms with the three different lighting systems. The table uses a baseline cultivation scenario of a grow facility using LED lights and target indoor environmental conditions of 80 degrees Fahrenheit and 60% RH. This baseline cultivation scenario could require a HVAC system with a capacity of 40 tons. The values in the pink cells are described as percentages, where the baseline cultivation scenario of 40 tons is 100%; 100% of 40 tons is needed to satisfy HVAC loads for target conditions. The 11 other cultivation scenarios are described relative to the baseline; X% of 40 tons is needed to satisfy their different target conditions.
Keeping environmental conditions the same, cultivation spaces using HID light fixtures require HVAC systems up to 50% larger than rooms using LED light fixtures. If the baseline cultivation scenario of a facility using LED fixtures lowered both temperature and RH targets, 90 tons might be necessary to satisfy the higher loads, increasing system size by over 50%. If an HID grow operation lowers temperature and humidity targets, HVAC capacity might need to be increased from 60 to 90 tons, resulting in a system capacity 33% larger. Reducing VPD targets can require HVAC systems over twice as large.
Likewise, raising VPD targets can decrease required HVAC system capacity.
If HVAC systems for cultivation facilities are sized to meet latent loads, in most cases, integrated HVAC systems have sufficient capacity to meet the sensible load. In 10 out of the 12 scenarios (values in light pink cells), the necessary size of the HVAC system is determined by the latent (wet) load; most of the examples need more latent capacity than sensible. In the two remaining examples, the sensible load requires a larger system than the latent load, so the system selection is based on capacity to handle the sensible load.

COY Balance
Balancing capital costs/capital expenditures (CapEx), operating expenses (OpEx), and yield (COY) is the goal of a highly efficient and productive cultivator. Many design decisions affect COY and impact profit. It’s important to know the ways HVAC solutions can help cultivators achieve profitable operations.
C (CapEx): A typical commercial HVAC system not built for a cultivation facility’s high latent loads may have lower capital costs; however, choosing more efficient systems that can satisfy varying environmental conditions can be worth the slightly higher expense. Commissioned and maintained properly, a high-performance HVAC and lighting system might have a 10% to 20% higher upfront cost but can reduce recurring operating costs by 15%. Paying lower energy bills increases profit margin year after year, freeing up money in the budget for capital investments for improving cultivation processes and product quality.
As evidenced in the table, careful evaluation of optimal temperature and humidity targets is critical. The design criteria that a grower selects will have a significant impact on the capital and operational costs. Careful consideration should be given to defining the temperature, RH and VPD set points, to avoid oversizing the capacity of HVAC equipment.
O (OpEx): Off-the-shelf HVAC equipment may seem affordable on Day 1 but can make up 45% of a facility’s operational expenses from higher energy use and utility costs. If the only option is to work with off-the-shelf HVAC equipment, cultivators can adapt by carefully choosing target indoor environmental conditions, including higher VPD targets. This can somewhat reduce operating costs; however not every HVAC system can maintain tight tolerances to maintain those design conditions, and this approach may not always result in energy savings.
Choose appropriate design temperature and humidity targets to minimize operational expenses. Aggressive targets for indoor environmental conditions lead to oversized equipment and higher operational expenses.
Y (Yield): A properly optimized and tightly controlled facility allows cultivators to increase yield, which directly improves profitability. Early design decisions with proper communication with HVAC design engineers are key to improving yield outcomes.
Successful cultivators have a long-range vision and seek to balance COY factors. Focusing only on lowering capital costs can often increase operational expenses. Utilizing HVAC equipment not tailored to your operations will always result in increased energy costs from poor equipment performance, which can lower plant yield and significantly negatively impact profit.