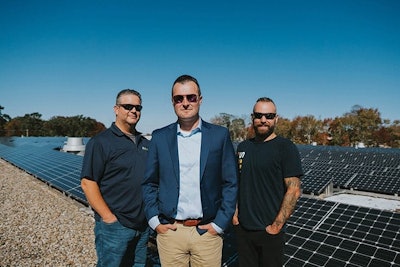
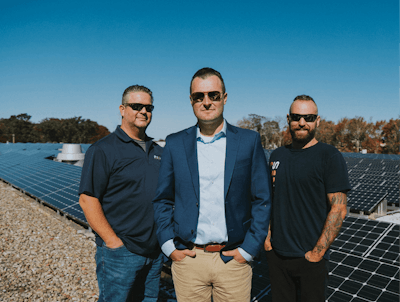
Solar Therapeutics is part cultivation company, part power plant, and the company is looking to replicate its model in different markets.
As an engineer with Woods Hole Oceanographic Institution and Deep Submergence Laboratory, Ed Dow explored the depths of the sea, tagging whales for tracking and designing submersibles for deep ocean floor exploration. Now, as CEO of Solar Therapeutics, a vertically integrated medical and adult-use cannabis operation in Massachusetts that offers a roster of THC- and CBD-rich varieties, he has turned his gaze up, toward the sun.
Solar Therapeutics, which launched in 2019, is not a sun-grown cannabis company, as the name might suggest. Rather, the name is derived from the plethora of solar panels that the company leverages—70,000 square feet on the building’s roof and acres more in an adjacent solar field.
Dow felt that indoor-grown cannabis was the best option for his company given Massachusetts’ brutal winters, but he also realized that indoor cultivation is not the most resource efficient. He wanted to leverage his engineering background to develop a facility that would decrease operational costs and carbon emissions while maximizing quality and yield. Finding a property that came equipped with a solar panel array, well, that “was absolutely a happy accident,” Dow tells Cannabis Business Times.
“That was of tremendous value to me,” he continues. “It might've taken a few more months to get our property together because we had to change the zoning, but it was well worth it in my opinion. And I think it's paying dividends now.”
Finding Solar
When Dow decided to make the jump into the cannabis industry, he quickly realized the assets he had accumulated in his last company, an industrial metal finishing facility that was a spin-off from his work with the Deep Submergence Lab, were not going to cut it. (Massachusetts requires applicants have at least $500,000 in cash-on-hand prior to applying for a license.) But he knew that his engineering background with the lab, as well as his experience working with automated systems in the metal finishing industry, were valuable skills that he could bring to developing systems relevant to cannabis cultivation, so he contacted friends and family and put together a group of seven founding investors, consisting mostly of doctors, to support his application bid.
Finding investors in the early days of Massachusetts’ medical program was an interesting challenge because prospective licensees also had to register as non-profits, Dow explains. He founded Dow Capital Partners as a funding vehicle and set up “these really complicated service agreements between Dow Capital and our marijuana company,” he says. “Thankfully, Massachusetts realized that [was] very cumbersome … and they allowed us to swap over to for-profit maybe two years ago. As soon as we had that opportunity, we did that. We got rid of our service agreement between the non-profit and now we maintain it as a for-profit company.”
The importance of those first investors went beyond their financial support. Without them, Solar Therapeutics would not have found its home in Somerset.
Hunting for properties in registered marijuana district (RMD) zones—areas that met state requirements for a cannabis business—was like trying to “find a needle in a haystack,” Dow says. He found the current location after one of the founding partners with an ownership stake in the property approached him with the idea of using the site. After some research, Dow learned that it was one of three structures that qualified as RMD zones in Somerset. The fact that the property came equipped with solar panels was the cherry on top of the sundae. “We changed our name to Solar Therapeutics for that reason,” Dow adds.
Yet one challenge remained: the property was zoned for commercial, not industrial, use. (The previous property owners converted the originally industrial lot to commercial use when industry took a dive in the 1990s in order to save part of their investment). Dow says it took only two special town meetings to change the appropriate bylaws and zoning regulations. “The property was only 20% occupied with five tenants. So, I offered to take the entire place, convert the whole thing for a considerable amount of money. ... And they … supported the idea,” Dow details.
Another requirement in Massachusetts’ program is the required Host Community Agreement (HCA)—a contract that applicants must have in place with the municipality to show local support of the project. Dow says negotiations were pretty straightforward three years ago: a business would present to the city council its plan, revenue projections, team members and proposed location. The city council, in turn, would assent to the project if it felt it was strong enough.
State regulations surrounding HCAs also allowed municipalities to charge up to a 3% annual tax for up to five years, which “I didn’t even bother trying to negotiate,” Dow says. “It just seemed like if you wanted to be serious, you just offered that, it’s what the town’s going to want.” He advises new applicants to follow that example. “Don’t try to negotiate down the fee. That’d be nuts … but also be wary of offering over and above the fee because that’s not necessarily legal.” He cites the 2019 arrest of the mayor of Fall River, Mass., who created a scandal by allegedly pocketing hundreds of thousands of dollars in bribes from cannabis businesses wanting to set up shop in the town as a lesson from which to learn.
When negotiating HCAs, “just give to the top end of the spectrum of what [is] legally allowed, and that’s kind of the only way Massachusetts wants to deal with you,” he advises.
_fmt.png?auto=format%2Ccompress&fit=max&q=70&w=400)
A Power Plant to Power Plants
Dow describes the Somerset facility as a “perfect blank slate.”
“This building was meant to be an industrial building. If you see it in person, you’ll say that that should never have been commercial. ... We look like a big Home Depot,” the CEO says with a chuckle. After demolishing dividing walls that had been set up for the commercial tenants, the structure became “the perfect canvas for us to build an entire new building within that space.”
The next step was rebuilding the rooms to create veg and flowering spaces. This was done using a PermaTherm wall system—insulated panels that are thermally efficient. A new HVAC system designed specifically for cultivating cannabis was installed and sized for the facility’s licensed canopy of 100,000 square feet, even though the company is only cultivating about half that space as it slowly ramps up output to keep up with demand.
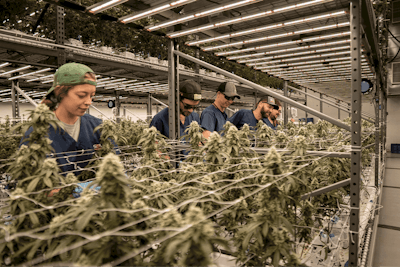
Sizing the HVAC was pretty straightforward compared to getting the power the facility needs to be able to operate at full capacity. Despite the acres of solar panels, “that’s not necessarily what you can rely on to feed your facility needs,” Dow explains. The sun isn’t always shining in Massachusetts, and battery storage is still a big hurdle for the solar energy industry. “Tesla hasn’t figured it out with battery storage yet on the solar side,” he says. “Once they figure it out, then maybe we can rely on a purely solar panel operation. But you still need either grid power, or you need to come up with a way to make your own power.”
Instead of using solar power directly, Solar Therapeutics sells the electricity back into the local power grid, with the proceeds offsetting other operational costs. Despite the solar assets offsetting its energy use, grid power was not an option for Solar Therapeutics, as the power plant supplying energy to the site would not increase its output to the facility. Faced with the untimely doom of his company just six months into construction (and millions invested), Dow decided to become his own power supplier and built a microgrid, which leverages both solar energy and a combined heat and power (CHP) system.
Solar Therapeutics’ CHP system burns natural gas and captures heat to circulate into the HVAC system. Dow worked for nearly two years with a company that supplies CHP systems to oil rigs and gold mines in order to get the plan and unit set up. CHP systems “make about half the carbon emissions that a typical power plant would,” Dow says, “but then if you do interesting things like recycle the heat … which we do … then you can do further energy reductions.”
The CHP unit allows the company to operate with emission rates 60% lower than a normal power plant, “but we’re targeting 90%-plus,” he continues. “And when solar battery storage develops further, we’re hoping to rely even more on our solar and further reduce our carbon footprint.”

Other Resource-Saving Features
Water reclamation was another resource efficiency aspect that was planned from the onset. Solar Therapeutics reclaims and recycles all the water captured by the facility’s air handlers. “We recondense it, pump it back to the fertigation room, clean it up and put it right back into our water supply,” Dow says.
Using LED lights throughout the facility allows the company to reduce the heat load to operate its HVAC system with greater efficiency, Dow says. Automating watering and fertigation, as well as environmental controls and lighting, also has allowed the company to collect data to develop benchmarks and identify further efficiencies as they complete more harvests.
Solar Therapeutics also uses a centralized heating and cooling technology where hot or cold water is sent through a closed-loop system to heat or cool individual grow rooms and/or pieces of equipment. The system can create “free” cooling by pulling cold, outside air into the free fluid coolers, allowing the company to avoid turning on the expensive-to-run chilling system. “It’s a much more expensive way to build upfront, but it’s a way more [energy-efficient] way to build if you have these big operations,” Dow explains. “When the free fluid coolers are running, all we have to power on are the fans.”
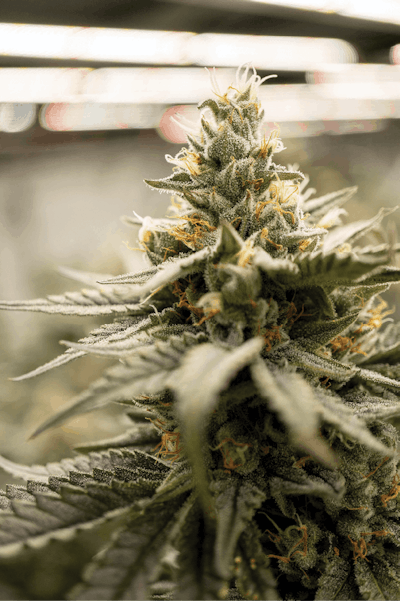
These early investments in high-efficiency and automated systems have allowed Solar Therapeutics to greatly reduce what are typically the two biggest cost drivers for cultivation businesses: energy and labor, respectively. According to Robert Keller, the company’s CFO, labor now outpaces energy as the company’s biggest operational expense. “Because of our energy efficiencies, our energy costs right now are about 30 percent of our labor costs,” he says. “When we’re done installing all of these components, our energy costs will actually go down another 30, 35 percent.”
Between the solar panels and the CHP system, Solar Therapeutics’ microgrid generates five megawatts of power (enough to power roughly 5,000 small homes). “Our location is able to produce approximately 700kW in solar,” Dow explains, “which due to current contracts and SRECs [solar renewable energy certificates], must be net-metered back to the grid. Solar ultimately intends to take this power ‘behind the meter’ in the future, and has already built in the electrical infrastructure required to accommodate the existing solar power, as well as additional solar assets.”
Additionally, Keller says the company has received almost $1 million in rebate incentives thanks to Solar Therapeutics’ LEDs, HVAC system and chillers.
Keller has found the utility companies to be very helpful and willing to work with cannabis companies—ultimately, it is in the utility company’s interest to reduce the amount of energy any facility pulls from the grid. He advises growers looking at energy incentives and rebates to open a direct line of communication with their respective utility companies and have them help growers walk through the application if they are unfamiliar with the process.
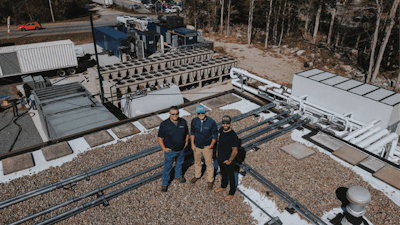
High-Efficiency Cultivation
The emphasis on sustainability in an indoor facility at the scale Solar Therapeutics is what attracted Brendan Delaney, the company’s director of cultivation, when he first visited the site during his job interview with Dow. After honing his craft in California’s Emerald Triangle, working at outdoor farms and greenhouse operations, “taking on a large indoor project like this was definitely something that intrigued me,” Delaney says.
Each flowering room at Solar Therapeutics is equipped with 200 LED lights spaced on a three-tier vertical rack system. Having a microgrid on-site also allows the company to run the lights at whatever intensity the cultivars prefer without having to worry about peak rates. “Not worrying about peak times from energy companies is great [because] we can really run the lights during the day if we want, and people can work under them during a normal 9-to-5 schedule,” Delaney says.
One big adjustment for Delaney was learning to grow in rockwool cubes, as he had obtained a certification in permaculture design in California to grow in organic living soils. “Making the transition into six-by-six [inch rockwool] cubes and using a really state-of-the-art fertigation system was a big change. There’s a lot less room for error with something like this,” he says. When using organic cultivation, the soil acts as a buffer that protects the plants from your mistakes. “If you make a big mistake here, you can potentially kill 2,000-plus plants in a room,” he continues. Automation technologies and a collaborative team of technicians helps reduce the chance of catastrophic failure in any one room, he adds.
The rockwool cubes are decked out with two drip emitters for fertigation, and every plant is fed a smaller amount of nutrients six to eight times per day with a custom-blended nutrient mix that fits the company’s growing style, Delaney describes.
These short fertigation blasts last between six minutes per round and allow the plants to get a smaller amount of water on a regular basis. This system helps “prevent waste, for one, and keeps the plant in a state where it’s constantly drinking and eating,” Delaney says. “This is just a constant state of uptake. … Our flower cycles actually have been a little bit shorter than I expected. Eventually, we’ll maybe be able to add a whole run [per] year by cutting down our veg time and our flower times a little bit.”
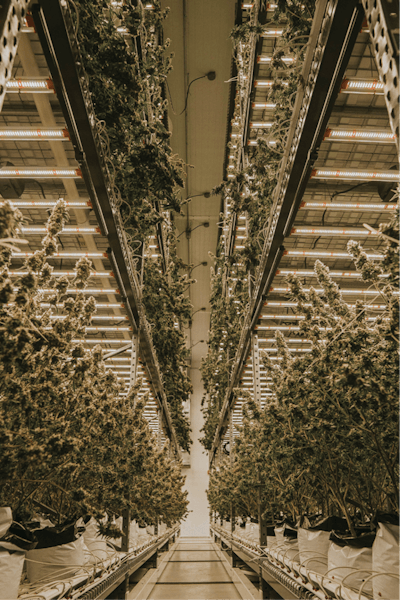
Keeping the plants stress free and maintaining a tightly controlled environment has allowed Delaney to avoid any pest and mold issues in the facility (so far), as well. In addition to tight environmental control, he uses a preventative citric acid spray during the vegetation cycle and beneficial predatory mites later on in flowering.
An automated CO2 enrichment system allows Delaney to set target parts per million (PPM) levels based on each cultivar’s needs in every room. “We have a liquid CO2 tank, which stocks 16 tons of liquid CO2,” he details. “We have sensors throughout the room that take a reading and then if we need to add more, it adds more. … [The plants] only really use CO2 when the lights are on, so we really bumped that number up as high as we can without going too far.”
While the company currently uses a separate liquid CO2 tank to supplement the grow rooms, Solar Therapeutics intends to tap into the CO2 emitted from the CHP system to further increase its efficiencies. “It’s definitely in the plans, but we haven’t implemented it yet,” Delaney says.
In addition to tracking and sending out a signal to inject CO2 into grow rooms, the environmental sensors also collect different environmental and fertigation-related data points for Delaney to analyze and track. Not enough data has been collected to notice any trends yet—the company only has been growing plants in the facility since February 2020—but Delaney is looking forward to finding any strain-specific needs that he can program into the centralized management system.
Solar Therapeutics’ genetic selection comes from Delaney himself: He brought seeds of approximately 30 strains with him from California, some of which he’s worked with for years and others that are unique to the Massachusetts company, he explains. Solar Therapeutics offers THC-rich varieties such as Pink Champagne, Gelato and All Gas OG, as well as high-CBD strains like Critical Mass and Harlequin. Delaney also is working on crossing those THC and CBD varieties to create more balanced cannabinoid ratios, which continues to be an ongoing project. Beyond cannabinoid content, Delaney is trying to bring to market varieties with terpene profiles unique to the East Coast. He’s working with a handful of West Coast breeders to bring exclusive cultivars to his market. “Exclusivity is huge in this state,” he says.
Delaney avoids varieties with inconsistent watering or fertigation needs, as well as cultivars with susceptibility to molds and pests. “On this scale, it’s really hard to focus on one group of plants,” he explains. “You have to come up with a feeding schedule that works for all of [the plants in one room].” Crossing the right varieties can help create more standardized and robust plants, but that takes time. Instead, Delaney focuses breeding efforts on trying to reduce flowering time to maximize the number of harvests the company can have in a year. “Sour Diesel or Chem strains typically [flower for] 10 weeks. If we can get them down to eight weeks and still keep all the good qualities, that’s what we’re looking to do here,” he says.
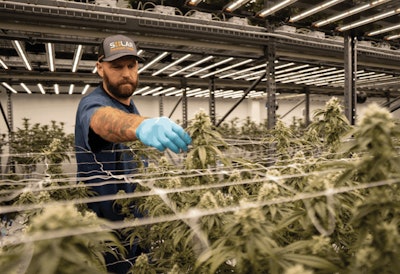
Taking Solar Out of Massachusetts
While not every facility will be equipped with a solar panel array, Dow believes the model he’s developed in Somerset, Mass., can be exported and replicated in other states, especially as solar technology continues to evolve. As he’s gotten familiar with some of the larger players in the solar panel arena, he’s come to the conclusion, he says, that, “I have the ability to bring solar panels to whatever location we go to,” he says. “So that means I don’t need to pick the perfect building, perfect location. I can always add those solar assets. More importantly, I can add the CHP.
“The microgrid combines a lot of different power generation assets and blends them together. That’s where the optimum efficiencies happen,” Dow explains. The COVID-19 pandemic definitely slowed down those expansion plans, but the CEO says he’s seeing the market spool up again.
Whether he launches a new facility on his own or partners with an existing or new licensee in a different state will depend on the circumstances that present themselves. But he warns that the microgrid model brings “a whole additional layer of headaches on top of an operation. … It’s not that you hire a contractor and they build you a microgrid. … If that were true, everyone would do it.”
Keller, the CFO, is looking forward to increasing efficiencies within the Somerset facility to drive down operational costs, while continuing to develop the company’s dispensary businesses. In addition to the Somerset location that is attached to the cultivation site, Solar Therapeutics plans to open at least two more retail locations in Massachusetts. Those retail locations are going to be important revenue generators as the company continues to operate at a loss while it builds out and refines its cultivation processes, he says. That said, “I see Solar probably in two to four states in the next three to five years—that’s my goal,” Keller says.
“We’re working on it now, but it’s a balanced process. You don’t want to grow too fast, too strong, just because you don't want to get your head over your skis,” he adds.
Delaney’s goals for Solar Therapeutics’ future are right out of the cultivator’s guidebook: “My personal goals are definitely to produce the highest quality flower in the most efficient way on the East Coast.” He believes that the systems that the company has adopted and created, combined with the team it has in place, means Solar Therapeutics’ potential is boundless. Or, as he puts it, “The sky’s the limit with this company.”