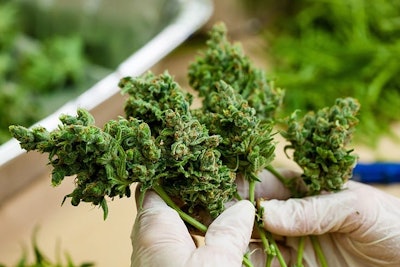
As the cannabis industry expands to a commercial scale, some operators in the market are searching for more efficient alternatives to hand trimming. Cultivators are turning to automated trimming technology to reduce labor costs, increase throughput and improve product consistency. Some machines can even increase an operation’s overall efficiency and improve workflow, although the biggest benefit, according to Josh Evans, head of engineering at Keirton, a provider of professional cannabis and hemp trimmers, is the processing power of today’s technology.
“The biggest challenge is the throughput—the amount of processing that needs to be done,” Evans says. “It typically takes one person a full day to trim one to two pounds of dry flower. … With our equipment, depending on the machine, we can do that in an hour or less than a minute. The biggest thing is just scale of your processing ability. With our large trimmer, T-Zero, we’ve done over 100 pounds an hour, where to do 100 pounds would take over 100 people all day long.”
Consistency is also a challenge when it comes to trimming, he adds. “If you have 100 people doing the trimming, you don’t always get the same output. You don’t get the same consistency in your product. You have one person that doesn’t trim it the same as another person, so you don’t get that consistent look and feel of your flower all the time. When you move over to automation, that’s one of the big benefits, is you can have the same look in every lot and you just continue to do the same process.”
Automating the trimming process can also significantly reduce an operation’s labor costs by decreasing the size of the workforce, Evans says. “If you typically need 100 people to trim 100 pounds in a day, [technology] can do that in an hour with only four or five people. So, if you’re paying an average [of] $25 an hour, that’s going to be a pretty big expense versus the equipment.”
How to Choose the Right Equipment for Your Facility
When selecting an automated trimming solution, cultivators should first determine how much material they need to process per day, Evans says. “You don’t want a massive facility with a small, little machine that can only do 30 pounds an hour. [Understand] your outputs or what your requirements are for processing and [match] the machine up to that.”
Cultivators should assess how many pounds of cannabis they have on site ready for harvest at any given time and purchase a machine that can process that amount of material before it begins to decompose.
“If it’s already dried, it’s not that big of a deal because they can set it aside and slowly process it,” Evans says. “But if it’s wet still and they want to process it wet, they need to make sure they can get it all down before it rots.”
Brand reputation should also be considered, he adds. The manufacturer should have a good track record in the industry and have replacement parts available.
Cultivators should also look for technology with features that further streamline the trimming process, such as machines that have programmable maintenance schedules and “clean-in-place” capabilities.
In the past, cultivators had to pull apart trimming equipment so they could access hard-to-reach places in order to thoroughly clean and sanitize the machine, Evans says. Cleaning equipment by hand can be extremely tedious, he adds, especially in larger-scale operations, as cannabis is very resinous and sticky.
“It’s very difficult to clean, but then once you clean, you have to sanitize,” Evans says. “Cleaning is getting it to the point where it looks clean, and then sanitizing is making sure there’s no bacteria or microbials left on your equipment.”
This is where clean-in-place technology comes in handy.
“Especially in highly regulated areas, … cleaning is a huge part of it,” Evans says. “When you’re processing and you’re up against regulations and making sure that your quality is there, you need to make sure your equipment is clean all the time. What we’re developing and working on is clean-in-place technology, where we hook our trimmer up to a cleaning system and you can essentially push a button and it will clean the trimmer itself.”
The ability to set and save various setpoints on trimming equipment can also be an advantage, he adds. Some machines allow the user to control every motor on the system, from the blades and the tumbler to the conveyors that feed the machine, Evans says.
“If a customer is processing, say, 10 different strains, both wet and dry, and they find certain setpoints that they like for each strain at each different moisture content, then they can save those setpoints as recipes and call on them later,” he says. “They’re not having to go through all the time and remember what setpoints they had for all those individual parts.”
Troubleshooting and repair should also be taken into consideration when purchasing trimming equipment, Evans adds. Keirton, for example, can run remote diagnostics on its machines and can even fix some issues remotely.
“We can log into a user’s machine and change it on the fly, and then they can go back to running it again,” Evans says. “That’s been really important for one of the customers that we have that’s on the other side of the world. They were having a couple challenges, so we were able to log on to their machine in the middle of the night, fix a couple things, and then hand it back over to them.”
How to Implement the Equipment in Your Facility
Once an operation decides to implement trimming technology, it should purchase the equipment well before harvest, Evans says, and ensure it is in good working order before using it the next season.
Ideally, equipment manufacturers work with cultivators to integrate the technology into the facility, Evans adds.
“For the large-scale equipment, what we do for all of our customers is we try to get involved with them from the very start,” he says. “As soon as they know that they’re going to be processing high volumes, we want to start taking a look at their architectural drawings, and then we have conversations with their harvesting manager and their tradespeople that are doing a lot of the work. What we want to do is plan it right from the beginning, as much as we can. We can then take our equipment, lay it out in their facility [and] help define a really good processing path."