
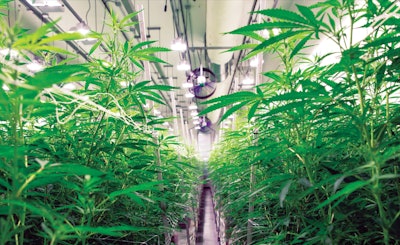
As the cannabis industry grows into new markets, the common misconception that starting a business in this industry will lead to quick-and-easy profits could not be further from the truth. In order to remain successful with increased competition and tightened margins, cannabis cultivators must take a “lean” approach to operations by limiting waste, managing costs and increasing efficiencies.
Here are three tips for cannabis cultivators looking to implement lean principles and practices in their grow facilities.
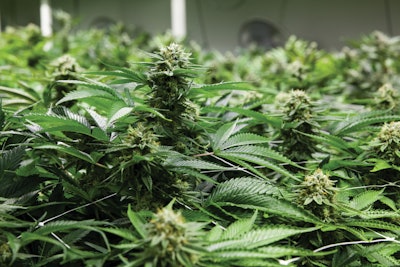
1. Use a buffer plant strategy.
Cultivators can create a buffer in their grow by cloning extra plants at the beginning of each crop cycle. Maintaining a buffer allows cannabis growers to absorb losses throughout each phase of plant growth while still being able to achieve the desired planting density when transitioning batches of cannabis plants into flower rooms. However, the buffer ratio should never be too large—or too small—for any operation. Therefore, Identifying the buffer “sweet spot” is essential.
For example, if a cultivator intends to grow 1,000 plants per cycle and is operating with a 5% buffer, it will be necessary to clone 50 additional buffer plants (5% of 1,000). Buffer plants are not treated any differently than normal production plants. They are not labeled or kept in a special area—they are simply safeguards for the batch in case of losses during the clone and vegetative stages of growth.
Having too large of a buffer can lead to using more nutrients, light, power and labor, which is wasteful and reduces cost efficiency. However, having too small of a buffer can lead to missed production and financial goals.
Finding the sweet spot for a buffer begins with having the right number of healthy mother plants to produce the number of clones needed for each production batch. A fully optimized grow should be able to operate within a 3% to 5% buffer for each phase of growth.
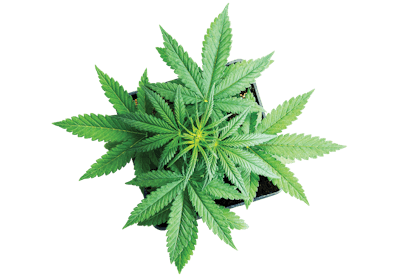
2. Automate cultivation processes to cut back on time and labor costs.
One of the most time-consuming steps for many operators is transplanting. Cleaning and filling pots with planting media can take hours of labor, depending on the equipment available, the size of the team and the scale of an operation. For a well-trained team of four to five growers, transplanting 1,000 clones into 1-gallon pots can take a full eight-hour workday. Transplanting plants from a 1-gallon pot into 3- to 5-gallon pots can take twice as long and requires additional resources (such as larger pots, more grow media, aeration and storage area for resources).
For coco coir and soil growers, there are a few options that can help automate—at least to an extent—the transplanting process. For example, soil growers can utilize pot-filling machines that are capable of filling more than 1,000 pots an hour, while coco growers can invest in compressed biodegradable pots that can be expanded with a slow drip from an irrigation system, eliminating the need to clean and fill pots.
Having too large of a buffer can lead to using more nutrients, light, power and labor, which is wasteful and reduces cost efficiency. However, having too small of a buffer can lead to missed production and financial goals.
Automating processes is also critical during growth stages. For example, utilizing automatic fertigation equipment will dramatically cut the time and labor of hand watering while simplifying plant feeds, enabling multiple recipes and feeding schedules, and helping optimize quality and yields.
Post-harvest processes can also be automated. Trimming hundreds of pounds of material can take weeks for teams that are not properly equipped. Fortunately, many forms of automated trimming equipment exist that allow for very high throughput while maintaining the quality of finished flower.
3. Reduce supply chain inefficiencies by purchasing supplies from the same vendor.
Using one source for all or most of a cultivation facility’s needs will streamline the ordering process and improve communication when compared to piecing together supplies from multiple vendors. Most importantly, a single-source strategy encourages a stronger partnership with your vendor, which leads to greater collaboration and improved quality of product. Close partnerships also equate to fewer opportunities for error, which can reduce or eliminate logistical delays created by the lack of necessary materials required to sustain production.