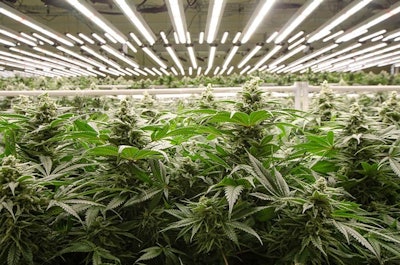
Expanding the canopy at Amplified Farms had been a longtime goal of Zachary Goodin, co-founder and director of cultivation of the Sacramento, California-based cannabis cultivator.
Amplified Farms has the space to grow – the indoor facility is 12,000 square feet. But the challenge had always been the electrical requirements of additional grow lights needed to power such an expansion.
“When we started out, we were using all HPS everywhere,” Goodin says. “We were kind of maxed out on adding more lights in the building.”
It wasn’t until the Sacramento Municipal Utility District (SMUD) reached out to him and other Sacramento-area cannabis companies that he considered using LED lights. SMUD was offering to pay for the equipment for one growing room as part of a study measuring how cultivators could run more energy-efficient operations. Amplified Farms installed Fluence SPYDR Series LED lights, designed for both single and multiple growing tiers, in one of the flowering rooms as part of the trial, converting Amplified’s 1,000 watt HPS lights to 660-watt LEDs, according to SMUD.
“We were kind of excited to work with SMUD and do a research project. [Cannabis cultivators] have been working in the shadows for so long doing the medical market thing that to work with a local utility was kind of exciting. And we actually anticipated going back to HPS lights after the trial was over,” Goodin says. “We just happened to really like the lights. And then when we were able to increase production, it was like a no-brainer after that.”
Goodin and the team at Amplified noted several benefits when they started working with LED lights.
First, the room entirely outfitted with Fluence by OSRAM LEDs “has been our best producing room in the last few years,” Goodin says.
Because LEDs don’t emit as much heat as other cultivation lights, Goodin has also found his HVAC systems don’t have to work as hard to keep conditions comfortable for the plants.
“The HVAC was always having a hard time keeping up. So by pulling some HPS and adding some LED in [the growing rooms,] I can really maintain my temperature. I’m not having as many problems with my mechanical equipment,” he says. “And with taking some of the heat out of our HPS rooms, that’s helped us increase our quality a little bit.”
Amplified Farms has about 50 cultivars it rotates through production, focusing on six to eight at a time, Goodin says, a practice that allows them to individualize the cultivation parameters, including lighting recipes, and increase quality. Although efficiency and yield are important, Amplified prioritizes taste, aroma and potency. Each cultivar has different requirements, Goodin says, adjustments that are possible with LEDs.
“You can dial them into whatever strain you're growing to give that plant specifically what it wants. We have a different dimmer on each row, and we can do a different strain in each row and give the plants more of what they want,” he says. “That's been [the] room that actually performs the best for us. Some strains will have this little bit of pink or this little bit of blue, or a little bit of purple; beautiful hues in the bud that you just don't get quite as much with the HPS. I think you get a little bit nicer aesthetically looking flower.”
But for Goodin, the most important aspect of converting to LEDs has been the ability to expand, thanks to the lower electricity requirements of LEDs. Amplified Farms has continued to add more Fluence LEDs, and by doing so, the cultivator has been able to install an extra growing row in each of its three flowering rooms. The company has also implemented vertical, tiered growing systems, increasing its production footprint. Tiers would not have been possible previously for two reasons, Goodin says – the HPS lights are too hot to work in stacked systems and require too much electricity.
The SMUD study noted that in one flowering cycle, “the LED room saved Amplified Farms 9,407 kwh compared to the HPS room. Ultimately, between the LEDs’ lower power consumption and lower HVAC usage, Amplified Farms realized a 25% savings over their HPS room in both cost and energy.”
Some of the flowering rooms are outfitted with both LED and HPS lights for now as they continue to invest in the technology, but Goodin says plant quality and HVAC efficiency is still improved in the hybrid rooms.
“I’m making the transition to the recreational market, and it has been a big jump,” he says. “Having that extra production has been one of the things that helped us."
For other growers looking to install LED lights, Goodin recommends starting small. Experimenting, dialing in other environmental controls such as HVAC systems and measuring the results has helped them as they have transitioned to using more LEDs.
“See what you're going to need to change. Maybe start with one room and run that for six months. There’s definitely some different environmental changes; you're going to maybe want to run your room a little bit warmer because you're not going to have that extra radiant heat from the HPS light,” he says. Once cultivators are able to adjust their operations, they can then experiment with the light intensity and range that dimmable LEDs provide, which more closely mimics the natural sunlight than other lights Amplified has worked with, he says.
Goodin also recommends working with the lighting manufacturer to make sure cultivators understand how to operate LEDs and get the most out of the technology. He says Fluence has provided Amplified not only with strategic planning and designs from the lighting design department, but also advice on plant production throughout the process of transitioning to LEDs.
“Fluence has been pretty active and been in touch with us the whole time, pretty much ever since we started using their lights. So they've been a really good group to work with,” Goodin says. “We visited their factory [in Austin] and seeing their whole operation … they have a group of people that you could tell they really liked working there, and they want to be a part of something successful and awesome. And you can feel that.”
To read more on the study conducted with Amplified farms and SMUD, click here.