Many years ago, in an article in Greenhouse Management magazine entitled “Efficiency Equals Savings,” I read: “150 employees saving 5 minutes per day at $6 per hour means $25,000 a year in savings.” Even back then, this resonated with me.
As with any business, your efficiency determines your profit margin, which in turn dictates your business’s success or failure. Efficiency can be applied to cannabis cultivation, processing and extraction in many ways, such as creating a proactive environment rather than a reactive situation. Being proactive allows the grower time to pay extra attention to the many small details required to produce top-quality cannabis.
Efficiency Does Not Mean Cutting Corners
Cannabis is swiftly becoming a commodity product, and the increased availability of state-legal cannabis will lower wholesale prices, making it difficult for growers to stay competitive and profitable. Therefore, intelligent growers must be mindful of their initial start-up costs and pay attention to the cost of production, from growth method, drying and curing to fresh, frozen extraction. All must incorporate lean manufacturing practices, defined as a systematic method to eliminate waste in the manufacturing process.
Lean manufacturing is a management philosophy derived primarily from the Toyota Production System — the essence of which is credited to Dr. W. Edwards Deming, an engineer and management consultant considered to be the father of the quality evolution — combined with QC, or quality control. ISO 9000, one of the most widely used quality-management standards, defines quality control as "a part of management focused on fulfilling quality requirements.”
Both lean manufacturing and quality control must be adopted into any large-scale cannabis production facility. That said, regardless whether the grower is utilizing an indoor warehouse or a purpose-built greenhouse, the questions remain the same: What is the most efficient method for delivering the best crop or product? And how do you achieve efficiency?
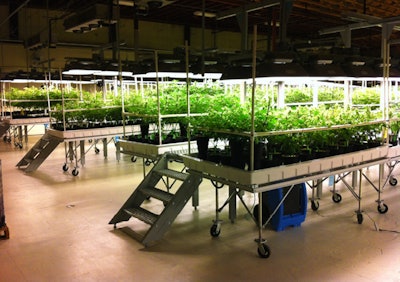
Planning for Efficiency
Efficiency needs to be planned for and incorporated into your facility from the beginning. Cannabis-specific, purpose-built, high-tech green houses will be the industry’s future. They afford the lowest cost of production, and cannabis does very well in greenhouses. But you must incorporate lean processes by using various mechanized technologies to create an efficient workflow:
- Proper staging/work areas need mechanized potting machines, conveyor belts to get the plants to desired areas, and moving or rolling aisles that allow maximum access to plants without sacrificing valuable floor space.
- Walkie-talkies or another form of communication between employees and management must be utilized to eliminate wasted time walking around looking for workers, tools or information, or to inform the front office when something is out of stock and needs to be ordered.
- Inventory tracking is a must, as well. Sending an employee to the store all the time for materials is inefficient. It is best to anticipate when a necessary item will be out of stock, order it and have it delivered whenever possible.
- Growers must consider small details such as lunchtimes: How much are you willing to pay to decontaminate every employee two times a day—once every morning and once upon returning from lunch if they left the facility? To do so equals 10 minutes every day per employee, and surely they are making more than $6 per hour. It may be best to provide a comfortable lunch room and encourage employees not to go out to lunch, or better yet, to provide lunch for them.
- Energy consumption is pivotal. The more energy you can save, the lower the production cost. Always look for ways to conserve energy. Geographic location will dictate your production cost to some degree, as heating and cooling costs are large expenses in both warehouse and greenhouse production. (Editor’s Note: For more on energy conservation, read “20 Ways to Cut Energy Use,” from CBT’s November issue, available on CannabisBusinessTimes.com.)
- Efficient supplemental lighting and light-deprivation methods must be employed in greenhouses. And indoor facilities must utilize correct lighting for each growth stage and cultivation method. Induction and LED lights work great for vegetative growth with minimum energy consumption and don't produce excessive, unnecessary heat. Compact fluorescents should be utilized for cloning purposes. Efficient, double-ended, high-intensity discharge (HID) lamps or plasma lighting should be used for the flowering stage.
- High-tech irrigation is rapidly becoming the environmentally correct thing to do and will be a requirement in the future. Choose an irrigation method that is efficient, effective and environmentally sustainable. Choose a system not only with upfront costs in mind, but also with the system’s maintenance in mind. If an irrigation system costs less up front, but frequently clogs or requires excessive maintenance, it ultimately becomes a detriment that costs more than you initially saved.
- Build large clone rooms, not lots of little grow trays with domes on top. It is much more efficient to turn a whole room into a purpose-built clone room. The labor it takes to attend to many little clone environments can waste many hours.
All these little things may seem trivial, but just as with any other business, time is money, and it all adds up rapidly. There is more to cannabis production than there is to growing vegetables or ornamental flowers, which can be harvested and sent direct to the market.
Cannabis is typically dried and cured after harvest. It needs to be attended to immediately. It must dry completely and uniformly, as well as cure properly before it goes to market. It should be produced in a line or U-shaped fashion, meaning materials enter one end, and waste by-product and desirable products exit the opposite end. This also aids in avoiding contamination with pests and disease.
When the top-grade buds/flowers are completely ripe and ready to harvest, the best 10-percent of each plant can be hand-trimmed and cured for sale. These are the tops of the plants and tips of the branches.
More Efficiencies: Concentrates and Compounds
With current trends heading toward concentrated forms of cannabis and super-refined compounds, large-scale producers must think toward the future when designing their facilities, not only for cultivation, but for processing and extraction as well. The large-scale commercial cultivator will eventually calculate yearly output measured in milligrams of cannabinoids and milliliters of terpenoids, and how much it costs to produce them.
To achieve the most efficient cost of production, the growth method requires that large apical buds be bent and trained sideways, so the shoot/branch produces buds the size of ping-pong balls, not huge buds that have to be broken down by hand, which is time-consuming. It’s best to produce lots of medium-sized buds/flowers whenever possible.
When the top-grade buds/flowers are completely ripe and ready to harvest, the best 10 percent of each plant can be hand-trimmed and cured for sale. This is the tops of the plants and tips of the branches, which received maximum light. The remaining 90 percent of each plant is left to ripen and receive maximum light for approximately two more weeks.
These plants do not necessarily produce a top-grade for the shelf as flowers, but ripening the remaining 90 percent of the plant increases the essential oils/terpenoids and cannabinoid content by as much as 25 percent. This makes it possible to eliminate one growth cycle per year, going from five growth cycles annually to four, while still producing the same amount of desirable compounds. Eliminating one growth cycle, yet producing the same amount of product, saves hundreds of thousands of dollars on a large scale, and not manicuring and curing the remaining, ripened 90-percent can save millions. One of my clients spends $1.2 to $2 million per year hand-trimming their cannabis.
This growth method also results in further substantial savings in construction costs and space allocation for drying and curing only 10 percent of the product, not to mention labor costs to perform this function. Instead of drying and curing the ripened 90 percent, these plants can be de-leafed of any primary and secondary leaves that do not show desirable attributes (visible resin glands/trichomes).
The un-dried buds/flowers can then be trimmed off the branches and immediately frozen in a subzero cryogenic freezer. This method allows for maximum terpenoid preservation. The simple act of drying cannabis evaporates many valuable terpenes, so by fresh-freezing the cannabis, the extracts retain the maximum terpene content. The frozen plant material will first be extracted utilizing hydrocarbon or solvent extraction methods, which separates all lighter volatile oils/terpenoids and a large amount of cannabinoids.
After solvent extraction, extracted plant material is dried, then a CO2 extractor is used to extract and collect any remaining cannabinoids in the plant material. The resulting extracts are terpene-rich from the first stage and primarily cannabinoid rich from the second stage. This ensures that all available desirable compounds are extracted as efficiently as possible and that the resulting compounds are in their most desirable forms. These can then be used as whole compositions in vape pens or in edible products, or refined into separated compounds for use in pharmaceutical or wellness products and research.
Basically, by employing these methods, the process is streamlined. The time saved by eliminating waste and inefficiency can be focused on producing superior plants and products. Simply put, good cannabis makes good extracts, and good extracts make good products. And doing both efficiently and with the lowest cost of production allows for production of a superior product at a competitive price, which is the name of the game in any industry.
All of this relates to the large-scale grower, but in essence, can be applied to small/boutique growers, as well, in that it all contributes to your bottom. Large-scale producers will ultimately produce top-quality extracts, using only the best 10 percent of dry buds/flowers; these will be mass-market products, similar to a leading brand name beer/brewery. Yet there also will be huge market potential for the boutique growers, who could be compared to today's craft breweries.
Envisioning a Two-Tier System for Cannabis
A two-tier system—mass-market and boutique—seems inevitable. But even the boutique grower must be mindful of efficiency and cost of production to be competitive against mass-market producers. There is room for both, as proven by the proliferation and explosion of craft breweries.
Keep in mind, however, that many craft breweries are being merged with or acquired by mass-market producers. The only way such a merger or acquisition becomes possible is that the craft brewery efficiently produced a quality product and demonstrated profitability by providing a superior product at an affordable price.
Whatever the producer’s path, cannabis production can't be done inefficiently any longer.
A company I consulted with in Israel produced top-quality cannabis in greenhouses for Israel’s Ministry of Health with the production cost of $0.50 per gram. It only makes sense that a high-tech purpose-built greenhouse can produce cannabis for $0.25 a gram. If that product is then refined for $0.03 a gram, you end up with high-quality terpene-rich vape pens for sale for $5 retail (or whatever price you determine) per 1 gram cartridge. This will make it very hard for the average producer to compete in that market.
Superior growers, breeders and processors will inevitably flourish, but only if they stay relevant and competitively priced. There will always be a demand for the best product possible, as proven by the high-end liquor market. But the customer must receive what they pay for, and growers must strive to always exceed customer expectations.
About the Author: Kenneth Morrow is an author and writer who has been covering cannabis-related subjects for more than 20 years. He is the owner of Trichome Technologies, a cannabis research and development company. Morrow also is an award-winning grower and breeder. He has made contributions to many of today's extraction methodologies, and he holds multiple patents in the field. He currently specializes in product formulation and consults on all cannabis-related subjects.