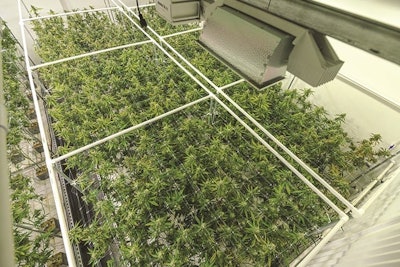
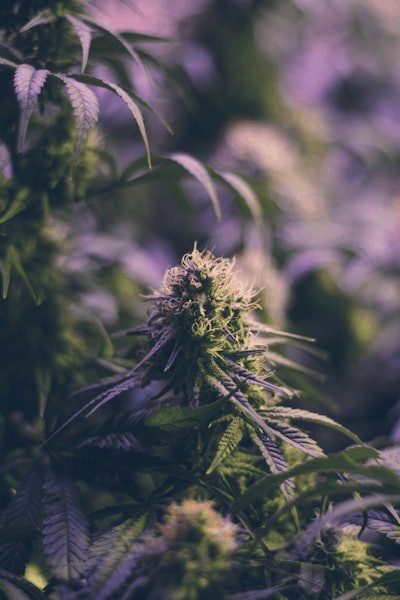
Indoor cannabis producers have equipment that gives them incredible power: They can create and control their own suns (aka lighting systems), have a plethora of automation tools available to cut down on manual labor, and can fine-tune their temperature, humidity and other environmental conditions to whatever best suits their crops.
With great power, however, comes great responsibility. Without proper due diligence and constant monitoring, one small slip up can lead to cultivators “bombing” an entire flowering room to cut losses on a pest-infected or damaged crop. A bigger mistake can lead to facility contamination and losing even more work.
Here are three common problems that can afflict an indoor cannabis facility and tips on how to troubleshoot them so growers can avoid losing their crop, and their shirt.
(Editor’s Note: This is part 3 in a three-part series. Read part 1 on troubleshooting greenhouse problems here and part 2 on addressing outdoor issues here.)
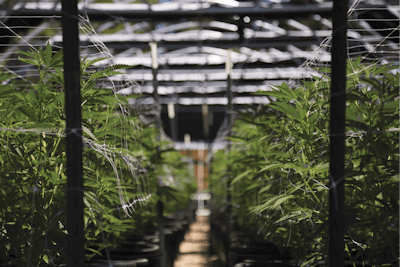
1. Common problem #1: Environmental issues throughout the facility
An indoor grower’s HVAC system is one of the most valuable assets to the operation. Without a properly calibrated HVAC system, there is no way a grower can maintain an optimal environment for cannabis cultivation. Luckily (relatively speaking), a faulty HVAC component can typically be easy to spot, as its effects on room temperature and humidity should not take long to manifest. Significantly warmer or colder rooms compared to set ranges, condensation on walls, or rooms that leave growers with dry throats because humidity is too low are all signs that the HVAC system needs servicing.
All HVAC systems must be regularly serviced—at least quarterly—and maintained to operate efficiently. Many systems come with periodic servicing that is covered either by the manufacturer or an independent contractor (growers should consider asking HVAC suppliers about their warranty and servicing policies when shopping for systems). During scheduled visits, independent contractors will perform a systems check on the HVAC unit. Growers with engineering backgrounds or with an engineer on staff can forgo these visits and calibrate their own equipment. Otherwise, it’s best to leave the fine-tuning to independent contractors and service experts.
Thermostats also should be calibrated periodically. Signs of defective thermostats can include: elevated temperatures during the wintertime, cooling or heating staying active for too long, and/or cooling or heating not kicking on fast enough. Verifying that the thermostats are functioning properly can be done prior to the winter/summer seasons to ensure efficient operation. Growers should make sure their contractor or engineer verifies the differential (the point at which the system kicks in or turns off) is properly set.
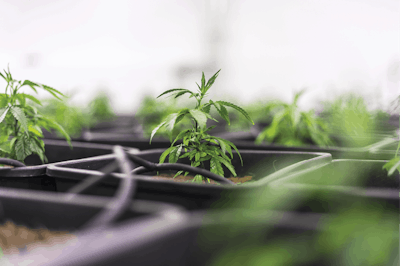
Common problem #2: Crop contamination
It doesn’t take long for a contaminant to proliferate in a tightly controlled environment because, as it turns out, the ideal climate for cannabis happens to be the ideal climate for many of the plant’s afflictions.
In most facilities, there are four main potential sources of contamination:
- Unfiltered and unsterilized incoming air from improperly sealed building and/or inadequate air filters
- Staff and visitors
- Unsterilized soil, unsterilized water and other polluted materials
- Contaminated genetics.
Each contamination source requires a different approach after the pest and/or disease outbreak has been addressed or contained. Besides regular maintenance of their ventilation systems, growers in wildfire-prone areas where smoke and ash can fill the air at certain times of the year should strongly consider incorporating a HEPA filtration system to clean the incoming air from all pests, molds, diseases and other contaminants. Considering the 2020 West Coast wildfires were the worst in recorded history, and data shows that they’ve been getting progressively worse over the past decade, it stands to reason that more fires will happen in the future.
If HEPA filtration is not possible, growers also can purchase a multi-stage, pre-filtration system to prevent ash and smoke from contaminating the HVAC equipment and smoke from entering the cultivation rooms. To ensure best results, the multi-stage system should be custom designed in collaboration with the system manufacturer.
Contaminations can sometimes come from staff members and visitors not properly adhering to sanitation protocols. All visitors should be required to wear Tyvek suits (or another covering over their normal clothes) and either wear shoe coverings or step into a disinfecting cleaning solution to clean the bottom of their shoes. Pharmaceutical-grade facilities also should create a barrier with a clean room equipped with air blowers that can decontaminate visitors and personnel each time they walk into the facility. Cultivation staff should be scouting for pests and diseases within the crop, not be a vector for introducing them.
All cultivation inputs that are being introduced into the facility, including soil, should be quarantined away from the rest of the production areas to ensure that pests aren’t being brought in by an unwitting soil shipment. The same applies to any and all new genetics and clones, even those from trusted breeders and seed producers.

Common problem #3: Plants yellowing or bleaching at tips
If all the climate systems are confirmed to be functioning properly and there are no pest and disease vectors, yet the crop is still struggling, or worse, dying, growers must look at their nutrient delivery system.
As stated in the two previous articles in this series, it is very important to be proactive when it comes to maintaining and servicing watering and fertigation systems. Broken filters, drippers and pipes, as well as leaks can all cause major problems for a grower if left unchecked, from imbalanced nutrient delivery to water-borne infections.
Growers can potentially spot a leak or a busted pipe by looking at how the plants are performing in different areas of the room. For example, if plants near the room’s entrance (and thus at the front of the fertigation line) are healthy but start to wilt after the first dozen, then growers can look to see if there are any blockages or leaks causing the nutrient solution to not be delivered to those yellowing plants.
In the case of a blockage, growers can thoroughly clean and disinfect both the inside and outside of irrigation systems using a 10:1 water-to-hydrogen peroxide solution. Pre-mixed cleaning products also offer similar results in a ready-made solution.
Yellowing plants also can be a sign of nutrient deficiency, lockout and/or an antagonistic effect. Nutrient lockout can be avoided simply by monitoring runoff water and determining how much of each element the crops are taking up. If plants are yellowing and the pH is outside of normal ranges, antagonistic effects might be preventing the plant from accessing important nutrients. A thorough flush of the crop and subsequent nutrient adjustment should address the issue within five days.
If the fertigation system seems fine upon thorough inspection, verify whether the plants are too close to the lighting system. High-pressure sodium (HPS) and metal-halide (MH) systems generate a lot of heat when the lights are on and can cause yellowing and burning if the plants are too close to the light source. Likewise, while light-emitting diodes (LEDs) don’t generate as much heat as HPS or MH systems, placing plants too close to the fixture can cause “bleaching,” where the tips of the plants turn white from being so close to the intense light source.
Murphy’s Law tells us that anything that can go wrong, will go wrong. By being vigilant and proactive about problems whenever possible, growers can eliminate, or at least minimize, any and all potentials for disaster.