
Cannabis extracts are an important part of the rapidly growing marijuana industry, especially in medical markets. The essential oil of cannabis, which is a concentrate of all the active pharmaceutical ingredients in the marijuana plant, is a dynamic substance that can be transformed into numerous forms for user consumption. As a starting point, extracts can be converted (with a bit of basic chemistry know-how) into products such as tinctures, transdermal patches, effervescent tablets, drink powders, suppositories and oral tablets, not to mention the standard vaporizing and dabbing oils.
A variety of suitable solvents is available for extracting the active ingredients from cannabis-each of which has strengths, weaknesses, laboratory infrastructure requirements and production-scaling considerations.This column explores supercritical carbon dioxide extraction (SCCO2), including its functionality, laboratory requirements and what features should be considered during extractor selection.
Medicinal Value
A logical place to begin a conversation about carbon dioxide extraction (or any type of extraction, for that matter) is a quick overview of the medicinally valuable solutes to be extracted from the cannabis plant.
Two classes of cannabis substances receive the most attention in this growing industry: cannabinoids and terpenes.
At least 113 cannabinoids have been isolated, and these molecules range in weight from 250 to 350amu (atomic mass units). Their physical form can be liquid or solid (depending on identity), contain a variety of functional groups and are non-volatile.
Terpenes are a large and diverse group of compounds produced by plants and some animals. This group of molecules is classified by the number of base isoprene units. (Isoprenes are common organic compounds produced by plants.) Furthermore, terpenes and their associated mixtures are responsible for the pleasant-or unpleasant-aromas given off by plants. Terpenes vary widely in mass based on the number of carbon atoms (or isoprene units), can include a variety of functional groups and are physically liquid or oil.
Flavonoids and carotenoids are also present in cannabis. While they are not frequently recognized as valuable in the cannabis industry, they are well-known bio-botanical compounds in the nutritional and medical industries. Flavonoids are polyphenolic compounds that give plant extracts their golden and brown colors. There are more than 5,000 known flavonoids that vary in molecular weight and numbers of functional groups. They are usually solid in their pure form.
Carotenoids are a group of pharmaceutically important molecules with more than 600 known constituents. They tend to be of very high molecular weight, contain a variety of functional groups and are orange to red in color.
Finally, numerous fatty acids and chlorophylls can be extracted from plant material. Though they are not generally thought of as medicinally valuable in the cannabis industry, some evidence exists for bioactivity in the nutraceutical industry. Fatty acids are commonly 16 to 20 carbons long, but can be much larger; they tend to solidify at room temperature, and the level of saturation (i.e., number of hydrogen-carbon bonds) can vary.
Chlorophylls are the large molecules responsible for a plant’s ability to produce sugars from sunlight and water. Chlorophylls range between 800 and 900amu and give plant extracts their green to black coloration. (Black coloring occurs when chlorophyll is oxidized.)
_fmt.png?auto=format%2Ccompress&fit=max&q=70&w=400)
The CO2 Process
Now that we have covered the majority of the extractable solutes in cannabis, let’s explore how carbon dioxide functions as a solvent.
Before diving in, a quick review of some relevant physical properties of carbon dioxide can be helpful. Carbon dioxide is a gas at standard temperatures and pressure. It forms a liquid at pressures above 5bar (i.e., 73psi), and its critical point (the vapor-liquid boundary) is 73bar (1060psi) at 33.1 degrees Celsius.
Here, we’ll describe the solvent properties of carbon dioxide in its supercritical state-because the gas state cannot act as a solvent, and the liquid state is not an efficient solvent in cannabinoid extraction.
So, what features of supercritical carbon dioxide (SCCO2) make it an efficacious solvent in the extraction of cannabis? Supercritical carbon dioxide-and all supercritical fluids-have the density of a liquid, diffusivity of a gas and a low viscosity (thickness). In simpler terms, this means that SCCO2 has: a high-solute carrying capacity (i.e., it can hold a lot of material), the ability to penetrate into the smallest spaces (like a gas) and very little flow resistance. Additionally, its polarity and density can be manipulated. Polar manipulation can be achieved with the addition of co-solvents, such as ethanol. Density manipulation is the true power of supercritical carbon dioxide as a solvent. While other solvents such as hydrocarbons and ethanol are more efficient at stripping plant material of their cannabinoids and terpenes, SCCO2 has the unique ability to target specific fractions in the parent (plant) material or separate solutes. Those processes are possible because SCCO2 density is dependent on pressure and temperature parameters.
Solute-carbon dioxide interactions are solute-specific. Each solute in a mixture (i.e., the parent plant material) has a unique solubility profile that is related to the density of the SCCO2; a density exists where specific solutes become highly soluble in SCCO2. This is called the crossover phenomenon. It is characterized by an exponential increase in a solute’s solubility in SCCO2. Because the crossover point is solute-specific-if the critical density is known for target solutes, they can be individually removed by using temperature and pressure gradients.
We can also view this crossover phenomenon from a different perspective: Imagine using temperature and pressure settings that result in the extraction of all solutes from your feed material, then reducing density downstream of the extraction location. This process is called retrograde solubility and can be taken advantage of to separate the components of the SCCO2/solute mixture.
Essentially, this process starts with SCCO2 at a very high density, followed by sequential depressurizations that result in consistent reductions in SCCO2 density throughout that process. As this process is occurring, certain solutes are no longer soluble and are collected at specific locations (i.e., separation vessels).
That ability to target or separate solutes from a mixture is the most valuable feature of SCCO2 extraction. Other beneficial features of carbon dioxide extractions include the fact that it is generally regarded as safe (i.e., high exposure limits), it is relatively cheap, and it is available in high purity from numerous sources.
CO2 System Considerations
So, what are the important features of a supercritical carbon dioxide extraction system? As previously mentioned, density, which is determined by pressure and heat, is one physical property of SCCO2 that dictates extraction efficiency and separation. Therefore, three variables are of the utmost importance:
- maximum pressure rating
- the ability to measure the temperature of the carbon dioxide (not the surface of the vessels) and
- high wattage heaters.
Those features are important because it is necessary to obtain high pressures, deliver the heat in an efficient manner and have a real-time knowledge of carbon dioxide temperatures to tailor the density appropriately.
An extractor also should have a pump/flow monitoring system that evaluates the mass of carbon dioxide being delivered to the extraction vessel. Additionally, that pump should have the ability to deliver high flow rates to the parent material in the extraction vessel. This is because an important calculated variable to optimizing a supercritical carbon dioxide extractor is the ratio of carbon dioxide mass used during extraction to the mass of the parent material-a ratio of 50 or more is usually necessary to reach 90-percent to 95-percent extraction completeness.
Finally, separation vessels with high maximum-pressure ratings are extremely important because they give the technician the ability to use a variety of pressures in the development of separation (i.e., product development) protocols.
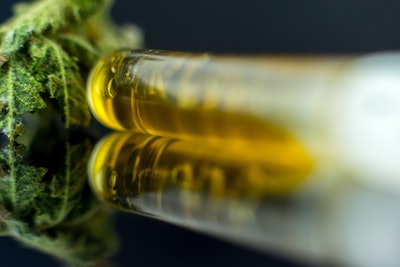
A shortcoming of SCCO2 extraction is that numerous waxes and fatty acids are also soluble in supercritical carbon dioxide. From a manufacturing perspective, this is an important point because those materials need to be removed during the refinement process before product development. This is achieved through a process called winterization, which takes advantage of the differing solubility of waxes and cannabinoids in a solvent at low temperatures (i.e., -30 degrees Celsius or lower).
The winterization process frequently represents the slowest part of the refinement process if the infrastructure does not match the extractor production rate. The standard protocol uses a funnel and filter paper in concert with a vacuum. Depending on volume, this process can take between four and eight hours. Furthermore, it must be repeated multiple times to account for the dissolution of waxes back into ethanol during the protracted filtering process. However, the redundancy and length of this process can be circumvented through the use of low-pressure cartridge filter techniques that can process large volumes of winterized material in an expeditious manner while controlling temperature.
The next consideration is the solvent recovery that follows the winterization process. It is important to size your solvent recovery units to match your winterizing/filtering production rates. Most commonly, rotary evaporation systems are used to recover your winterizing solvent. It is also important to scale this system to match your pre-solvent recovery step production and extraction rates.
To put these notes in perspective, here is an example of a production system followed by an identification of the bottleneck.
First, it is necessary to lay out the assumptions:
- extractor input of 2,000 grams
- return ratio 0.18
- two extractions per day
- five days a week run time.
With those assumptions, the output per run is 360 grams per day and 3,600 grams a week. Therefore, the total volume of material to be filtered would be 36 liters with a 10:1 ratio of winterization solvent to extract.
That material can be filtered in 34 minutes with a positive-pressure filtration system capable of an aqueous flow of 125 liters per hour and an equal volume of solvent to wash the waxes. The final volume for solvent recovery is 72 liters, which can be recovered in four and a half hours with a rotary evaporator capable of processing 16 liters per hour. Evaluating these numbers suggests that your post-processing equipment is capable of refining a week’s worth of extract in roughly five hours. Therefore, your extraction parameters or the extractor are the bottleneck in the described production system.
While this analysis oversimplifies the process in some ways, it does exemplify the importance of planning your total production system to meet the output at each stage because capital might be better leveraged to obtain a system with a higher overall output. Imbalanced systems can cause manufacturing equipment to lay idle for periods of time, which is not an optimal use of capital, labor or equipment.