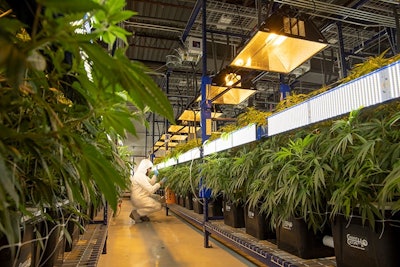
Precise climate control is essential for cannabis cultivators to produce consistent crops, especially in indoor environments, but the equipment needed to achieve this level of control is only as effective as how well the equipment and the growing space itself are designed, according to experts with Surna. Surna provides MEP engineering and equipment for energy and water efficient solutions that allow growers to meet the unique demands of a cannabis cultivation facility.
In many operations, cultivators work with clones, and although all the plants are genetically the same in this case, external stressors such as temperature, humidity and CO2 levels largely determine the end product’s cannabinoid content, terpene profile, yield and overall health, according to Troy Rippe, senior technical adviser and director of research and development with Surna. The HVAC system controls many of those stressors, he adds, particularly temperature and humidity, meaning that cultivators can have a lot of influence over the end product, as long as they use the right equipment for their facility.
Greenhouses typically use an evaporative cooling method called a wet wall, Rippe says, which adds humidity into the space and therefore cools the environment. Greenhouse facilities are subject to the region’s climate, however, and an area’s temperature and humidity can impact the end product’s consistency.
“Even if you have the same genetics or the same plants grown in the same greenhouse, that’s a different end product in California than it is in Arizona than it is in Massachusetts,” Rippe says. “You’re still at the whims of nature. Although you can control it a lot more in a greenhouse than in a field with ridge vents and ventilation and heating and cooling systems, it’s still a pad wall, and you’re at the mercy of the temperature and humidity outside.”
In an indoor environment, cultivators can use HVAC systems to create environmental stressors at precise levels by controlling the temperature, humidity, CO2 levels and airflow. However, growers need to know how to pick the right equipment for their facility.
“There’s still a learning curve in the industry on the best approaches and the best equipment and the best systems to put together in order to achieve those very precise environmental controls,” Surna Engineering Manager Kenneth Loshelder says.
Designing the Right HVAC System for Your Facility
The HVAC system is key for precisely controlling the environment in indoor facilities, Rippe says, and set points for temperature and humidity may change during the plants’ growth stages, depending on the plants’ size and lifecycle. Growers may also have different set points for temperature and humidity based on whether the lights in the facility are on or off, Rippe adds.
HVAC systems are expensive to buy and expensive to run, and these expenses should be considered when choosing both equipment and set points, Rippe says.
“Growers don’t always necessarily realize, as you shift your temperature and humidity set point down, it can have huge impacts on your capital requirements in terms of how big that equipment has to be in the facility and your energy requirements in order to do dehumidification,” he says. “When we started, a common set point was 78 degrees, 55 percent relative humidity, and now we’re starting to see temperature more and more in the lower 70s and a lower humidity range, like 50s and 45, because it drives certain properties in the plants.”
Rippe and Loshelder work closely with cultivators on their temperature and humidity requirements, working to determine the right mechanical system for a grower’s unique facility and cultivation methods.
Many cultivators want very low temperature and humidity set points at certain phases of cultivation, but they do not have the mechanical experience required to understand that oversized equipment is often necessary to meet these demands, Rippe says.
“When you want to grow at 60 degrees and 40 percent relative humidity in your last week, that’s a pretty extreme ask and that might be an additional $40,000 of equipment to make that happen,” he says.
By working with an engineer who does have this mechanical background and experience, cultivators can better design their facilities and climate control equipment to reach their goals and align with their budgets.
“They’re going to give you a design that hits the vapor pressure deficit (VPD) on the chart exactly when you want to hit it,” Rippe says.
And it’s important that the engineer has experience in the cannabis industry specifically, Loshelder adds. “You want to find somebody who understands the unique requirements of growing a plant, and that the conditions are not designed for people,” Loshelder says. “One engineer you might talk with could be doing a lot of commercial-type facilities, working on office buildings or banks, and then you’re just going to plop a job with completely different operating requirements on them. If they don’t have the experience to weigh these different factors, it’s more likely that they might miss something in the design that ends up costing a lot of operational trouble in the future, or a lot of cost to remedy the design to get it to work right.”
Rippe and Loshelder have worked with cultivators who have had to spend millions of dollars fixing mistakes engineers made because they had never designed a cannabis facility before, and they undersized the climate control equipment needed for cannabis cultivation.
Designing Systems for the Long-Term
In addition to working with a cannabis-specific engineer in the design of their systems, evaluating costs from a long-term perspective is essential, Rippe adds.
“If you’re just using the cheapest system you can get away with, swings in temperature and humidity and mold problems can cause you issues because plants can’t pass testing and you’re not getting the yield,” he says. “Those systems are going to hurt you long-term. If you don’t spend more up front, you’re going to spend more over the life of your building.”
Cultivators should avoid light commercial equipment that is designed for comfort cooling only and not for the rigors of round-the-clock needs of cannabis cultivation, Loshelder adds. “All the equipment runs 24/7 and it’s a constant load on the HVAC equipment. The HVAC equipment needs to be industrial-grade to handle high-duty cycles without failing prematurely.”
Rebates are available for HVAC systems, Rippe says, which can help cultivators save money when designing more effective and efficient systems.
“That becomes a win-win,” he says. “It’s more energy efficient, you get money back from the utility and rebate companies, and you actually get a system that achieves the desired functional performance from an engineer that’s used to doing that and can show you the results.”
Cultivators should also have some flexibility built into their systems, Rippe adds. “You might want to consider designing a system that can actually vary. As your building changes or you get a different cultivator that wants a different temperature and humidity, you want some flexibility. And those systems are out there."