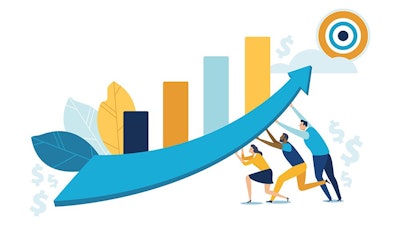
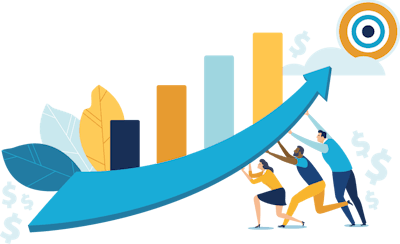
Recently, I’ve had several conversations with cannabis growers about the ongoing pressure they’re under to increase yields to make up for falling prices. As the legal market has matured in many states, the sale price for cannabis products has plummeted from where they started in the early days of the legal market. These lower sales prices have resulted in thinning profit margins and anxious investors who banked on high prices for years to come.
The reality is that many markets are becoming saturated with supply, leading to the frequently discussed concern that the industry is in a “race to the bottom” of sales prices. And still, even in the face of oversupply, investors and owners are demanding yet more yield and product to sell.
But what if the “race to the bottom” wasn’t about supply or sales price?
Weighing the Costs
When we talk about profits, there are two general ways to achieve it: either increase sales or reduce costs. (See sidebar below.)
On the surface, the urge to produce more when prices are low makes sense. Suppose an investor forecasted profits based on the assumption that indoor-grown cannabis would sustain a selling price of $3,000 per pound, and prices are now $1,500 per pound. In that case, it follows that doubling the yield would make up the price difference. But this focus on sales is single-minded in its objective, which only further drives prices down and exacerbates the “race to the bottom” until cannabis risks becoming a commodity market.
Fortunately, increasing sales isn’t the only option for increasing profit margins. Reducing costs can be just as impactful in widening profit margins, with added benefits.
The costs associated with producing and selling cannabis are many. Although most cultivation operations would consider the total cost of goods sold to calculate profit margin, this article focuses on the cost of production, namely the resources used specifically for cultivation and processing cannabis after harvest (i.e., drying and curing).
The ongoing operating costs of a cannabis cultivation facility includes labor, utilities (energy, water, sewer, carbon dioxide (CO2)), consumables (grow media, fertilizer, plastic stuff), service and maintenance, and, of course, taxes and fees. These costs are necessary to cultivate cannabis, but the magnitude of each of can vary greatly among operating types, grower practices and technologies employed.
After labor, energy use for lighting and HVAC is frequently pinpointed as the next-highest operating cost for indoor and greenhouse growers. Consumables and water may have much lower costs, but many growers express concern about the environmental impacts of overusing water, releasing phosphorous and reverse osmosis (RO) sludge into the sewer, and the dependence on plastic for everything from containers to irrigation tubing. Reducing the use of these resources, therefore, is not only economically favorable, but also environmentally friendly.
Increasing Resource Use Efficiency
In agriculture, we often think of Resource Use Efficiency (RUE), which is the efficiency attributed to how much product is produced relative to how much of a particular resource was used to produce that product.
Like net profit, RUE can generally be increased in three different ways:
- Increase outputs (supply) using the same inputs (costs)
- Decrease inputs (costs) with the same outputs (supply)
- Simultaneously increase outputs (supply) and decrease inputs (costs)
If a market is mature or the available space to grow more product is maxed out, then the best or only way to increase profit margins would be to focus on reducing the inputs (costs of resources) rather than increasing the outputs (saleable product). By doing so, you are inevitably focusing on maximizing efficiency.
One of the goals in agricultural production is to maximize the utilization efficiency of the resources provided to crops. Ideally, plants would use every joule of light, every drop of water, and every molecule of CO2 growers provide them. But in reality, plants don’t need or use everything we give them. That’s because sometimes we give them too much on purpose (flushing with water at the end of flower) or because they simply can’t use that much (high CO2 levels when temperatures are low). Finding the optimization point between different growth variables is essential to maximizing resource use efficiency, minimizing inputs and lowering costs. By managing the inputs to plants, growers can achieve more predictable production outputs and steer crops toward more profitable outcomes.
One example is managing vapor pressure deficit (VPD), a variable used to manage air temperature and humidity and control plant evapotranspiration in an indoor or greenhouse operation. Many growers tend to target a higher VPD (>1.4 kilopascal (kPa)) in an attempt to limit mold growth and turn flowers purple at the end of their life cycle. However, this low humidity condition can be detrimental to crop health, increase plant water demands, and increase energy use by the HVAC system to dehumidify the air.
When VPD is managed to cannabis’s sweet spot (1.0-1.2 kPa), several positive outcomes occur. First, the plant grows strong and healthy, free of calcium deficiencies and endowed with an immunity against diseases. The lower VPD also requires less dehumidification, which means smaller HVAC units or fewer standalone dehumidifiers would be needed to manage humidity, resulting in less energy use. The right VPD also puts less pressure on plants to transpire, resulting in less water and fertilizer use. By managing one variable—VPD—plants will yield more saleable product, resource inputs will be used more cost effectively, and, in turn, profit margins will soar. (A free resource to calculate VPD is available online.)
Another good example is the use of CO2 to increase the photosynthetic rate of plants to boost yields in greenhouse operations. Enriching the greenhouse with CO2 in the summer can be challenging and expensive because vents are often open or exhaust fans are running, discharging CO2 practically as quickly as it’s delivered. Further, because sunlight levels and mean greenhouse temperatures tend to be lower in the winter, many growers experience reduced yields in the winter, making it difficult to achieve production targets. By focusing CO2 enrichment during the winter months, operators can simultaneously achieve consistent yields year-round, use and waste less CO2, and increase annual profit margins.
Measuring Efficiency and Lowering Costs
One of the biggest challenges to managing resource inputs and reducing costs is knowing what variables to measure, how they affect crop productivity and health, and the initial costs to compare against when making changes to technology or growing practices.
One major obstacle to understanding and managing resource use is that many growers use different metrics to track productivity and profitability. In a recently published literature review1, we documented over 10 different industry metrics used to report energy use, including kWh/sf of building area, kWh/sf of canopy area, kWh/flower cycle, kWh/gram produced, kWh/gram sold, gram/Watt lighting, and gram/kWh total building energy use—just to name a few.
Not only are operators using different metrics to track resource utilization, but many are not tracking resource use inputs and costs at all. Or, if they are, they are doing it at the whole building level rather than at the subsystem level. Whole building meters are great for utilities to know what to charge for energy or water use, but they don’t reveal how much energy is used for lighting versus HVAC or how much water is used for irrigation versus toilet flushing.
To determine and reduce the costs of production, cultivators need more sub-metered data specific to cultivation inputs. These data are best tracked through a monitoring system and using power meters connected to subdivided systems at the electrical panel. There are also several plug-in power meters that can track electricity use at the outlet for equipment such as standalone dehumidifiers and fans that plugs into a power outlet.
By having these data, growers can better determine how changes in technology or operating practices could reduce inputs costs while maintaining or even increasing production. However, without these data or a consistent use of metrics by grow operators, it can be difficult to convince investors and owners that greater focus is needed on resource use efficiency as a means for increasing profit margins.
The Profit Denominator: Reduce Inputs to Increase Efficiency And Profitability
Increasing profit margins does not need to be a one-trick pony focused solely on producing and selling more cannabis. Giving greater attention to the other half of the equation by reducing the cost of production through greater efficiency, reduced resource inputs, and data-driven decision-making can ultimately boost profit margins.
Further, by applying scientifically proven growing practices, growers may simultaneously reduce operating costs while increasing saleable product.
So, what if the “race to the bottom” wasn’t about increasing supply in response to declining sales prices? What if, instead, the race to the bottom focused on the denominator—the bottom value—of the efficiency equation? By reducing resource inputs and using them more effectively, cultivators can increase efficiency, reduce costs and increase sales. After all, isn’t that the holy grail all business operators are looking for?