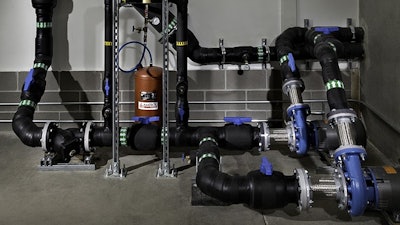
Cannabis cultivators have many factors to consider when implementing HVAC systems for their facilities, including facility type and design, production schedules, and overall cultivation methods and goals.
Here, Graeme Kirkness, EIT with engineering consulting firm Enertec Engineering, and Mark Dieser, president of engineering firm D2E Solutions, offer advice for selecting the right equipment.
Tips from Graeme Kirkness, EIT, Enertec Engineering
1. Design with your facility type in mind.
Indoors, challenges arise when cultivators try to make too many sudden changes in the buildout of their facilities. “Your timelines don’t match up with what the lead time of equipment may be, and you may be all of a sudden trying to design a space with the equipment that you have on site or that is ordered that isn’t necessarily the best solution for what the new space is,” Kirkness says.
In order to implement HVAC systems that are the best solution for their space, Kirkness says to evaluate vapor pressure deficit (VPD), or the plant’s ability to release the water that it has used to get nutrients from the soil. Variables such as temperature, humidity and lighting all directly impact VPD, and HVAC design companies can control around those variables, lining them up within the range needed for optimal plant growth.
“To maximize the efficiency of your system, you then look at how your facility as a whole operates,” Kirkness says. “A plant grows in a natural environment with sunset and sunrise, so it’s slowly introduced to light and slowly decreased from light. You can simulate that with your lighting, and that lets you slowly ramp up or ramp down your equipment’s capacity to match that. Instead of having your equipment running full-tilt the whole time, you can tailor it to your growing situations.”
2. Set production schedules that allow for smaller, more efficient equipment.
Larger indoor facilities will likely have several rooms operating simultaneously, which equates to more energy to keep all the spaces in the facility cool, Kirkness says. “If you can schedule your facility in such a way that you only have half or a third running at a time, depending on what your lighting requirements are, you can then have a single, smaller piece of equipment that’s able to operate the whole time and operate more efficiently while maintaining your production schedules.”
Changing the number of plants in a room can also greatly change the equipment’s ability to cool or dehumidify the space, Kirkness adds. “By putting more plants into a room, you add a larger latent (dehumidification) load as they release the water off their leaves, and if the facility’s already been designed around a smaller load of plants, by adding more plants into your room, it’s potentially reached the point where the equipment that’s been designed and the systems that have been designed don’t have enough latent capacity to pull all the moisture out of the air. So, now you’re stuck trying to retrofit pieces of specific dehumidification equipment, for example, to make up that deficit that’s been introduced by adding more plants.”
In addition, as companies consolidate, new ownership might mean that a cultivation facility must adopt new production schedules and growing methods, which might require new equipment, Kirkness says. “You are left with equipment or a design that doesn’t line up with a new space. Your mechanical room may have been moved, and now the fans in your HVAC equipment might be too small, and now you need to order a larger fan, which means larger equipment and having to reorder large pieces of your facility.”
To solve these challenges, Kirkness suggests working with an engineer who understands cannabis cultivation and how to properly heat and cool the facility with the business’s goals in mind. “With an engineer or an engineering firm, you’re getting someone who’s familiar with the different types of equipment and what each type of equipment is best suited toward and how they can fit all those complicated puzzle pieces together into a system that best meets your needs, both immediately and for potential expansion.”
3. Work with a company that has cannabis experience.
HVAC companies and engineers working on cannabis facilities should have past experience with the industry, Kirkness says.
“Climate control is an area that directly impacts your bottom line and your profit margins, and it’s not something that you want to be fiddling around with,” he says. “It’s something that you want to be able to turn on and it works, and it provides you with the history, the real-time data and, ultimately, the growing conditions that you want to be able to make the product that you are striving for within the really stringent tolerances that are allowed.”
Tips from Mark Dieser, President, D2E Solutions
4. Choose equipment that supports your facility design and cultivation goals.
Finding the right climate control equipment for an indoor grow depends on a facility’s space requirements, as well as what the cultivator wants to achieve in their grow rooms, according to Dieser.
“The conditions growers want to achieve—that being temperature and relative humidity—can and does dictate the type of equipment and/or the size of the mechanical systems,” he says. “The size of the rooms is also another big item.”
Grow rooms are more intense environments than standard buildings, and they require more effort to remove moisture and heat, Dieser adds. Depending on the lighting and whether the space has one or multiple tiers of plants, there is a significant amount of energy per square foot of usage, which is a unique situation for HVAC systems, he says.
“It’s out of the norm for a lot of systems,” Dieser says. “You typically don’t see this kind of energy density, and design of the system as it relates to multiple things, such as the room temperature, relative humidity and the discharge temperature, or the air cooling the room, which all plays into what type of equipment you will need for the grow rooms.”
5. Plan the facility design before it’s built out.
In addition to working with engineers who are experienced with cannabis cultivation facilities, cultivators should also carefully plan out the facility design before the build-out phase, Dieser says. In order to do this, growers need to decide how they want to lay out their rooms, as well as standard operating procedures and how they would like the business to operate internally, he says.
“Some grow rooms have spacious and easy-to-access tables and plants, and others, they pack them very densely, which can change your design requirements and how you’re attempting to achieve the cooling and dehumidification of the space,” Dieser says.
By planning the facility design in advance, cultivators and engineers can more clearly see the bigger picture and determine what kind of climate control equipment is needed to best serve the space.
“I often see project teams put the cart before the horse—they look to get things up and running as fast as possible, and perhaps they go so fast that they may not have given everything the adequate thought,” Dieser says. “There are quite often a lot of changes, and the cultivators know what they want to do in their space, but I think the design of the HVAC system is something that does take a little bit of time to make sure that everybody understands what they’re trying to achieve. Going quickly is good, but sometimes I think it causes rework or issues where they’ve got to change things, so planning before they start building something—whatever little bit that may be—is well worth it."