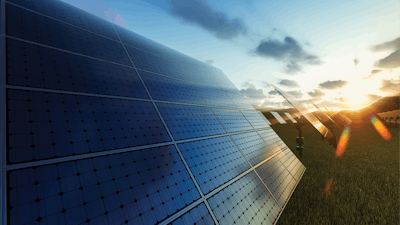
Note: This article has been adapted/expanded from an article “Photovoltaic solar electricity for greenhouses,” which appeared in Greenhouse Management magazine in March 2017.
Will all greenhouses become electricity generators some day? Can solar panels be mounted on the roof of grow room facilities? Photovoltaic (PV) systems with efficiencies of 20 percent (meaning 20 percent of the sunlight can be converted into electricity) are now available at a cost that results in a reasonable payback, but collectors with efficiencies greater than 40 percent are being developed with new materials and manufacturing methods. Systems that can be integrated with production facilities are also being installed. Let’s look at some of the options.
It would take a very large system to provide all the energy needs for a typical greenhouse, but supplying a large percentage of the electricity needs is definitely feasible. First, we need to establish how much power the production system requires. From my analysis in doing energy audits, the typical greenhouse uses between 1 and 2 kilowatt hours of electricity per square foot of floor area per year (kWh/sq. ft.-yr.). To this, you must add the cost of plant lighting.
Electricity Use
If greenhouse conservation measures—such as roof and sidewall vents, wall insulation, energy screens, accurate controls and a boiler system rather than furnaces or unit heaters—are utilized, electricity use is decreased to a minimum. Ventilating fans and hot air furnaces use over ½ kWh/sq. ft.-yr. each if the greenhouse is operated year-round. Vents and boiler systems reduce this by 75 percent or more. Grow room facilities that have plant lighting and air conditioning require considerably more electricity.
Depending on the efficiency of the solar collector, the location of the collector and the area of the country where the facility is located, a PV system will generate from 10 to 35 kWh/sq. ft.-yr. If you operate 10,000 sq. ft. of greenhouse space that uses 1 kWh/sq. ft.-yr. and have a collector system that provides 25 kWh/sq. ft.-yr., you would need at least 27 3-feet by 5-feet solar panels to supply your electricity needs.
Example System Cost and Output
What does a typical system cost? A review of a 60 kW ground-mounted system in Massachusetts installed in 2011 cost about $400,000. (Due to improved efficiencies and lower manufacturing costs, today’s cost for this installation would be less than half.) It consisted of 240 2-feet by 4-feet panels that generate 250 watts each. Much of the funding came from Federal, state and utility grants, and low-cost loans. In five years, this installation generated about 440,000 kWhr of electricity, most of which has been used for the greenhouse/farm stand operation. At the $0.20 electricity rate charged by the local utility, the installation has generated about $88,000 of electricity. It has also saved about 550,000 pounds of carbon dioxide emissions that would have come from utility-generated electricity.
There are two basic types of PV systems: One that stores electricity in batteries and one that connects to the utility power grid. Grid-connected systems are the most common. When excess power is being generated, the grid absorbs this. At night when there is no generation, the grid supplies the needed power. This is net metering. As PV systems supply direct current, it must be converted to alternating current to operate the equipment.
Photovoltaic systems can be ground-mounted, but these take up considerable land area. Another option is to mount them on an adjacent building such as the headhouse or storage building. As most panels are opaque and block light, they cannot be mounted on a greenhouse without blocking light needed for plant growth.
The panels manufactured today are projected to produce electricity for at least 25 years. By that time, continued material development and increased efficiency will warrant replacing them with new units that will have a shorter payback. Maintenance on solar systems is minimal, as the panels are self-cleaning. They’re washed every time it rains, and there are few moving parts.

New Developments
Poly-silicone, thin film materials that allow light through are becoming available. This material can be placed between two layers of glass or plastic, and then used as the glazing on the greenhouse. As it reduces light transmission by about 30 percent, only part of the roof is covered with the PV panels. MaineAsia LLC, along with the Maine Sustainable Agriculture Society, received a grant to utilize this technology with a 6,400-square-foot greenhouse, which has a 14.4 kilowatt total solar power system, and produced enough electricity last year to operate all the mechanical systems on the farm. The technology also provided the capacity for four hours of LED lighting per day in the winter. The panels have also provided beneficial shade during summer months, said Tony Kieffer, MaineAsia’s managing partner.
Another company, Solaria Corp. in Fremont, Calif., has developed photovoltaic modules that alter the light spectrum by converting some of the sunlight to power, with the rest remaining for plant growth. The pink light transmitted increases production while reducing disease problems.
ULMA Agricola in Spain has developed greenhouse-mounted, optical lens-based PV modules that allow light through during cloudy weather and divert it to solar cells when it is sunny.
One area that hasn’t been explored much is making energy/shade screens into solar collectors. When a screen is extended to provide shade, it could provide a large area for collection.
One further development that is being researched is a clear, spray-on PV material that will generate electricity without much reduction in light transmission. This could make all greenhouses electricity generators.
Although the manufacture of solar panels requires considerable energy, the National Renewable Energy Laboratory has determined that the payback is less than four years. To date, there are not many places to recycle used panels that recover the rare metals used. The Silicon Valley Toxics Coalition is leading the way in developing a sustainability standard for panels made in the United States. PV systems help reduce total sulfur dioxide pollution and nitrogen oxide generation by reducing power generation from fossil fuels.
The future looks bright for converting sunlight into electricity. Photovoltaic systems could help to reduce greenhouse operating costs.