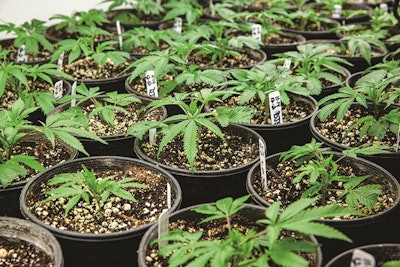
Each year, new products and technologies come to market that can help commercial cannabis growers speed plant growth, improve yields and decrease production costs. Immediate changes to the grow environment, however, can place a crop at risk, and improperly introducing new products into your cultivation program can result in missed deadlines, damaged plants and even crop failure.
Improperly introducing new products into your cultivation program can result in missed deadlines, damaged plants and even crop failure.
New cultivation materials should be cautiously introduced into the grow environment, and preferably trialed on a small scale first. Not only does this make good grow sense, but it is a fundamental tenet of Good Manufacturing Practices (GMPs). GMP-compliant growers follow very strict guidelines when it comes to changing cultivation practices or introducing new materials into production.
The following guidelines can help ensure that your next cultivation purchase is a blessing to your operation, not a curse.
Fertilizer
Growers frequently experience plant issues as the result of introducing new fertilizers into their cultivation program. Most operations use fertilizer with each irrigation, and it’s applied to thousands of plants at once. If a new fertilizer is mixed incorrectly, or reacts poorly with the grower’s substrate, plant problems can manifest themselves in the form of burned leaves, discolored pistils or dead roots.
For hydroponic growers, switching out premixed hydro-shop nutrients for a different brand can be risky. Mineral ratios will differ between brands, and some plant additives are not required to be listed on the product label. For organic growers, new liquid fertilizers or compost teas can be risky as well because it can be difficult to guarantee the consistency of ingredients in these mixes. Compost teas that aren’t properly brewed can negatively affect plant health, and even properly prepared liquid organic fertilizers have a short shelf life.
The correct way to introduce a change to your fertilizer regime is by first trialing the new product on a small portion of your crop. For new hydroponic formulas, make sure to follow the label and test the final solution with an electrical conductivity (EC) pen. For new organic fertilizers, be aware of the product’s expiration date and discard the product if not used before then. In both cases, if the fertilizer is purchased in large volumes, it is a good idea to perform a solution analysis on each lot prior to use.
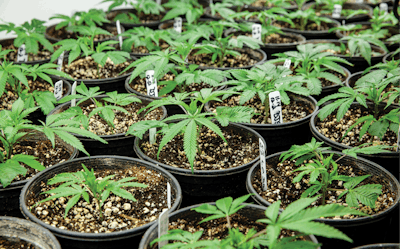
Growing Media
Cultivators may want to change their growing media to decrease production costs, but a dramatic change in substrate composition can catch cultivation teams off guard. For example, when plants have fertility issues due to a growing media switch, growers must rethink their fertility and watering programs. The setback can cause slow plant growth and missed production deadlines.
When using coconut products (coir, fiber, etc.) the potassium, sodium and chloride content can vary drastically between brands. Some manufacturers/suppliers triple-wash and pH-buffer their products to remove salts and provide for better nutrient uptake, yet others skip this step, and growers must adjust their plant nutrition protocol to account for the higher salt content.
When plants have fertility issues due to a growing media switch, growers must rethink their fertility and watering programs.
Most organic growing media components are not composted, but if a composted material is being used, it needs to be properly “cooked” during the compost stage, meaning the microorganisms in the compost must be given time to break down the raw material (in a process that naturally creates heat as a byproduct); uncooked or poorly prepared compost can burn plant roots and shoots. Different raw materials affect nutrient availability in an organic mix, so growers will need to adjust their watering and fertility programs to find a proper balance.
A media analysis can help provide information like high salt content or unfavorable pH values at the outset, and the risks inherent to introducing new growing media can be mitigated by selecting a reputable supplier to work with that can formulate the proper media mix for your operation. Proper media formulations will guarantee optimal/desired physical properties (porosity, air, water, etc.) essential for crop management.
If feasible, it is also helpful to perform a small trial of one complete crop cycle prior to switching over the entire operation.
Lights
The temptation to upgrade to new lights is very compelling, and with good reason. Today’s horticultural grow lights provide more power, use less electricity, and some even enable growers to customize light spectrums to encourage cannabinoid production. However, if you don’t slowly introduce your plants to a new light source, you’re likely to encounter problems.
Whether you’re going from 600-watt high-pressure sodium (HPS) to 1,000-watt HPS), or HPS to light-emitting diode (LED), you need to trial these products before implementing them on a large scale. For indoor growers, moving from a lower-wattage HPS to a higher-wattage HPS could overwhelm the HVAC system and cause heat burn to the plants. On the flip side, some growers are so delighted with the low heat output of LEDs that they place the plants too close, and as a result experience crop bleaching—the plants could literally grow white buds.
If you are thinking of upgrading to stronger lights, make sure your HVAC system can handle the increase.
Even if the supplier swears you won’t have any problem incorporating its new lights into your grow, or you know of industry colleagues that have seamlessly made the transition, it is still your responsibility as the grower to minimize potential damage to the crop by testing these lights first. If you are thinking of upgrading to stronger lights, make sure your HVAC system can handle the increase. If possible, establish plants at a greater distance from the light than is recommended by the manufacturer, and slowly bring the lights closer over the next five to seven days. If light height is fixed, try dialing back light intensity, or use fewer lamps initially and slowly build up to full strength. If no negative effects are evident after one week, it should be safe to introduce the lights to the entire crop. Still, play it safe and slowly introduce your entire crop to your new light setup.
Advanced Hydroponics
Aeroponics and deep water culture (DWC) are advanced forms of hydroponics that use no substrate at all. Plant roots are either suspended in air and misted with nutrient solution, or they are bathed in constantly flowing oxygenated water. Switching to these cultivation methods can appeal to growers because the systems use less water, grow plants more quickly and avoid the risk of soil-borne diseases.
Although the advantages may be obvious, moving from substrate growing to aeroponics or DWC is a huge jump. These systems demand tight control over water temperature and dissolved oxygen levels, and there are a near infinite number of spray nozzles and tube junctions that could clog, leak or rupture. Equipment and systems need to run in perfect unison, and they can be especially risky for start-ups because they are more prone to unexpected interruptions in power supply.
The best growers establish their toolkits of new pest control products before they need to use them.
Growers interested in evolving their programs in this direction should consider setting up a research and development (R&D) station to trial these systems first. Get used to the increased vigilance of new equipment and all the intricacies of running these ultra-high-tech hydroponic systems. After a few mini-crop cycles, the grower can decide if this upgrade makes sense to incorporate over several thousand square feet of cultivation. (Editor’s note: For more information on these hydroponic systems, see the article “Are You Well Versed in Hydroponics? Part II” in the March 2019 issue of CBT.)
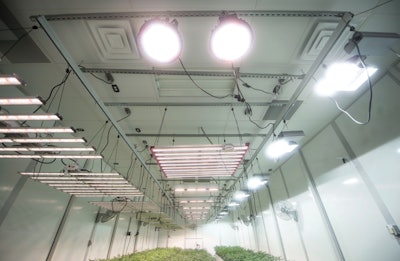
Pest Control Products
A common misconception is that organic pesticides and fungicides are not as effective as their chemical counterparts, and as such, the introduction of new organic products are safe in any amount. Unfortunately, many growers find out the hard way that this is simply not true. I have repeatedly witnessed plant damage that was the result of using all-natural pest remedies, such as neem oil. Although 100-percent organic, if neem oil is applied at a high rate, or to dry plants, or in the heat of the mid-day sun, plants are likely to suffer.
The best growers establish their toolkits of new pest control products before they need to use them. This is because most spray applications are done urgently, when pest or disease pressure is severe, and the grower doesn’t have time to perform plant compatibility tests. The only thing worse than having a severe insect outbreak on your crop is to further aggravate plant problems with the use of a non-compatible pesticide.
Trials only need to involve a few plants, but they should be representative of the entire crop. Plants should be in good health and recently irrigated, and the spray application should occur in the early morning or late afternoon in a greenhouse, or under reduced light if indoors. Application rates are stated in ranges on the product label, so start at the low end of that range. If after 72 hours no phytotoxicity is evident, the product should be safe to apply in the same manner to the rest of the crop. If phytotoxicity does occur, trial the same product again at half strength or replace it with different product and begin the trial again.