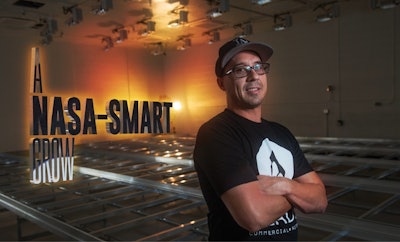
David Holmes was no stranger to cannabis, and saw his first plant, in an uncle’s California garden, when he was just nine. But when he saw his first indoor cultivation site while in college, he says, “It just blew me away, and I immediately told myself, ‘I really would love to try doing this.’” Upon graduation, he set up his first indoor grow and “it just expanded from there,” he says. After growing for California collectives for years, Holmes established and serves as CEO of Clade9, a full-service cannabis-cultivation business that designs, builds and manages cultivation, as well as sells a nutrient line. The company currently has an exclusive contract (where they can't manage other grows in Arizona) with Herbal Wellness (a cultivator with a 30,000-square-foot facility in Phoenix), and it manages an 18,000-square-foot site in Las Vegas. In the past six years, Clade9 has helped more than 50 facilities/cultivation projects get off the ground. Clade9 also operates its own cultivation facility in California, and the company has become a respected name in modern cultivation.
This issue’s Guest Interviewer, interviewing Holmes, is the legendary Mel Frank, who likely will need no introduction — but if you aren’t familiar with him, you should be. In addition to having nearly five decades of cannabis cultivation experience, Frank is an internationally recognized book author and contributor to many cannabis-based magazines. But he is perhaps most well-known for his 1977 “Marijuana Grower's Guide Deluxe,” which he co-authored with Ed Rosenthal. “Deluxe” distilled what was scientifically known about cannabis and brought the reality of home growing anywhere, indoors or out, into public awareness.
By the late 1970s, Frank managed a collection of more than 200 marijuana landraces, which he bred and hybridized for increased potency and earlier harvesting, so that growers in colder, short-season areas could grow fully matured, high-quality cannabis. He was even asked by the U.S. Government in 1977 to donate premium landraces to the government’s marijuana research program at the University of Mississippi in Oxford. He donated nine diverse landraces with seeds and samples for research.
Frank also donated two strains he developed, Afghani1 and Durban Poison, which, along with Haze, Hindu Kush and Skunk #1 from other California breeders, became the basis for Amsterdam's commercial seed industry.
In this momentous interview, Frank talks in-depth with Holmes about his earliest grows, his latest two-phase build-out of the above-mentioned Nevada facility, how his mathmatics backdground and a stint at Nasa’s Jet Propulsion Laboratory have helped him with research, data collection and the development of his proprietary Holmes Matrix used in breeding … and more.
Mel Frank: How many and what kind of lights did you have for your first indoor grow?
David Holmes: I think I had one 1,000-watt lamp with reflector, and I hung it in my girlfriend's … garage. [Laughs] And it just expanded. So I went to two 1,000-watt lights, to four, and then eventually … around 40. It incrementally increased over several years.
Frank: You must have been building these for collectives, after Proposition 215 passed in 1996, because the collectives were legal then, right? You weren't building 40-watt light grows for yourself, for sure.
Holmes: [Laughs.] Exactly. ... As the cultivation sizes increased, I started to team up with collectives. We formed a nonprofit, and it was all legal and regulated within California — as regulated and legal as California could be. ...
Frank: So, you were growing from the time you finished college. What was your major?
Holmes: I have a Master’s in math, believe it or not.
Frank: Did you use that or just start growing?
Holmes: ... The mathematics background has been very beneficial. The critical thinking and the problem solving you have to do in math — and pure math especially – lends itself very well to cultivation design and research.
... One of the things that has made me very successful in these cultivation designs is the research and data I've collected, and the experiments I've created.
Frank: When did you start doing experiments?
Holmes: During my first cultivation I would collect data, and as they scaled up, I did more experiments. But one of the first true experiments I did … was with UVB in an indoor cultivation. We were trying to see if UV radiation would stimulate the plant to create either more cannabinoids or more terpenes.
Frank: Who did the testing for you then?
Holmes: The testing was all done by The Werc Shop lab – this had to be around 2010-2011. They were very generous, not only by not charging for testing, but also by participating in the sampling process.
Frank: Yes, Werc has been in the forefront for testing and trying to educate and professionalize the industry. ... Now, the mathematical input here is kind of fascinating. How else has that helped you?
Holmes: ... One specific thing it really helped me create was [with] plant breeding, which ... is one of my favorite things in cannabis cultivation. I developed, using math, what I called the "Holmes Matrix." I don't want to say too much about what it does because it's proprietary, but, basically, it’s a mathematical tool to help aid breeding. ... For cultivation, the name of the game is efficiency, and increasing yields and quality, and you really can't do that without data and data analysis.
I actually had a research stint at the Jet Propulsion Laboratory (JPL) a couple years ago, and that really pushed the research even further because I was forced to learn a programming language called MATLAB [laughs]. And the MATLAB really helped in setting up some of these experiments, including the Holmes Matrix.
Frank: So that was just an opportunity that came up? I mean, working for JPL, it must have been [laughs] pretty interesting, right?
Holmes: I … was a part-time math professor for many years ... so the opportunity came out of that.
Frank: Was work at JPL part of the Space Program?
Holmes: We were calibrating a camera that would be mounted on a telescope that searched for extra-solar planets.
Frank: Amazing! Now, after building these grows for the collectives, how did Clade9 begin to do business out of state?
Holmes: A friend of mine in the industry introduced me to a group from Arizona. They were having trouble designing their facility and were trying to find professional cultivators.
So ... we had a couple meetings, I met their first cultivator, and I [gave] them pointers and design advice. ... They showed me a really inefficient cultivation design that was 10 years outdated. So I pushed on them that they were going to lose tons of money if they did it this way. And, luckily, they agreed and scrapped the design. We just built it up my way.
Frank: Who was this?
Holmes: The dispensary and cultivation [operation] is Herbal Wellness, in Phoenix.Ever since our cultivation produced, about a year and a half ago, they've done really well. They were on the Leafly list as the No. 1 rated dispensary in the nation last year.
Frank: So what did you build for them?
Holmes: We parsed their 30,000-square-foot warehouse out into three phases. We built out Phase One, which is about 160 lights. It’s about a quarter of the facility. Phase Two is under construction now, which adds another 200 lights, and that should be done in the next couple weeks.
Frank: What was the Phase One build-out?
Holmes: We built it out as a perpetual harvest. We have five flowering rooms, a mother room and a veg room – pretty standard – and … the ownership had a specific budget, so we designed it … as a very basic ... cultivation design that fit within their budget.
We even used … these $12, 1,000-watt bulbs to make sure we stayed on budget, and even then, we did very good work on harvesting and efficiency. Our first harvest was about 1.7 pounds per light, and we've incrementally increased to about 2.2 pounds. Flowering rooms are staggered in development, so one is harvested every two weeks.
Frank: And was that just a standard, four-by-eight trays in aisles kind of a setup?
Holmes: Yeah. It was your standard – each reflector covering a 4-foot by 4-foot space, and we have 9- or 10-foot ceilings.
Because they were able to start making money on Phase One with the cultivation, Phase Two is much more ... like a grow room 2.0, which is next-level technology.
Frank: What’s the difference between how Phase Two and Phase One are configured?
Holmes: Phase Two takes into consideration all the greenhouse tech that's coming into the industry, which is really the trend right now in indoor cultivation — increasing efficiency using things like rolling benches, 12-foot ceilings and Gavita lighting (which have a larger footprint), and using fertigation (a greenhouse-style irrigation system that's completely automated). Also, they'll be harvesting a room every week from this build, instead of every two weeks like the first one.
Frank: So you got better bulbs. You don't have as many aisles now. You probably have one aisle per room, right?
Holmes: Basically. The name of the game is … increasing the canopy size in the rooms and making the lighting uniform. In indoor cultivation, the key is obviously the genetics, plant nutrition and environmental control.
Frank: All aspects of atmosphere control are incredibly important. So you're using AC and dehumidifiers. Are you filtering air coming in?
Holmes: Yeah. I think, also, as the industry evolves, one of the things people have to start paying close attention to is the state testing. In Nevada, the state is requiring testing of every batch, and every batch has to pass testing for heavy metals, fungicides, pesticides, bacteria; so when you design a grow room nowadays, you really have to consider that. Even in California, we still don't have any regulations, but in two years, three years, those regulations are going to come down. I'm assuming they're going to be very strict.
So if you have a grow room that's built now, without the clean room protocols ..., you're going to be in trouble. In our Vegas facility, which will be complete in about three weeks, we're going to have all of those protocols to ensure that we pass state testing.
Frank: These places also need cleanliness in terms of the workforce. ... So you have to have a change of uniform, footwear, things like that, so you're not bringing in pests, or funguses, or whatever.
Holmes: No question about it. You walk on your lawn, you bring in spider mites, or you've been to another facility and bring broad mites into a 40,000-square-foot facility, and it's over.
... We instill a clean-room protocol now, where you walk in and dip your feet in a bleach solution. Then you have to put on different shoes and basically a space suit — gloves, mask, hair net, everything. Then you can enter the facility.
You really have to treat it as a clean room you'd design for a space ship going to Mars. … Because a spore of powdery mildew could cost the investor tens of millions of dollars.
Frank: Right, because once it's infected, you have to close it down and disinfect, and then you're months away from your next harvest. A lot of newbie investors don't seem to realize how devastating it can be.
Holmes: Very devastating, very expensive.
Frank: How many people work at Herbal Wellness?
Holmes: Besides cultivation, it's also extraction and edibles. They have a dispensary, so there's packaging and lots of other aspects of the facility. They have around 30 employees just at the warehouse.
Frank: These aren't your employees, right? How many employees does Clade9 provide?
Holmes: We only have one official Clade9 employee on site. When we do a cultivation facility, part of what we do is design the protocols and management, get plants in the ground, growing and cultivating, and then train them and get them used to the system over the next year and a half, and this particular individual works with the grow teams day-to-day, overseeing the cultivation.
Frank: I know you have a huge arsenal of genetics back there. You're crossing various things and trying to develop one strong with terpenes and different cannabinoids, that sort of thing, right?
Holmes: I do a lot of breeding, and the way I do it, I think, is a lot more technical than most. I go beyond just a traditional plant breeding. We’re using Punnett squares and breeding technology, and tons of lab testing.
So, typically, every time we finish a round of phenotypes we've created, we take maybe the top 20 or 30 — and have them lab tested for cannabinoids and terpenes.
Then we ... have as many connoisseurs as we know smoke and give feedback. ... The lab testing and terpene analysis only tell you so much. So many other factors determine if a strain is going to be popular or not, and the smoking effect is a huge part of that.
Frank: You mentioned Las Vegas. ... Tell us about the approach you've done there.
Holmes: ... One of the biggest trends I mentioned earlier is a lot of greenhouse technology coming into indoor cultivation. In Big Ag [agriculture], they've been doing this for decades and haven't had to worry about being raided by police, so they could put a lot of resources into these facilities and designs, and have professionals look at things. Now that the [cannabis] industry is gaining credibility, that's what's happening. So we brought a lot of that greenhouse tech indoors into Vegas, and also took into consideration that we had to be very, very clean.
Frank: What filtration system do you use?
Holmes: For odor, we're using your standard carbon scrubbing with an ozone generation that's vented out of the facility. And then, there's also a technology called AiroCide, that we're going to be employing, which was, I think, originally developed by NASA to stop fruit from spoiling on the space station. So we hope it would eliminate a lot of the pathogens.
Frank: Was odor control one of Las Vegas's stipulations?
Holmes: It was, and it varied by the municipality. But, we decided that it's going to be better for the neighbors anyway. That's definitely one thing I learned about being in California: happy neighbors, happy life. [Laughs]
Frank: In Vegas, the heat is obviously a huge concern and expense. So what are you using to control the atmosphere?
Holmes: ... In Vegas, we just had to install more HVAC. We're using a VRV [Variant Refrigerant Volume] HVAC system, which I think was initially developed for server room technology. It does a lot of things we need to do for indoor cannabis cultivation — cooling a room that has a lot of heat-generating technology, and keeping the room's humidity in check.
Frank: And then, of course, you're doing CO2 supplementation?
Holmes: Yes. It's all going to be a tank system, so one of the great things about being in a regulated state is that ... you could just hire a company like Airgas, to put a huge CO2 tank on the side of your facility and, just like the Sparkletts [bottled water] guy, they come and change out your gas every two weeks.
Frank: You're doing hydro in Vegas. What medium and kind of system are you using?
Holmes: We're, using rockwool drain-to-waste – on tables, basically. ... We're going to use six-inch rockwool cubes, on tables, for the flowering rooms. And our mothers are going to be in coco pots, maybe three- to five-gallon.
Frank: How often do you flood the rockwool?
Holmes: I've always been a fan of feeding rockwool more than less, so, anywhere from six to eight feedings a day.
Frank: If you miss a feeding with rockwool, it dries out so quickly you can lose your plants.
Holmes: Definitely. It’s a very unforgiving grow medium, but it’s also very clean, and it fits the clean-room environment very well. In indoor facilities, hydroponic is the safest way to go.
Frank: It's certainly the most controllable. ... I imagine after all this time you've been growing, you've probably tried just about every indoor light source? I have never used plasma lighting, but I think I've used all the rest of them — the LEDs, the fluorescents, and now I've even been doing ceramic bulbs. Have you tried those yet?
Holmes: I haven't. It's something I really want to experiment with. We've done testing mainly on HIDs [high-intensity discharge], obviously single-ended and double-ended bulbs. We've done testing with fluorescent lighting, T5s, and with LEDs.
Frank: Do you use the T5s for your mothers?
Holmes: Yes ... and our clones.
Frank: So, what about the future here? How do you think this is all going to work out?
Holmes: The data shows that extraction is getting more popular, and extraction is easier to make a consistent product, so obviously the future is extraction, probably things like vape pens and edibles.
And indoor cultivation is expensive and takes a lot of power. There are a lot of upfront costs, and obvioulsy outdoor and greenhouse are cheaper. ...
But, I think, still – because of the environmental control you have indoors for really high-grade, connoisseur flower, I don't think indoor will [go away]. …
Frank: I tend to agree with you. I think the indoor product will be around forever. It's just a matter of how large a piece of the pie it's going to have.
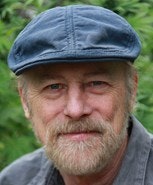
About the Interviewer:Mel Frank has been writing about cannabis since 1971. He has co-authored and authored three internationally known and translated books on cannabis cultivation, and in 1988, he founded Red Eye Press, publishing his “Marijuana Grower's Insider's Guide” as well as updated versions of the “Marijuana Grower's Guide Deluxe.” He also edited and published Rob Clarke's “Hashish!” in 1998, which revolutionized hashish-making worldwide.
His photographs have been made into posters, calendars and trading cards, and reproduced as art, and hundreds have appeared in books by Rob Clarke, Ken Morrow, Ed Rosenthal and Jorge Cervantes.
He has lectured at Oaksterdam University and judged numerous cannabis competitions in the United States and the Netherlands. He currently collaborates with a network of cannabis researchers, works as a consultant and is the senior advisor to several California-based marijuana companies.