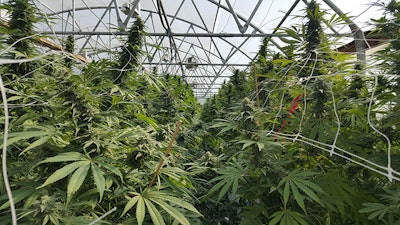
Don’t miss Nadia Sabeh’s presentation at the Cannabis 2018 Cultivation Conference! Sabeh will be joined by Strawberry Fields’ Rich Kwesell in the session “Facility Design II: Greenhouses.” Sabeh and Kwesell will discuss the most important considerations in greenhouse facility design, including lessons learned from scaling up/expanding and other insights. For more information, visit www.cannabiscultivationconference.com.
The planning and build-out of a greenhouse cultivation facility comes with a unique set of challenges—from finding the right master grower to designing the layout for highest efficiency and yield. Here, Nadia Sabeh, founder of consulting firm Dr. Greenhouse, discusses some of these factors and outlines common mistakes in greenhouse design.
Cannabis Business Times: What are some key considerations in greenhouse facility design that are most often overlooked?
Nadia Sabeh: Number one is not having a good and experienced grower during the design process as well as in the actual operation of the greenhouse. I find that a lot of people are looking for help in planning a greenhouse or designing a greenhouse, but they don’t have any grower expertise [or] someone to help guide the decisions around product flow, labor workflow [and] conditions they want to achieve inside the greenhouse, [including] operation setpoints and procedures, facility layout and workflow, equipment selections and helping investors [and] developers set realistic expectations about production rates and volume.
One of the questions that I always ask a new client, whether it’s a greenhouse or indoor grow facility is, who is your grower? Do you have a grower? And if they say they have one and this person has experience, I feel more confident about the outcomes of that project than those projects where they say, “Well, we’ll find them later. That’s going to be easy.” Or [projects where the grower] came from [a] small indoor grow. What I’ve seen is that, even if you have an experienced grower indoors, making that leap to a greenhouse is not so simple. It’s very different equipment [and] very different conditions.
CBT: What are some common mistakes you see greenhouse growers making with HVAC, and how can these mistakes be corrected?
NS: A lot of growers, in an effort to prevent mold and bacteria and other pathogens, tend to grow at a very low humidity in what I would call vapor pressure deficit. Evaporative cooling and adding moisture to the space would be helpful in a greenhouse climate, especially where it’s drier and we’re not constricted by a high-humidity climate like Florida. But a lot of growers are constrained by odor control requirements by their local jurisdictions and state requirements and regulations, so they can’t use conventional HVAC such as evaporative cooling, which would add moisture to the space.
I see a lot of facilities use air conditioning, and there’s no way they’re able to get moisture back into the space fast enough. It’s a vicious cycle in that if it gets too dry, the plants produce more moisture, use more water and produce more moisture in the air, but if [moisture] gets too low, the plants will start to shut down and use less water and produce less moisture in the air, and then it can get even drier. Adding a way to humidify the space with misters or foggers can help increase the humidity.
The other thing I see is growers who are not monitoring temperature and relative humidity frequently enough or in enough locations. They might have a greenhouse controller that is turning equipment on and off based on a temperature setpoint, maybe a humidity setpoint, but usually it’s temperature only, and they rely on that one thermostat and humidistat to control a pretty large space. It would be helpful for growers to pay attention to differences in those conditions from one end of the greenhouse to the other, [which] can be very different. Those mitigation methods such as [increasing] the humidity in the space might be different given a location. Paying attention, monitoring the room or the greenhouse at various locations over the course of the day and over the course of various seasons, [is] critical to understanding how your plants are responding to those differences in the environment.
The other thing I see is poor air distribution [where growers are] not getting good air movement [and] circulation of the air around their crops, and I’ve seen different types of horizontal airflow fans that don’t move the air very well. They don’t create a strong velocity, or they do create a high-speed, but for a very short distance, so you need more fans to make up that difference. There’s a lot of good conventional greenhouse equipment that can help with air distribution, and air distribution can also be one of those mitigation methods for a climate that isn’t perfect.
[Another mistake is using the] wrong sequence of operations for equipment. I’m of the school of thought that you use shade as a last resort for cooling because the whole reason we’re in a greenhouse is to use natural sunlight. If you shade when you don’t have to, you’re eliminating a lot of the energy and a lot of the light your plant can use to grow more quickly, to fix more carbon, to produce chemicals that we’re looking for. Let’s not shade until we absolutely cannot control the temperature in the space.
CBT: Which greenhouse facility design decisions can impact efficiency?
NS: The first one is the type of cover or glazing on a greenhouse, [which] plays a huge role in how heat enters and leaves that greenhouse, and therefore impacts what type of equipment we want to use, how big that equipment is, how your plants receive light from the sun [and] how heat gets trapped in the greenhouse.
The other thing is make sure you have horizontal airflow fans. These fans are used to create air movement in the greenhouse, and often they’re overlooked for how much energy they use. [With] vertical fans that suck air up and push air down, to get a uniform circulation of air over the crop, you might need 16 of those fans to get full coverage. If you were to use traditional horizontal moving airflow fans, you might need four. There are a lot of options on horizontal airflow fans, and if you pay attention, you can see how many watts per CFM [or cubic feet per minute] of energy these fans use—watts of energy per how much airflow they’re actually pushing. I see too many low-efficiency fans used in this industry. There are good alternatives.
CBT: Which greenhouse facility design decisions can impact yield?
NS: Lighting can impact yield in terms of both the amount of energy (the watts and the micromoles per square meter per second), as well as various spectrums of light. If you just need to extend the daylight hours because you’re in vegetative state and not in a flowering state, using low-energy LEDs to keep the plants vegging can impact your production rates and prevent flowering, but also keep your costs down in terms of operations and energy.
Climate setpoints [are] another big one that can impact yield. There’s more and more evidence coming out that cannabis is similar to tomatoes in that it not only can tolerate high temperatures, but might actually thrive at higher temperatures like 80 or 85 degrees. You’re increasing the metabolic rate of that crop and increasing the rate at which carbon gets fixed, and as long as there’s plenty of water provided to that plant, they’re just going to move fast. Trying to keep temperatures low like in an indoor facility, or [to] keep relative humidity too low because you’re afraid of pathogens, can be very deleterious to yields and production rates.
Sabeh standing outside a greenhouse in Humboldt County, Calif.
The other thing I would say is workflow. How do you move your plants from point A to point B to point C, assuming you’re not growing the full life cycle of the cannabis plant in the same greenhouse, in the same spot in the greenhouse, and you’re moving it from one area to another area as it matures? Is there a special corridor that is enclosed and protected that the plants aren’t going to be exposed to the outside weather, whether that’s extreme heat, say, in Arizona, or extreme cold, say, in Michigan? That will shock the plant, and the plant will go into a survival mode and will shut down a lot of its processes. You might be able to recover that crop, but it might take longer than if you were more gentle in terms of what it’s exposed to.
The other thing is how it’s exposed to other plants in the facility. Again, having an extra corridor or area where you’re moving plants from one area to another as opposed to moving plants through the greenhouse where they might be exposed to a pathogen.
Editor’s note: This article was edited for length and clarity.
Photos courtesy of Nadia Sabeh