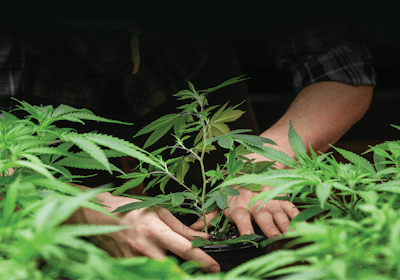
The legal cannabis industry is at a crossroads. With mainstream approval growing, legal hurdles are being cleared in state after state, paving the way for an inevitable legalization of medical cannabis on the national level. With the increased exposure from rapid growth, the industry inevitably will attract more scrutiny from OSHA, the Federal Occupational Safety and Health Administration. Ultimately, this is an industry just like any other. Cannabis cultivators and distributors are responsible for providing their employees with a safe and healthful work environment, and you would be well-advised to address safety before OSHA regulations come crashing down on your business.
OSHA created the Federal Safety Standards in 1970. New businesses and industries do not have the luxury of not knowing about Safety and Health laws. In August, OSHA will be raising penalties for violations — which has not happened since 1990 — and they are expected to rise by 80 percent per citation. Currently, a serious citation holds a $7,000 penalty. This is expected to rise to $12,500 under the new structure. On top of that, OSHA will be allowed to adjust its penalty levels based on inflation going forward. This is unprecedented and will affect all industries, including the seedling that is the legal marijuana industry.
The stakes are high, and with the nation steadily moving toward legalization, now is the time for the legal cannabis industry to get ahead of regulators and make safety a top priority. By creating a safe work space for employees, employers are protecting their businesses and their employees.
We are not experts in the cannabis industry. We are experts in OSHA regulations and Loss Control, which is a constant across all industries. We have found that regardless of the industry you are in, a comprehensive written safety program is the foundation for a safe workplace. Not only is the written program required by OSHA, but when used correctly, it prevents and reduces work-related injuries. Insurance companies, too, are requiring comprehensive written safety programs, tying them to lower rates.
While the amount of information the employer is required to know in order to be compliant can be daunting, four components should be covered in your safety program to avoid a citation and provide the required safe workplace:
- A Comprehensive Written Safety Program
- Employee Training
- Accountability
- Safety Auditing
Written Safety Program
A written safety program is the manual for your company’s safety policies and procedures. It should identify all aspects of your operations and the hazards associated with each procedure, and implement control measures to eliminate those hazards. It should cover such things as employee and management safety responsibilities, incident reporting and response, emergency action plans, disciplinary action, workplace violence and harassment, vehicle safety, proper use of tools and equipment, electrical safety, Personal Protective Equipment and any applicable hazardous materials.
OSHA requires specific written procedures for safety specific to any hazardous materials in your operations. These must include training for those materials and chemicals, and include the Safety Data Sheets and corresponding information.
Employee Training
Employee training is another OSHA requirement. Train your employees on rules and safety procedures and requirements, and in the proper use of tools. Document the training, and have your employees sign off on it.
Safety training not only cuts down on workplace injuries, but also protects you, the employer. OSHA accepts, as training, in-house safety meetings that go over safety requirements with employees, as long as the required topics are covered per OSHA regulations.
Accountability
A working safety program needs a component of accountability, through written warnings and disciplinary action for safety infractions. If your safety program is unenforceable, it has already failed. The purpose of disciplinary action isn’t to punish; it’s to hold employees accountable. Your disciplinary actions should be written into the safety program, and employees should be trained on what is expected.
Retraining is an effective form of disciplinary action. As with training, disciplinary actions must be documented, whether for minor infractions or serious violations. In the case of an OSHA citation, disciplinary-action records are one of the first things OSHA will ask for. Remember, you are protecting employees and your company. A rise in injuries will result in a rise in insurance rates. A company with numerous injuries will not stay in business long.
Safety Auditing
One of the most effective tools in preventing injuries and avoiding OSHA violations is conducting regular safety audits. Observe your operations. Identify areas in need of improvement, and take corrective action. Are your employees following the proper safety procedures and wearing the required personal protective equipment? Are machines, tools and chemicals being used per the manufacturer’s specifications? Do your employees have the appropriate training for operations they are performing (such as applying pesticides)?
Safety audits should be documented, too, and along with the corresponding corrective actions, provides you with an ongoing record of your safety program in action.
As the marijuana industry becomes more and more mainstream, companies must lead by example, including on employee safety. Investing in a safe workplace protects the employees, your company and the industry.

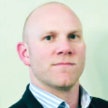